Exercise: Marble Fidget Toy¶
In this exercise we will design a small handheld marble toy fabricated using 3D printing.The toy may optionally include a DC motor, freely moving elements, or side ports to use as a tile with other similar devices.
The main objective of this exercise is implementing a device using 3D printing fabrication. A secondary objective is developing your parametric design skills in 3D CAD. The scope and size of the design idea should be chosen in keeping with your existing CAD skills. If you are a novice to parametric CAD, then please keep your priorities centered on modifying the sample device to suit your creative goals. If you have prior CAD experience, please choose a more ambitious scope.
The IDeATe Stratasys 3D printer is a highly capable tool for producing three-dimensional forms in ABS plastic. However, it is considerably more expensive both in production time and cost than laser-cutting plywood, so you will only be allowed one print for this assignment. This prioritizes careful design review before submitting jobs for printing.
Some amount of post-processing is possible, e.g. filing edges or drilling out slightly undersized holes, but the final parts are not solid plastic so the options are more limited than with laser-cut parts.
Objectives¶
The overall objective of this exercise is to design and fabricate a small handheld device incorporating one or more steel marbles in motion. It may be self-contained or include input and output ports so it may be assembled on a sloped table with other similar tiles.
The goals of this exercise are that you should be able to:
Conceive and sketch a handheld marble toy.
Design a three-dimensional form compatible with the FDM 3D printing process.
Create a 3D CAD representation in SolidWorks using parametric constraints and dimensions to capture design intent and support iterative design modification.
Refine a 3D design for efficient use of material to control costs.
If you are already familiar with 3D CAD and 3D printing: incorporate a DC gearmotor into a 3D printed structure.
Sample Parts¶
The sample files for this exercise can be browsed on the course site:
Or as a single zip file:
Sample files are provided on the assumption that students will go farther given a stronger foundation, so these are provided for you to examine and use as starting points. But if you use one as a template, please be mindful that you add meaningful development, not just tweak it trivially.
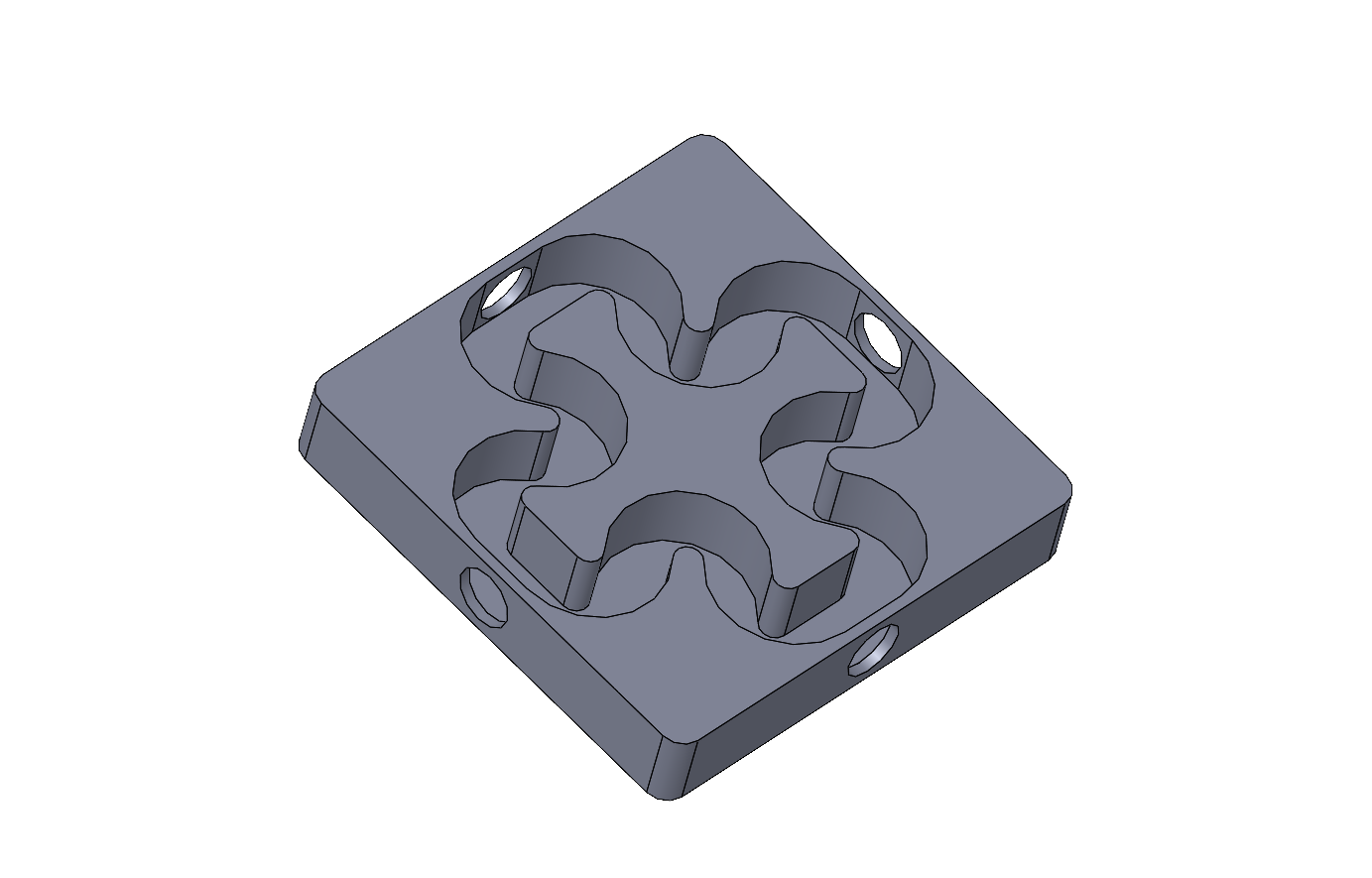
Example of a marble fidget toy. The design includes entry/exit ports on all four sides. This version was drawn using only 2D cut and extrude operations. The track sides are vertical and a ball can fall out the top.¶
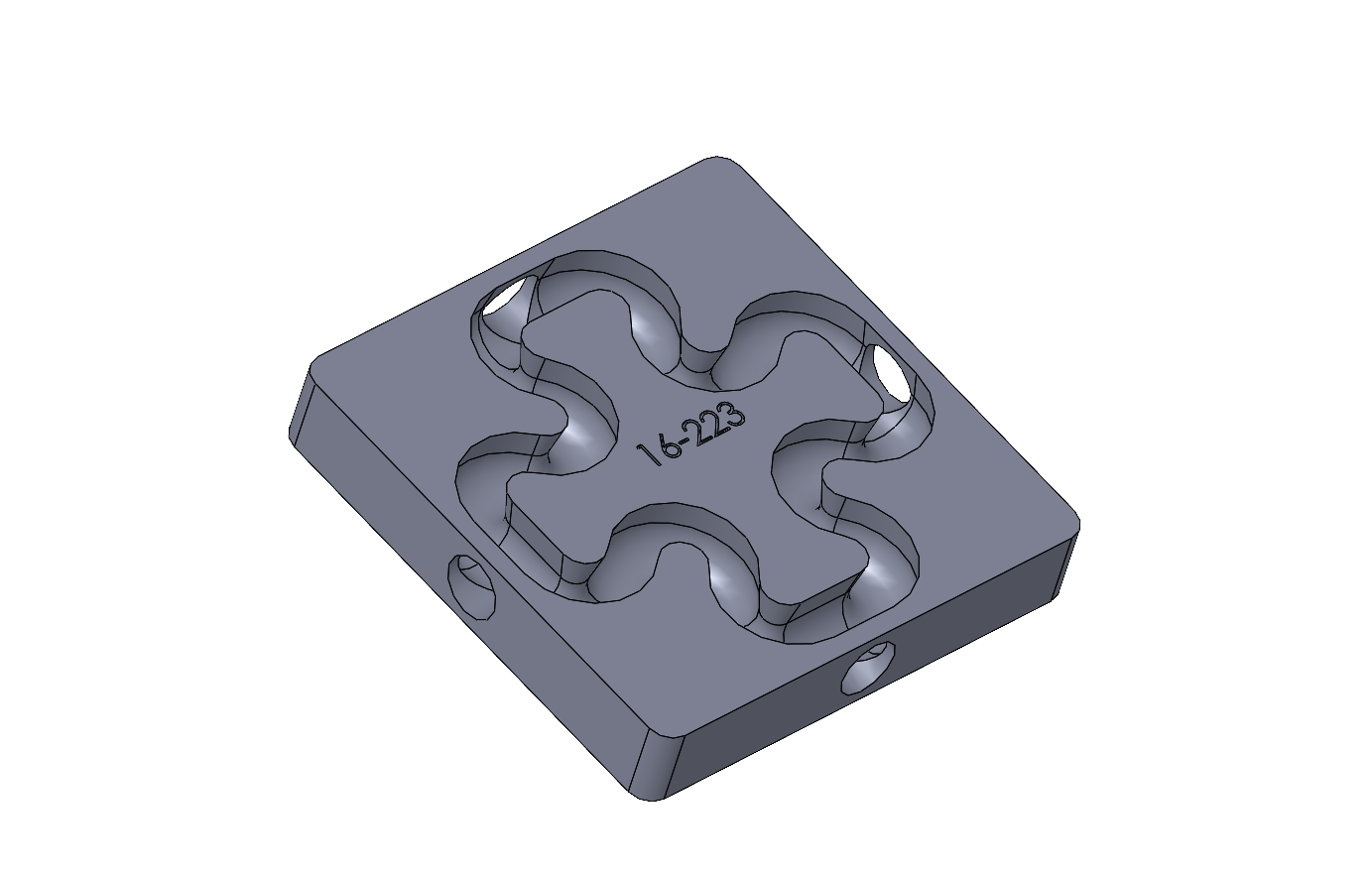
Example of a marble fidget toy. Similar to the first example, but the track is defined by a swept cut using a planar cross-section and planar path. The top track opening is smaller than the 3/8 inch marbles and so a ball is captured in the track or can ride along the surface.¶
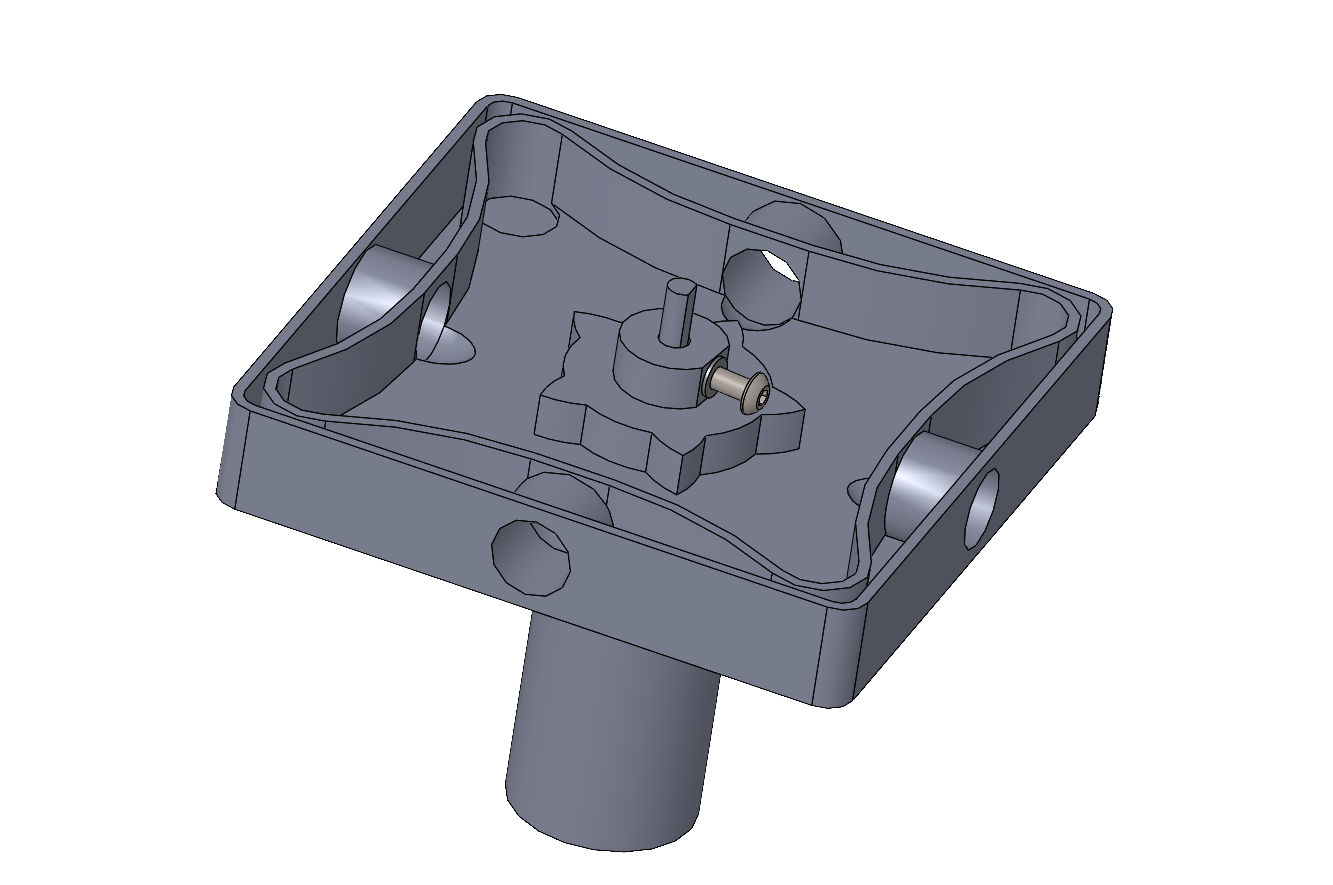
Example of a motorized marble fidget toy. A gearmotor is mounted to the bottom and rotates the central impeller. Shallow pockets in the corners can capture the ball, or they can exit the sides. Material use has been minimized using a shell operation to create thin walls.¶
Material and Tool Constraints¶
The device should fit into a 80 mm square. Entry/exit ports should be located at the midpoint of one or more edges.
The example tiles have a height of 15 mm with the 11 mm diameter side ports vertically centered. Taller features are fine as long as the total volume meets cost constraints.
We will use 3/8 inch steel marbles. A 11 mm track width is recommended for generous clearance.
Please fabricate all parts in a single job on the IDeATe Stratasys CB3D, keeping the cost under $10. As a general rule, the sparse setting appears to print at about 50% density, so a SolidWorks-estimated volume of 100 cubic centimeters will use about 50 cc of plastic and stay under the cost limit. For details on file preparation and submission, please see the IDeATe 3D Printing Guide.
Cost comparison:
laser-cut 6 mm plywood
0.28 cents/cc
material always solid, but lower density than solid plastic
typical PLA or ABS filament
2.5 cents/cc
printing density can be widely controlled
Stratasys 3D printed ABS
15.3 cents/cc
some control of printing density
A straightforward way to export multiple parts within a single STL file is creating an auxiliary assembly file with parts oriented for printing. This file can be saved as a single STL if the export option is set to include all bodies in one file.
Optional:
You may optionally include freely moving elements, e.g. pivoting spinner or gate.
You may optionally include a 25 mm miniature gearmotor driven by a 5V power supply for constant rotation.
You may optionally include a hobby servo actuator driven from a Pico.
Deliverables¶
Live in-class demo of your device.
A short report posted to the course site including:
a zip of your SolidWorks files
a brief video (less than 30 seconds)
a short text statement reviewing your intent and outcomes