Special Effects Automation Kit¶
The special materials for the course include a rapid-prototyping kit of laser-cut wood parts and standard mechanical components. This is intended to ease building articulated armatures with a minimum of fabrication. The individual component designs are all available as a start for projects to make custom parts, subject to CAD and laser-cutter experience.
The course emphasizes real-time practical effects, mostly at model-scale. Since this usually happens on a shot-by-shot basis, the goal is to support quick, temporary construction, and to keep it very inexpensive. This is likely to include the following needs:
- building structures to hold materials in a scene
- making articulated armatures to move props or puppets in a scene
- setting up rigs to hold or move lights and cameras
- connecting actuators to rigs and armatures for scene automation
The following guide includes images of the reference designs. Many of the parts exist in multiple variations which can be found in the DXF file archive. These images are not to scale.
Contents
Structural Parts¶
Tubing Clamp¶
Precision Angle Mount¶
Rotating Joints and Articulations¶
Lazy-Susan Turntable¶
Fixed Ball Joint¶
Linear Joints¶
Rail Tie Plates¶
Rail Slider¶
Accessories¶
Flat Element Holders¶
Gears¶
Spur Gear¶
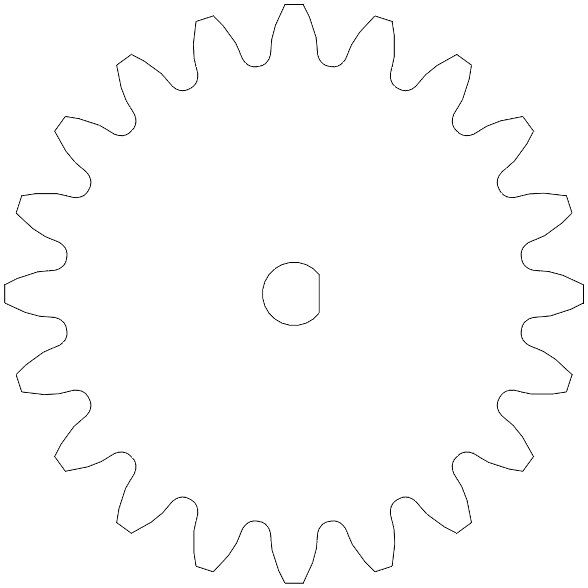
Spur gear, 2 mm module, 20 degree pressure angle. Available in multiple sizes and several bore shapes. With a 2 mm module, the pitch radius is the same as the number of teeth.
Basic Connections¶
(need sketch or photos for: captive-screw connection, standard hole pattern, lap-joint slot, etc.)
Standard Components¶
(need renderings or images for shoulder screws, servos, bearings, etc.)
License and Repository¶

The text content and mechanical designs of the 16-374/60-428 Automation Kit by Garth Zeglin are licensed under a Creative Commons Attribution-ShareAlike 4.0 International License. Based on a work at https://courses.ideate.cmu.edu/16-374.
The original SolidWorks design files for the wooden components are available as a single zip file, or may be browsed file by file in the SolidWorks file tree.
Design Rule Guide¶
The base components and subassemblies were designed with the following set of constraints, chosen for both general purpose utility and simplicity of fabrication. New parts for the kit should generally follow this rules. This list will continue to evolve.
- Material: 6 mm Baltic Birch double-sided plywood.
- Dimensional grid: part features are generally chosen on a 25mm grid. E.g, the basic straight connecting links are 25 or 50mm wide.
- Wooden part fasteners: M6 bolts and nuts. Specific components may require special cases.
- Extrusion rail fasteners: M3 button-head socket cap screws and square nuts.
- Clearance holes: nominal 6 mm. This is a close fit on an M6 screw.
- Bolt pattern: the standard interconnection pattern uses a 25 mm grid with four 6 mm holes at the vertices of a square with 25 mm sides, centered in a 50 mm square area.
- Shafts: 6 mm shoulder screws.
- Shaft holes: 6 mm drill. This is a free fit on a 6 mm shoulder screw. (This may need adjustment.)
- Where parts glue together, provide 0.2 mm glue gap: increase holes in outer surfaces by 0.4 mm diameter, increase slot lengths and widths by 0.4 mm.
- Existing tabs are either 15 or 30 mm long. Existing slots are 9.4 mm wide and 15.4 mm or 30.4 long with the glue allowance. Inside corners are 3.5 mm radius. The preferred inside corner design uses a 180 degree arc, but the position varies depending on the purpose.
- Bearings: still in flux. Some components will use a 6 mm shaft in a plain wooden hole, some may use a 6 mm shaft in a bushing with 8 mm OD, some may use an 8 mm shaft in a 8x22x7 mm skate ball bearing. The actuated knee designs use a 50x65x7 mm thin-section ball bearing.
- SolidWorks parts include Design Tables wherever possible with systematic parametric variations.