TEAM: Myles Sherman, Vidhi Patel, Luis Ortega
Description
Be amazed and astounded at the all-new all-different Daredevil Rollercoaster from the hottest new engineer…YOU! Explore your limitless imagination as you push the boundaries of your wildest dreams! You can build any track you want as low as the ground or as high as the sky, with twists and turns galore! Then race your coaster all around the room with boundless velocity and limitless acceleration! Make your dreams a reality with the spectacular, extravagant, fearless Daredevil!!!!!!!
*Recommended for ages 12+
How the parts were made
Tracks
Each track component was first modeled in Solidworks, then 3D printed on the Stratasys continuous build printer. Our initial design derived inspiration from roller coasters such as the Vertical Velocity coaster at Six Flags Great America that provide channels on the sides of the track for wheels. Initially, this consisted of an I-beam style track with a lip on either channel to prevent the wheels from falling out. This idea was scrapped due to its high mass that would make it difficult reproduce quickly, as well as its lack of an aesthetically pleasing design. Our improved design consisted of grooves for wheels on the top and bottom of the track, as well as rungs through the center of the track to decrease its mass while maintaining structural stability. Our tracks are also modular, so that the builder can rearrange them in any configuration they desire. This was first done with small hexagonal connections, which were not robust enough to withstand the weight of coaster and repeated use. Our final design constituted of two thick rectangular pegs that would connect sections of track together.
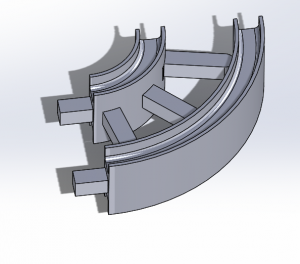
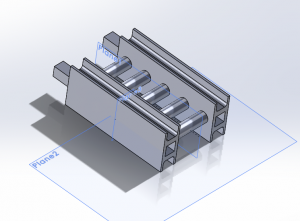
Supports
Our supports were made using a combination of laser cut and 3D printed parts. The bottom platform was 3D printed with grooves for laser cut columns to slot into; similarly, the top platform that would hold the tracks in place was printed with grooves for the upper part of the column. These top platforms also have 240 degree semi-cylinders for the rungs of the track to snap into. We ensured that the spacing of these cylinders was standard throughout the track and could be placed anywhere in the design. Ideally, we would have different height supports for the various needs of the builder.

Coaster
We began with a simple design for the roller coaster which consisted of a trough like chassis with hexagonal holes to stress fit the axles. We ran into numerous issues with this stress fit, leading to many redesigns of our axles. Initially, we adopted a c-bar design for our axles which would have allowed us to fasten two delrin wheels on the same axle to accommodate our top-and-bottom track design. This proved difficult due to the fragile nature of the 3D printed axles, which were too thin for the stress fits we had designed. After a few iterations using 3D printed c-bars and acrylic crossbars, we converged on a design that would only use the top rails of the track. We decided to use four non-c-bar axles per coaster (i.e. four wheels instead of eight), which greatly simplified our design.
