Suitcase Testbed¶
The suitcase testbed is a four-channel actuation system installed inside an aluminum equipment case. The intention is that we will use this as a shared platform which students augment with props and additional mechanism to explore the possibilities for a notionally portable performance.
The aluminum suitcase has an inserted structure containing four stepper motors, Arduino drive system, and 12V power supply. The motor shafts have hubs installed onto which are mounted wooden discs with a mounting hole pattern. The Arduino USB cable and motor power cord can be routed out the slots in the left rear corner.
The SolidWorks model is available as suitcase-testbed.zip, or may be browsed as individual files in the suitcase-testbed folder.
The electronics use an Arduino with a CNC Shield on top incorporating four A4988 stepper motor drivers. Documentation can be found at CNC Arduino Shield.
A recommended approach for programming the system is to write control scripts in Python which communicate over USB with Arduino firmware which moves the motors. An initial candidate for that firmware is the StepperWinch Arduino Sketch.
With this strategy, we can also use wrapper code to emulate the Webots interface but transmit motion commands to the Arduino. This will enable some degree of transfer from the simulator to the hardware. Sample code can be found at Suitcase Control Samples (Python).
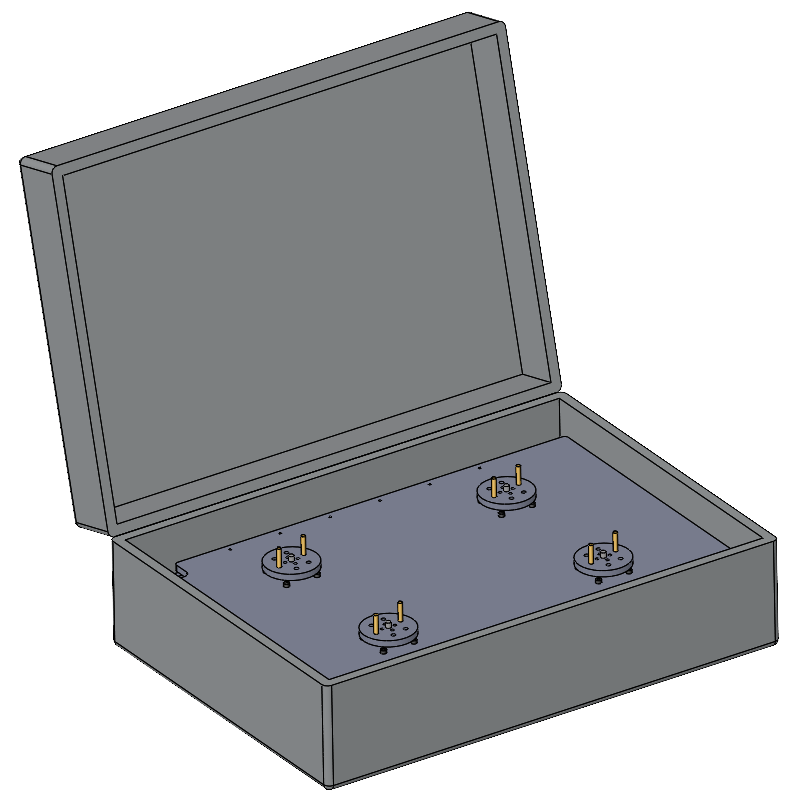
CAD rendering of the wooden structure inside the suitcase. Four stepper motors are mounted in the deck with hubs installed on their vertically aligned shafts. The electronics and power supply are mounted below the deck.¶
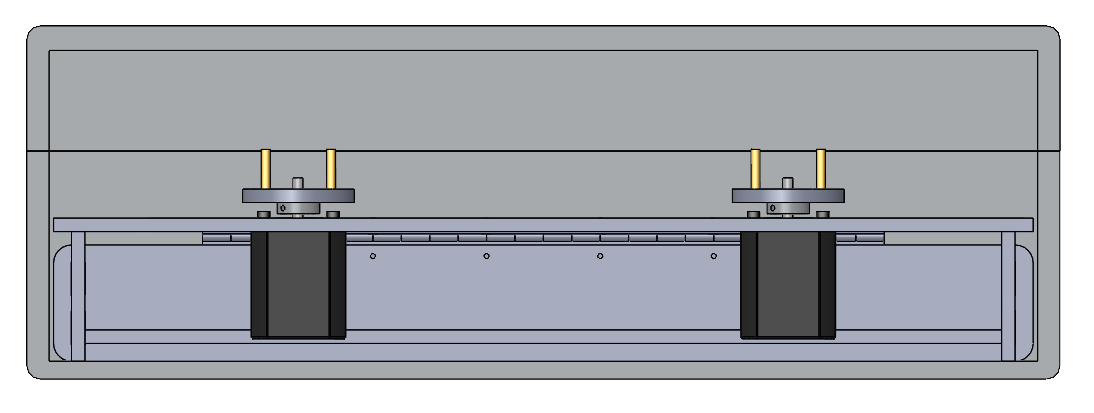
Cutaway view CAD rendering showing the placement of the stepper motors.¶
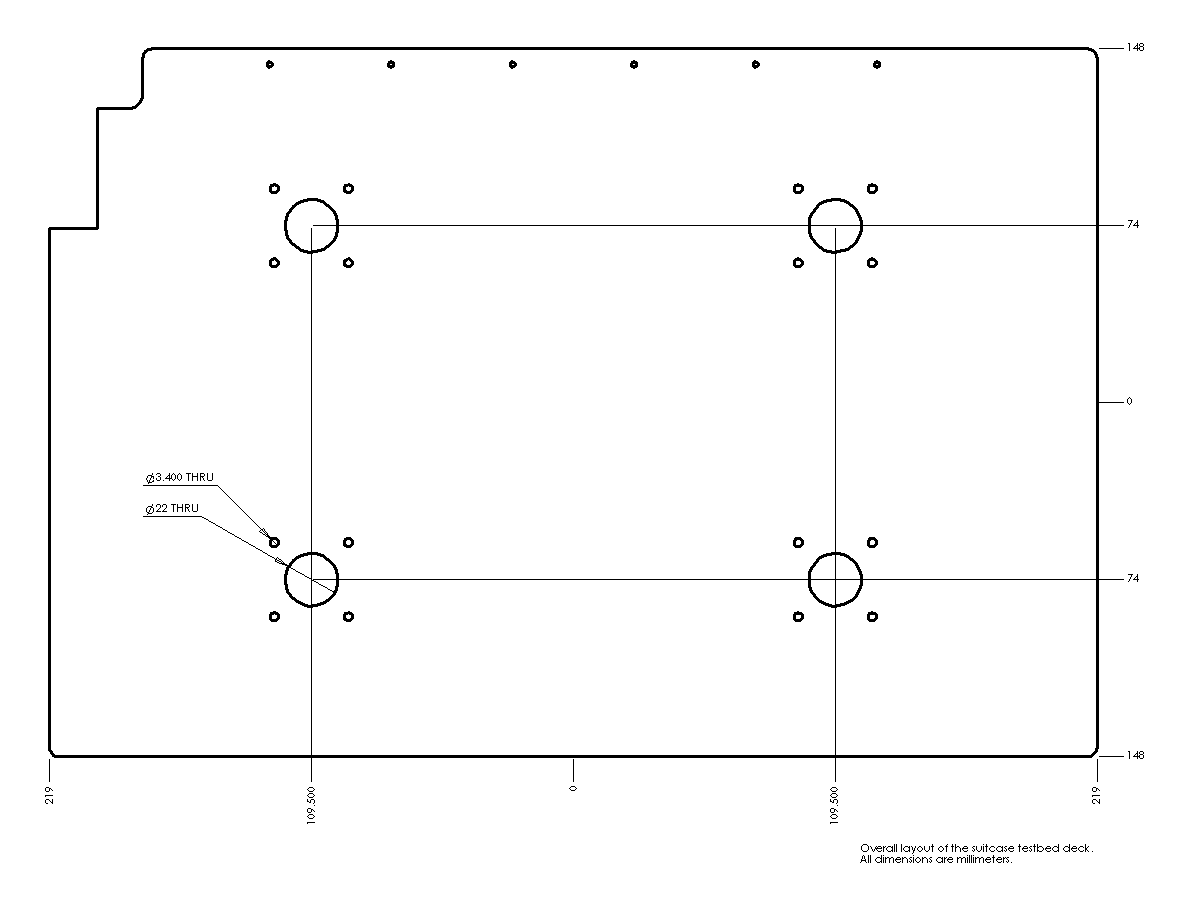
Essential dimensions of the deck and motor placement.¶
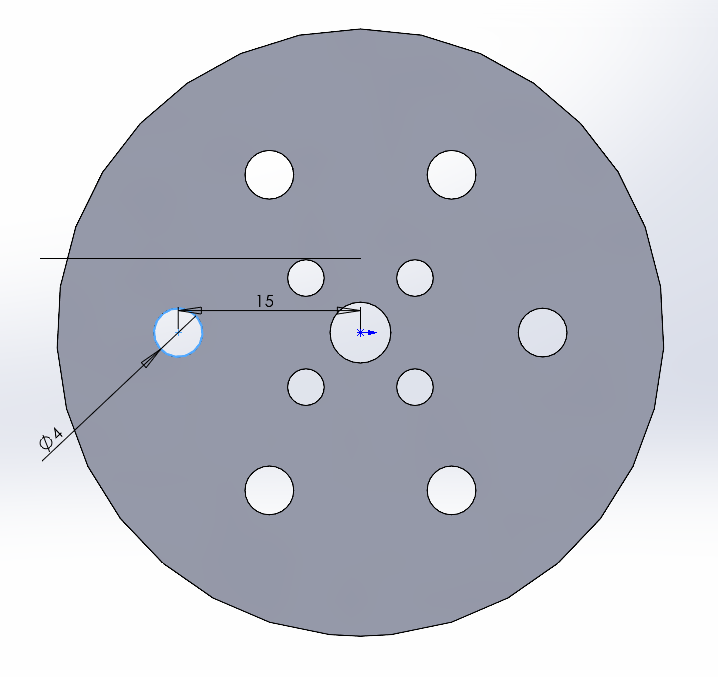
Rendering of the discs attached to the motor shafts. Each is fabricated from 6 mm plywood. The central hole pattern is used to screw the part to a metal hub. The outer pattern of six 4 mm holes evenly spaced on a 30 mm diameter circle is intended for attaching student parts.¶
Fabricated Parts¶
All fabricated parts are designed to be laser-cut from 6 mm plywood. The cutting patterns may be found in laser-cutter-DXF.
Quantity |
File |
Description |
---|---|---|
1 |
deck |
Main flat deck within suitcase, hinged onto rear-support. |
1 |
rear-support |
Vertical strut across the back onto which the hinge mounts. |
1 |
front-support |
Vertical strut across the front supporting the front edge of the deck. |
2 |
side-support |
Vertical strut on each side connecting rear-support and front-support. |
1 |
electronics-bracket |
Horizontal plate near bottom of case onto which the Arduino and power supply are mounted. |
4 |
rotor-base |
Circular disc mounted on each motor hub. |
Standard Parts¶
Quantity |
Size |
Description |
Vendor |
Vendor Ordering |
---|---|---|---|---|
4 |
NEMA17 |
stepper motor, 76 oz-in (5.5 Kg-cm), 1.5 Amp/phase, M3 mounting holes, 5mm shaft |
Automation Technology |
KL17H248-15-4A |
4 |
5mm x M3 |
mounting hub for 5 mm shaft, M3 holes on 12.7 mm circle, for stepper motors, includes 1.5 mm hex key for set screw |
Pololu |
1998 |
24 |
M3 x 10 |
socket head cap screw, 2.5 mm hex socket |
McMaster-Carr |
91290A115 |
8 |
4 x 24 |
optional dowel pin installed in the rotor discs |
||
1 |
piano hinge |
McMaster-Carr |
1575A1 |
Assembly Notes¶
All fabricated parts are designed to be laser-cut from 6 mm plywood.
Electronics and Software¶
Drive system: CNC Arduino Shield.
Arduino firmware: StepperWinch Arduino Sketch.
Python scripting examples: Suitcase Control Samples (Python).
Webots simulation of system: Suitcase Robot Model.
Prototype¶
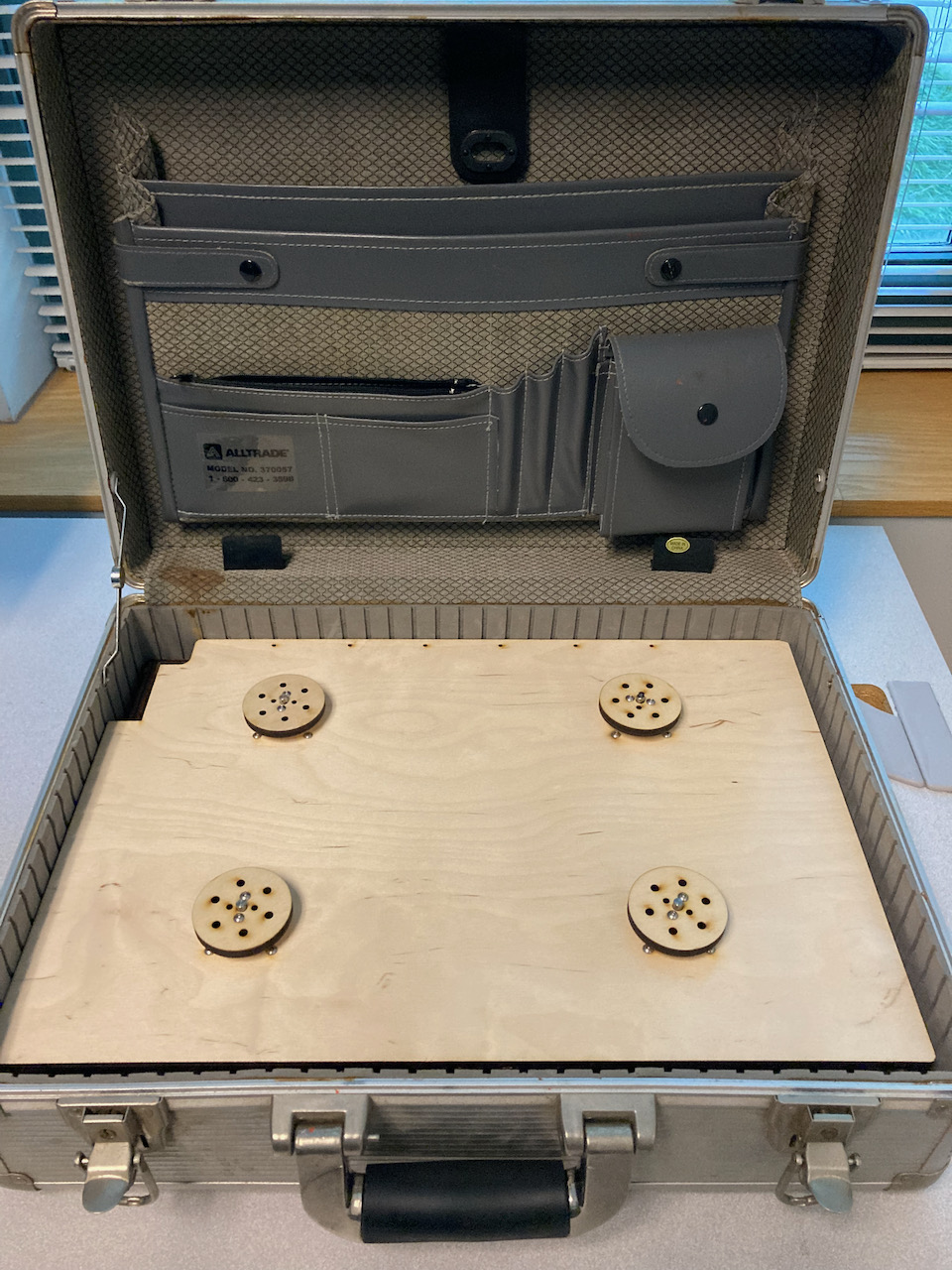
Photograph of the physical prototype.¶