Joey Wood & Sebastian Carpenter
Statement of Narrative:
Haptic Mobility is a shared tactile experience. Two participants take remote control of a small bug-like robot with limited mobility. Through their controllers, the participants can feel the the forces acting on the robot’s legs. By virtue of this feedback mechanism, users co-inhabit the body of the machine as they struggle to crawl up and down obstacles in the environment.
Reflection
This project strayed a bit from the explicit framework of using autonomous behavior as a narrative medium; it instead drifted into the territory of using a definitively non-autonomous robot in order to create an experience of shared control and a telematic extension of the users’ bodies. Rather than being a piece of art that is merely observed, Haptic Mobility as an installation requires participation in order to be fully appreciated. Like all remote-controlled vessels, this robot extends the users’ range of mobility in a way completely divorced from their physical body. Where this experience becomes somewhat novel, though, is in the direct physical feedback returned to the control joysticks and in the piece’s encouragement of collaborative control. Users can not only feel what the robot feels, turning the robot into a true extension of their bodies, but with each user taking control of only one leg with their joystick, they begin needing to communicate and developing a shared rhythm in order to make the robot follow any sort of predictable path.
Outcomes
Despite being separated by mid-November, we managed to get a robot that functioned. It was able to drive and be controlled in the manner we intended, though not necessarily to the degree of fidelity we had hoped. A number of aesthetic sacrifices were made in the interest of time and resources (notably the lack of a housing for the controller and the slightly ill-fitting shells that necessitated fastening with tape rather than a proper housing), and the robot likely would have benefitted from more tuning on the controls side to improve the experience. Another casualty of our logistic constraints was our ability to do an actual physical installation that other people could experience. If time allows over the next couple months, we may revisit this project for the purposes of making improvements or setting up an actual installation.
Video
Technical Documentation
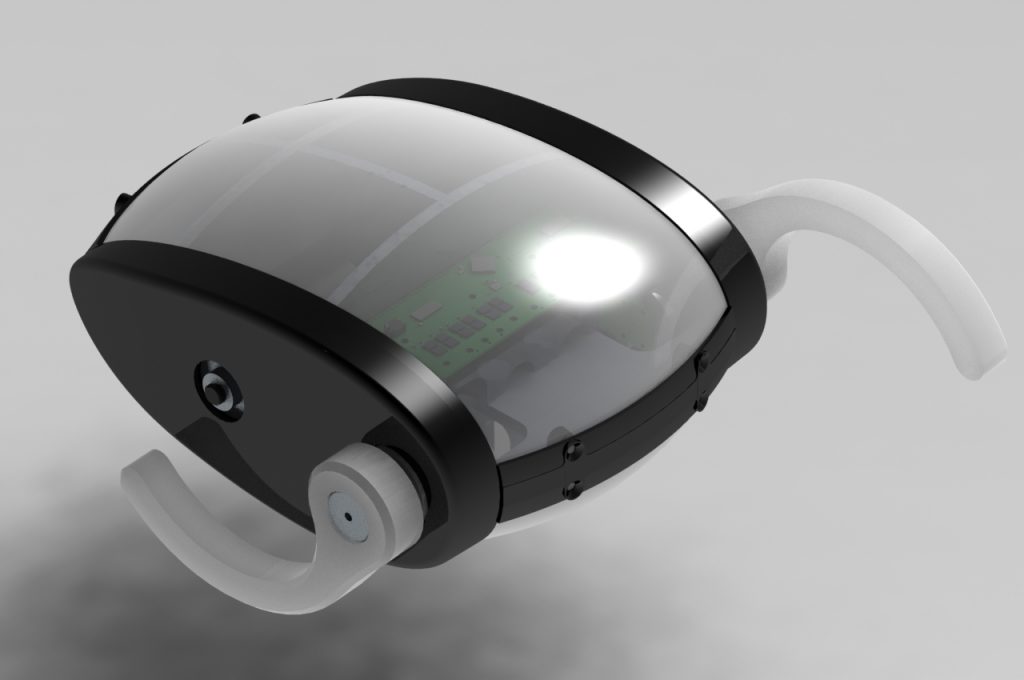
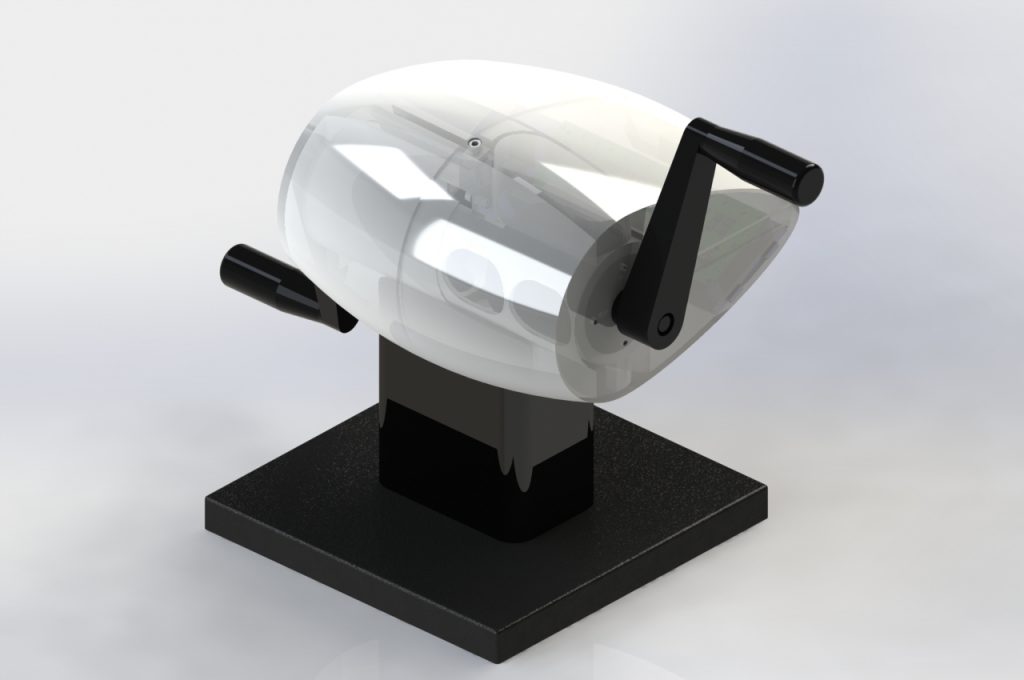
Mechanical CAD & Software Files:
https://drive.google.com/drive/folders/1FTkAokVrruO1IYQU8XG63WgJ1ay5KRsM?usp=sharing
Contributions
Joey: Mechanical design of robot and robot drive mechanism, fabrication (machining, lasercutting, 3D printing) of mobile robot, electronics architecture & assembly, software development and testing of bilateral teleoperation control.
Sebastian: design and fabrication (making plaster form and vacuum forming plastic) of outer shells for robot, 3D-printing robot legs in nylon, designing controller housing (ultimately never fabricated due to time and logistical constraints), creating renderings of robot and controller, editing final video.
Citations
[1] Katz, Benjamin (2018). A Low Cost Modular Actuator for Dynamic Robots. Massachusetts Institute of Technology, Cambridge, Massachusetts.
[2] K. Goldberg, J. Santarromana, G. Bekey, S. Gentner, R.M.C Sutter, J. Wiegley (1995), The Telegarden, University of Southern California, Los Angeles, California.
Comments are closed.