Ankita Bhanjois (abhanjoi) & Sunjana Kulkarni (sunjanak)
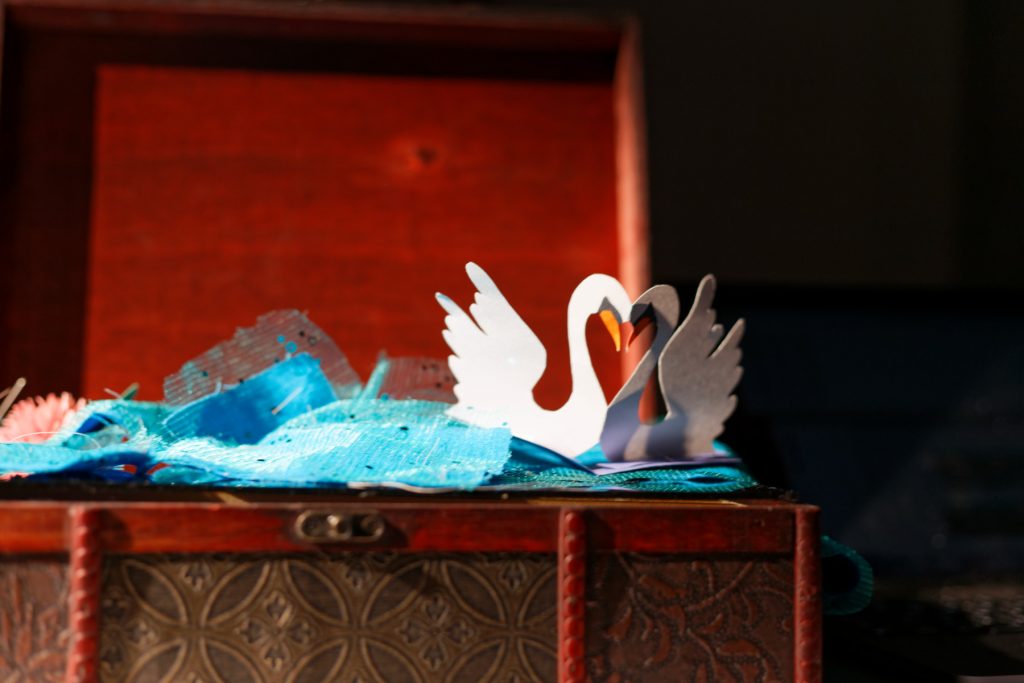
Concept
When we had first drafted what we wanted to accomplish with our “Magical Canvas,” we knew we wanted to invoke that idea of time passing and progressing. The idea behind our project was to demonstrate the passing of time and how change is inevitable. So, we took the idea of a blank canvas where there was a barren surface and we transformed it into a beautiful idealistic landscape. And from the perspective of the audience, that is exactly what we wanted to show: a blank piece of acrylic becoming a Claude Monet inspired landscape.
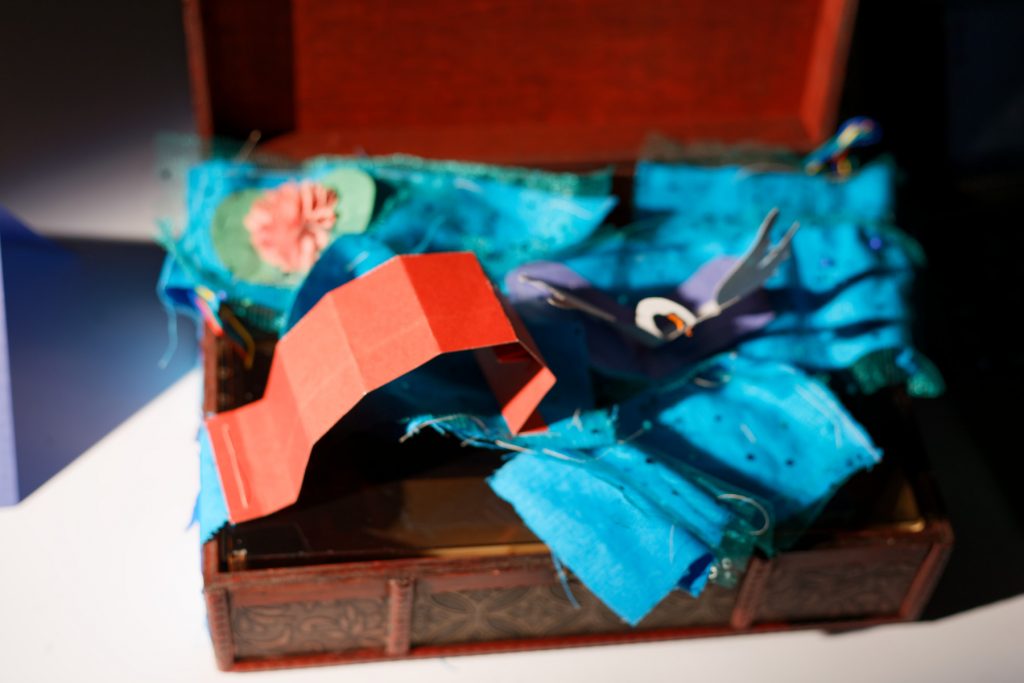
Reflection
How does our project fall inline with the courses themes? We were able to use robotic movement and mechanisms to create an art piece, one that was animated in a surprising manner. By using conveyor belts, pulleys, and magnets, we were able to facilitate the motion of pop-up mechanisms to create a landscape mimicking one of Monet paintings. Using the autonomous behavior helps enhance the narrative medium especially for our project, because if we use an opaque piece of acrylic, the audience doesn’t know that there is a mechanism under the acrylic layer. Thus, the pieces of fabric seem to slide by “magic”, coming together to create a landscape. There is always this misconception that robotics are just for the practical and technical uses, but this project and all the other RfCP projects prove that autonomous behavior and robotic movement can create artwork.
Outcome
Creating our final project was a journey of trial and error. In regards to the soft material manipulation, there were lots of adjustments made along the way. We had initially started with a more busy design with more pop-up elements but noticed that with what could be accomplished with our fabric ribbons, that would not be as feasible. There were many prototypes that went into coming up with the fabric ribbons and how they would be structured. Initially, paper was not meant to be used in our design at all but it proved to be an interesting medium to work with alongside the fabric, especially because it added more spring to the fabric’s free structure. We discovered that if we were to create pleats in the fabric to fold up the pop-up paper elements then it would be easier to unfold as the magnet dragged the fabric. We also learned that with the paper’s springiness it would be hard to keep the pleats on the side of the suitcase before being unravelled, so we used sewing pins to fasten the fabric and as the fabric unravelled the pins would detach. Working with the paper and the fabric taught us a lot about mixed media and how they affect one another. It was unexpected seeing how the construction paper completely changed the movement effect of the fabric and it was a challenge to work with. However, with the various prototypes, we were able to come up with a working design.
As far as fabricating the model, even that process required some trial and error to see which model design would be most appropriate. We started out by building a model which consisted of one base horizontal panel and two upright vertical panels, with one stepper motor attached to each vertical panel and a belt between the two. We realized that this wasn’t scalable because of two things. One, using two stepper motors where one was the “idler pulley” and the other actually had its motor powered was a waste of a stepper. Two, the two panels wouldn’t be that supportive, and having one panel connect the stepper and the idler pulley would be better.
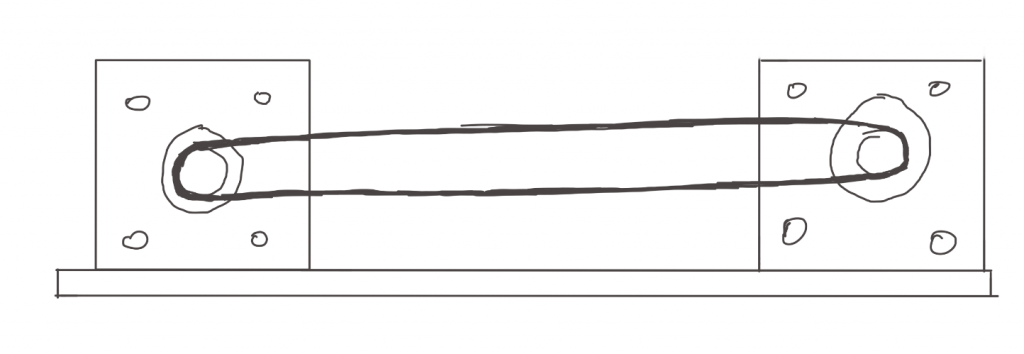
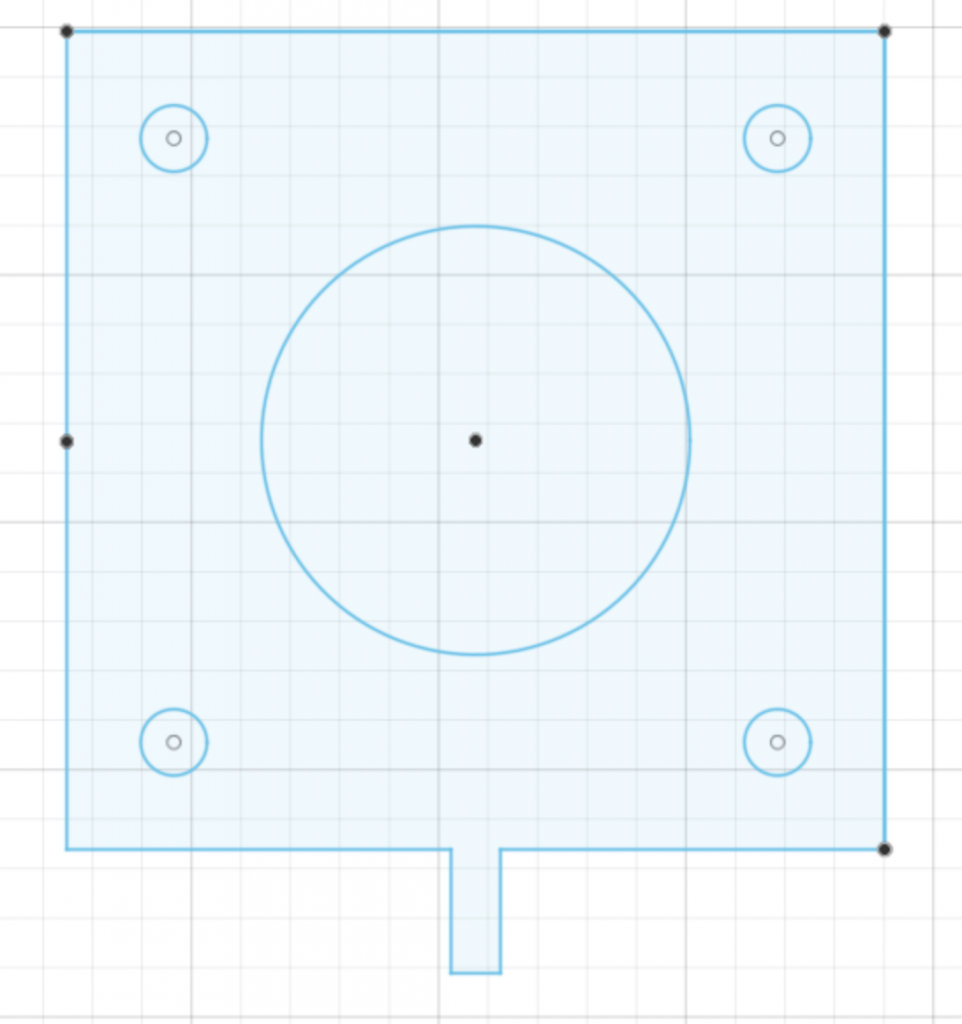
Next, we built a model which consisted of a stepper and an idler pulley, with one panel connecting the two and a belt with a coupler moving between them. While the belt was functional, we discovered the panels needed to be taller in order to account for the heights of the other coupler pieces, which were larger than the one we were using, and would have to have the magnets glued on top. We also realized we needed to build a model with walls so that the panels would be better supported, and we needed to organize the panels so that there would be enough room for 4 motors, but the whole model would fit in the small space of the suitcase. This required a lot of measurement and planning with paper drawings before using Fusion360 to create the actual model and laser cutting and assembling the model.
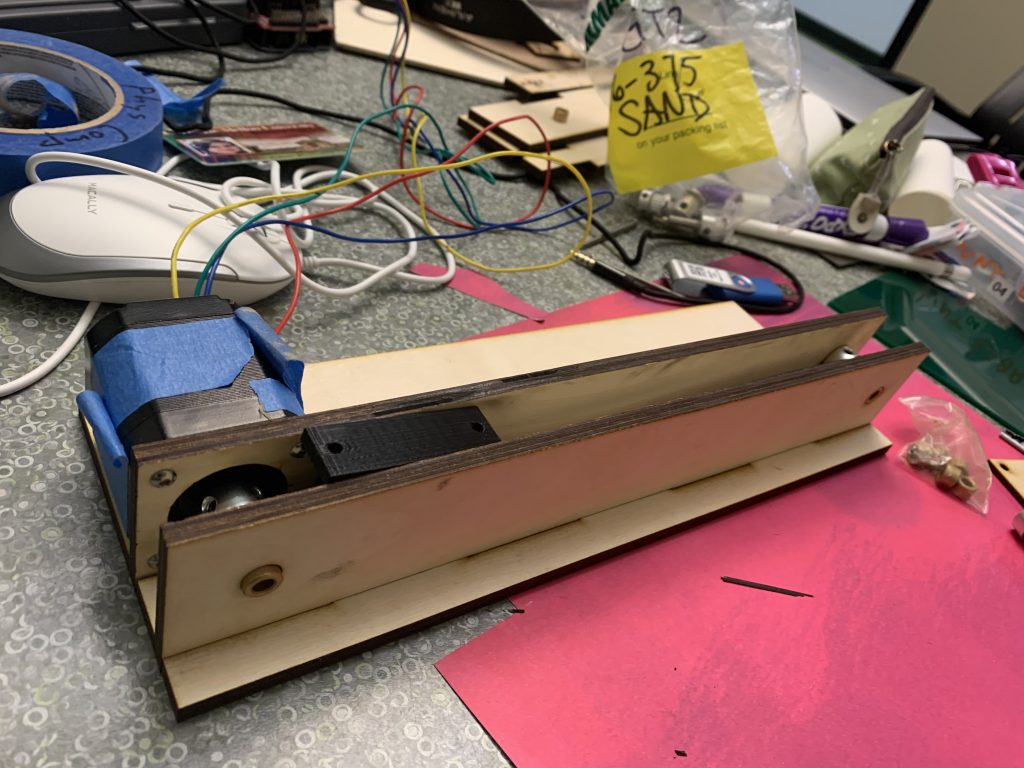
While assembling the model, we ended up running into issues we hadn’t previously considered, like the strength of the magnets on the coupler pieces causing them to “lift” to meet the magnets on the other side of the acrylic, and the belts not being perfectly tensioned. We ended up fixing this by using rods that went through most of the coupler pieces (minus the one without holes to put the rod through), so the pieces could only slide linearly and not rise. We also raised the magnets to a level where they were touching the acrylic by having them be situated on top of mini platforms, which were then glued to the couplers.
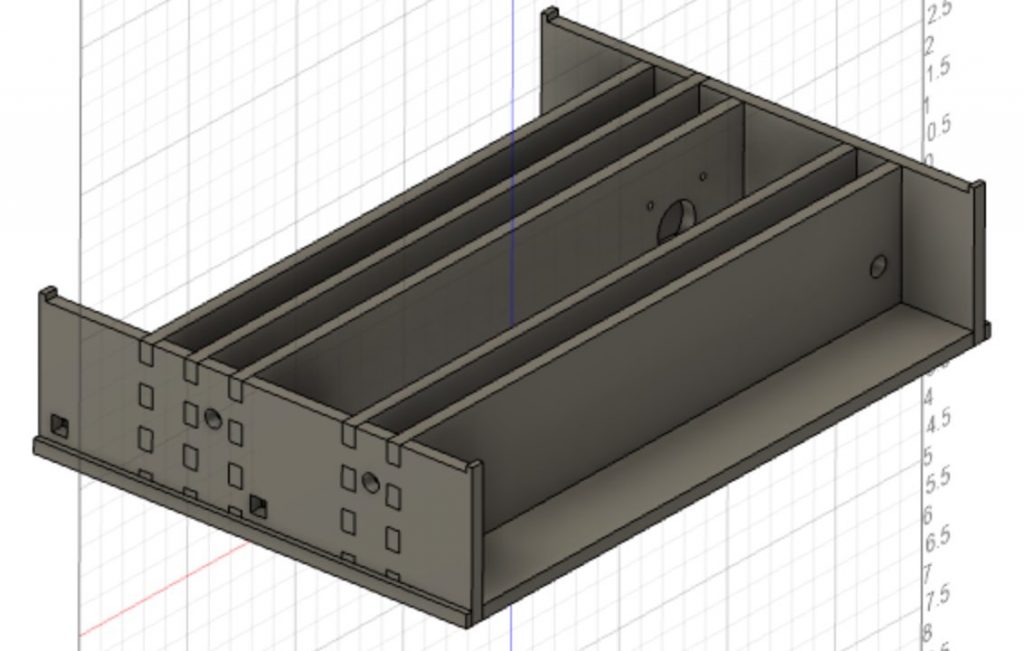
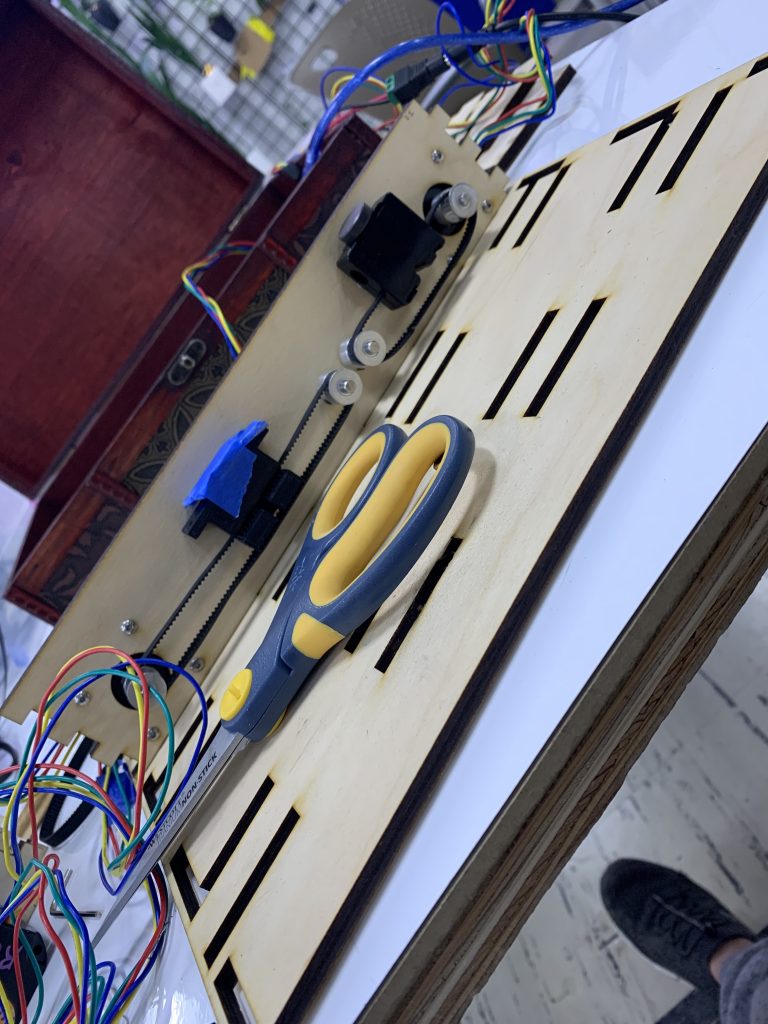
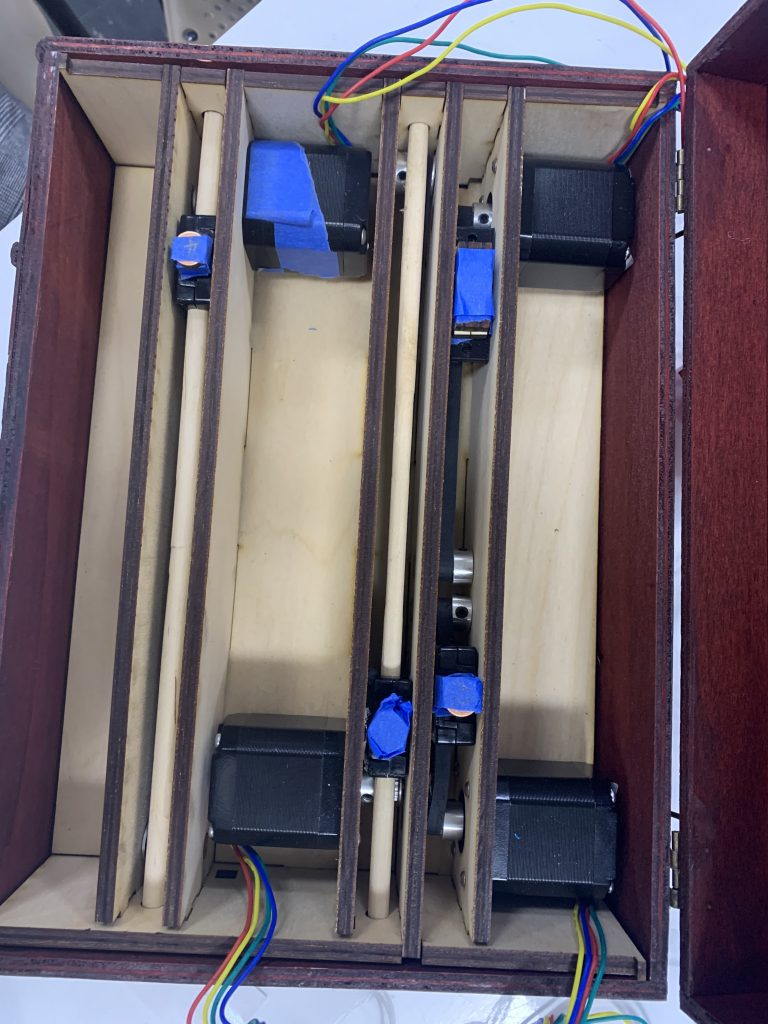
As for the code, it was pretty simplistic. The only trial and error that was needed was to see which speeds the magnets should move at to produce the most dramatic effect, so we could hardcode a “start” and “reset” mode and have each motor start, move the magnet along the belt for some seconds at a particular speed, and then stop.
Final Setup/Results
For our final exhibition, we had set up three ribbons that would be unravelled in a sequence. First, a ribbon holding a waterlily would unravel and then a ribbon with two swans, and finally for our showstopper, we had a bridge be unravelled onto the suitcase. The lighting was set to add extra reflection onto the sheer fabric and create an effect that the fabric was “water.”
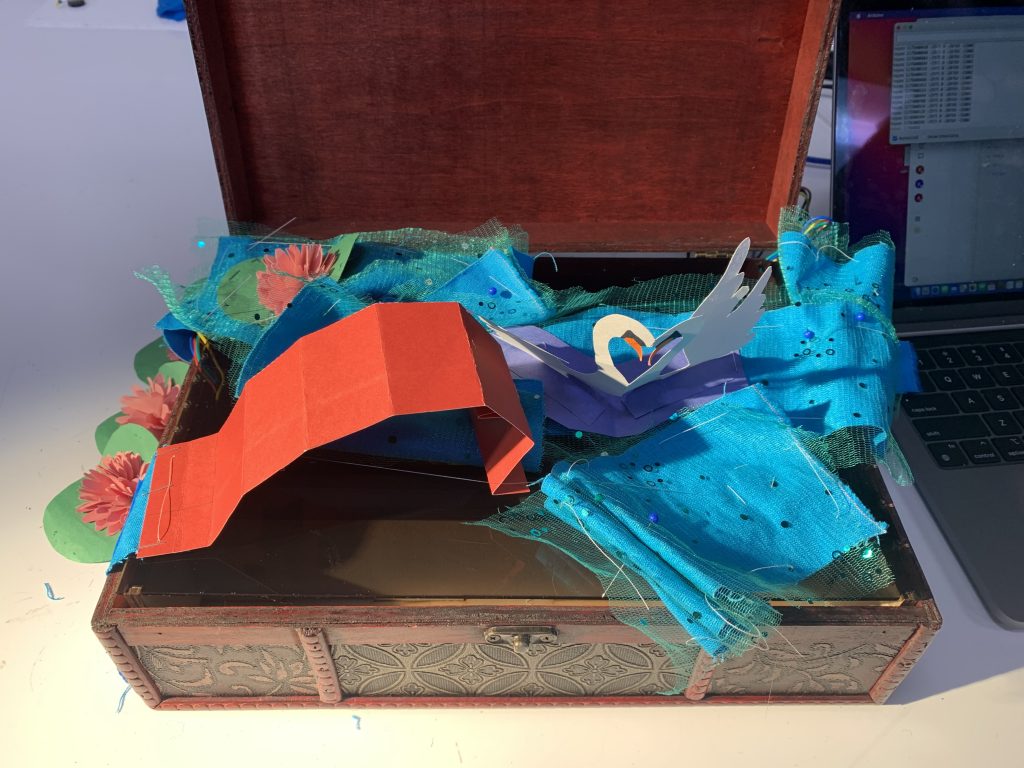
References/Inspiration
We wanted to create a landscape that mimicked Claude Monet’s iconic waterlily painting:
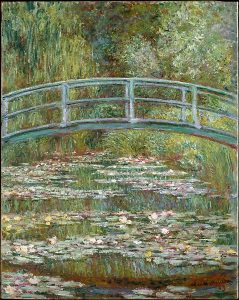
soft material references:
We took a lot of inspiration from the other IDeATe class, Kinetic Fabrics, thanks to the help of Professor Olivia Robinson. In addition, a lot of references were made to tutorials on how to create pop-ups.
Technical Material
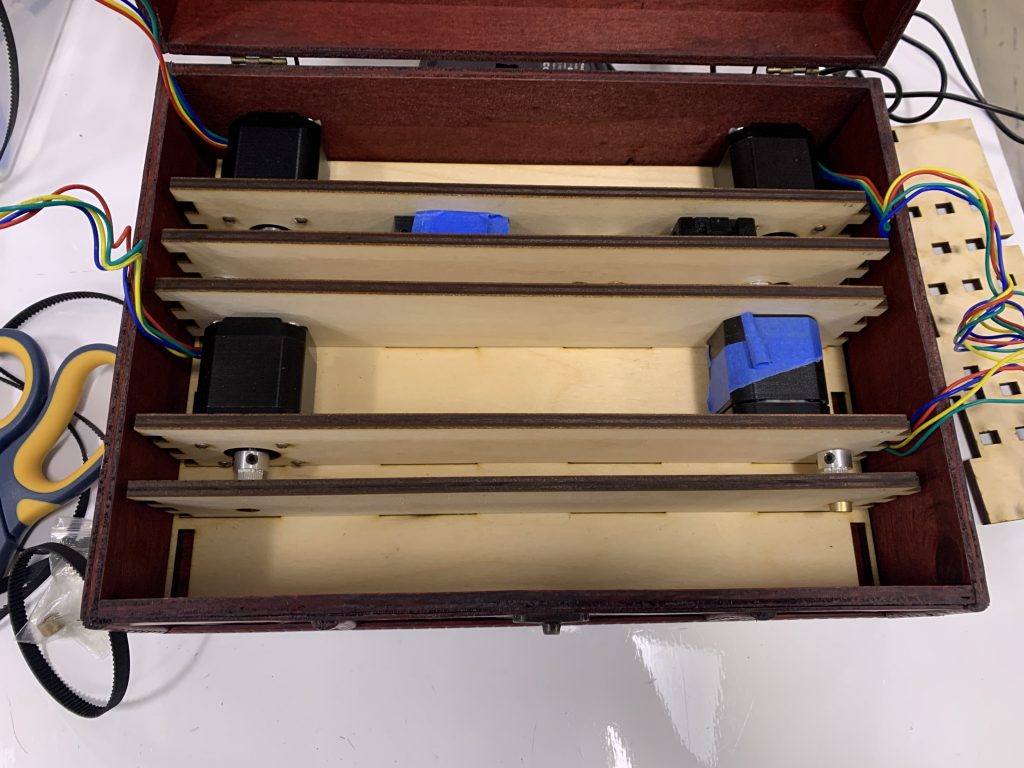
Feedback
To our relief and surprise, during the final showcase, our project was able to work most of the time. What was least ideal was that we needed to manually reset and bin the fabrics before redoing our demonstration, but the audience was happy enough to wait. Everyone who saw our functioning project wanted to know how were able to achieve the movement of the fabric and were interested to hear it was solely through magnets on a conveyor belt. This machine was able to create an art piece solely through movement and it created a landscape for the audience to see.
Specializations
Model Fabrication/Code – Sunjana Kulkarni
Soft Materials/Art – Ankita Bhanjois