Exercise: Marble Lift¶
In this exercise we will design a new marble run component incorporating a DC gearmotor which lifts marbles to increase their potential energy. The main objective of this exercise is implementing a system blending the passive physics of a marble track with a motorized mechanism. The secondary objective is using a mix of laser-cutter and 3D-printer fabrication processes.
A principal technical objective is gaining design experience with gearmotors. These actuators can provide continuous rotation in either direction at variable speed and are useful for energy input and motion control. In this exercise we are simply powering them for for constant rotation, but please note that unlike the hobby servos, they do not have any position sensing, so moving them to specific positions will require the use of additional sensing.
Please choose design goals commensurate with your mechanical design experience and CAD skills. But please consider how to make the device versatile enough to allow different system behaviors to be implemented via software revisions.
Objectives¶
The overall objective of this exercise is to design and fabricate a small marble run track which incorporates one or two DC gearmotors used to add potential energy to the marbles. hThe goals of this exercise are that you should be able to:
Conceive and sketch a simple mechanism including ball pathways, moving elements, actuator mounting, and motion transmission.
Create 3D parts from 2D CAD sketches.
that use parametric constraints and dimensions to capture design intent
that support iterative design modification
compatible with the limits of the fabrication process
Fabricate, assemble, and test a mechanism combining laser-cut plywood, 3D-printed parts, standard components, and a DC gearmotor.
Sample Parts¶
The sample files for this exercise can be browsed on the course site:
Or as a single zip file:
Sample files are provided on the assumption that students will go farther given a stronger foundation, so these are provided for you to examine and use as starting points. But if you use one as a template, please be mindful that you add meaningful development, not just tweak it trivially.
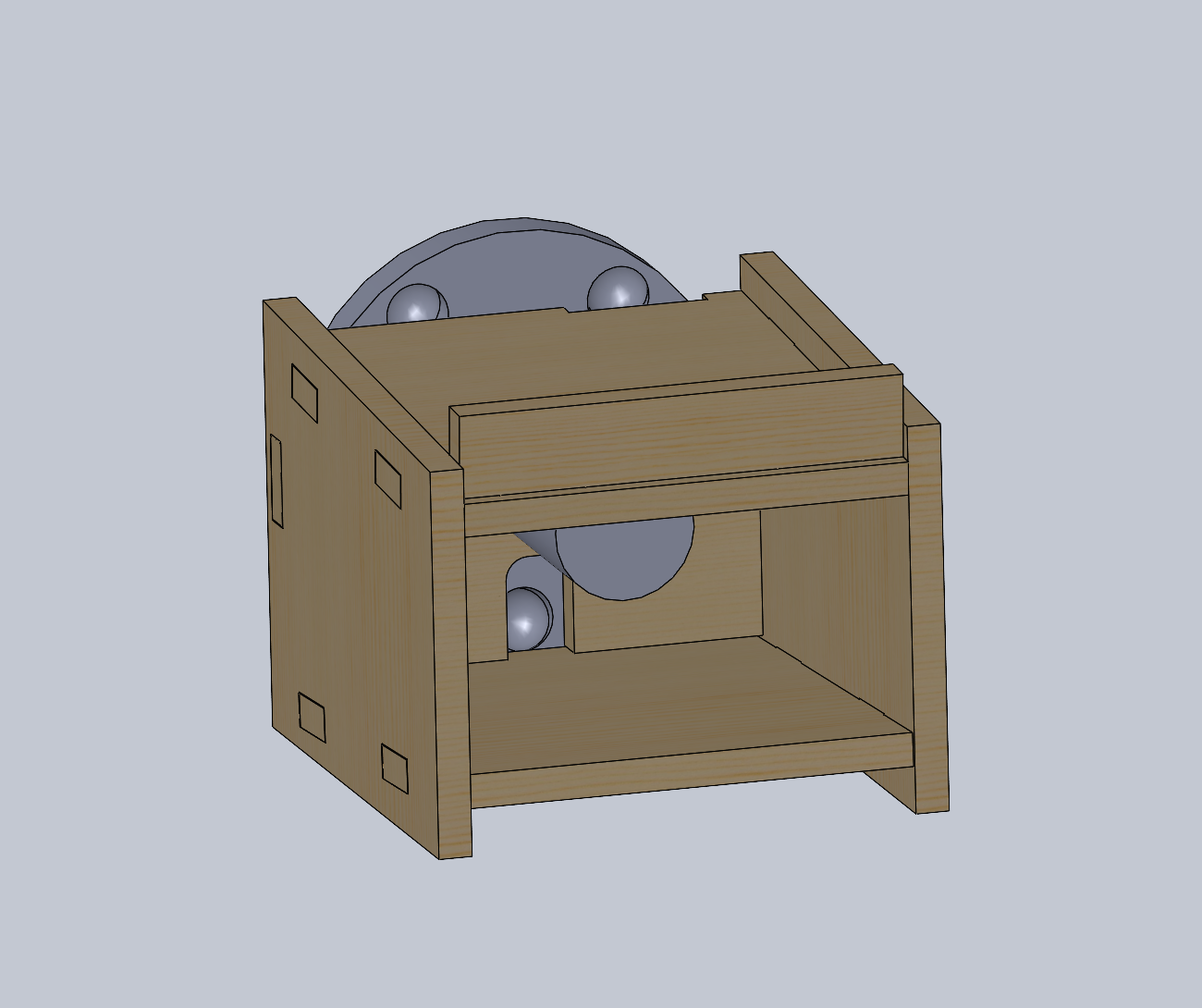
Example of a small marble run including both a DC gearmotor and a 3D-printed lifting wheel. This design is self-contained without entry or exit ports.¶
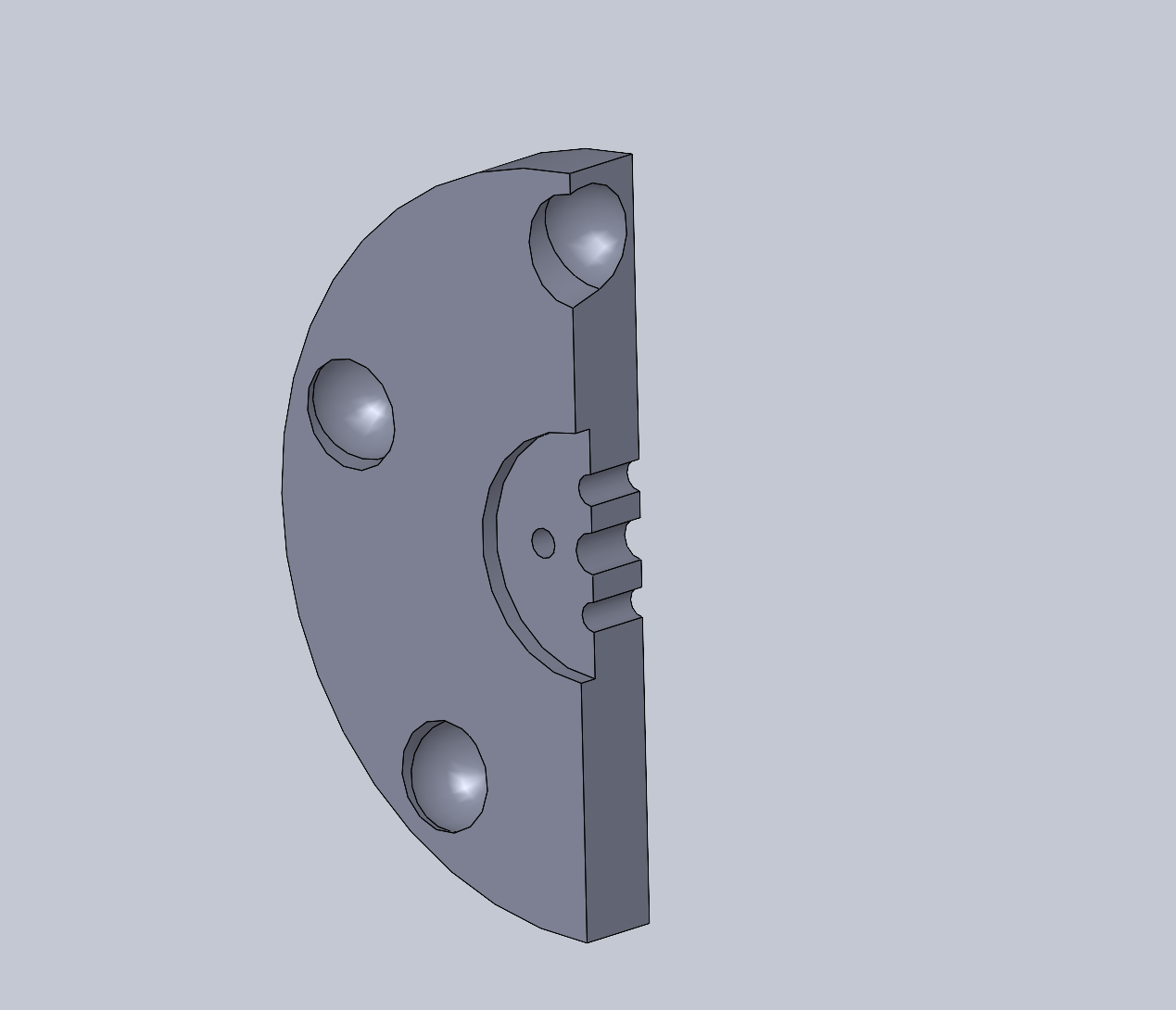
Section view of the lift wheel showing the inclined pocket used to capture a ball at the bottom but force it to roll out at the top. This part is fabricated using 3D printing.¶
Material and Tool Constraints¶
We will use 3/8 inch steel marbles. A 11 mm track width is recommended for generous clearance.
The Pololu 1997 hub is the most practical way to mount an element on the motor shaft. Please do not glue anything to your motor shafts. The M3 x 10 mm button-head cap screws are a good length for attaching them to 6 mm plywood or similar 3D-printed thickness.
Approaches¶
We have seen various approaches to lifting balls:
side-entry wheel (as per the example)
edge-entry wheel, e.g. with hooks
Archimedes screw
ball pump
centrifugal impeller
Deliverables¶
Live in-class demo of your device.
A short report posted to the course site including:
a zip of your SolidWorks files
a photo and/or brief video
a short text statement reviewing your intent and outcomes