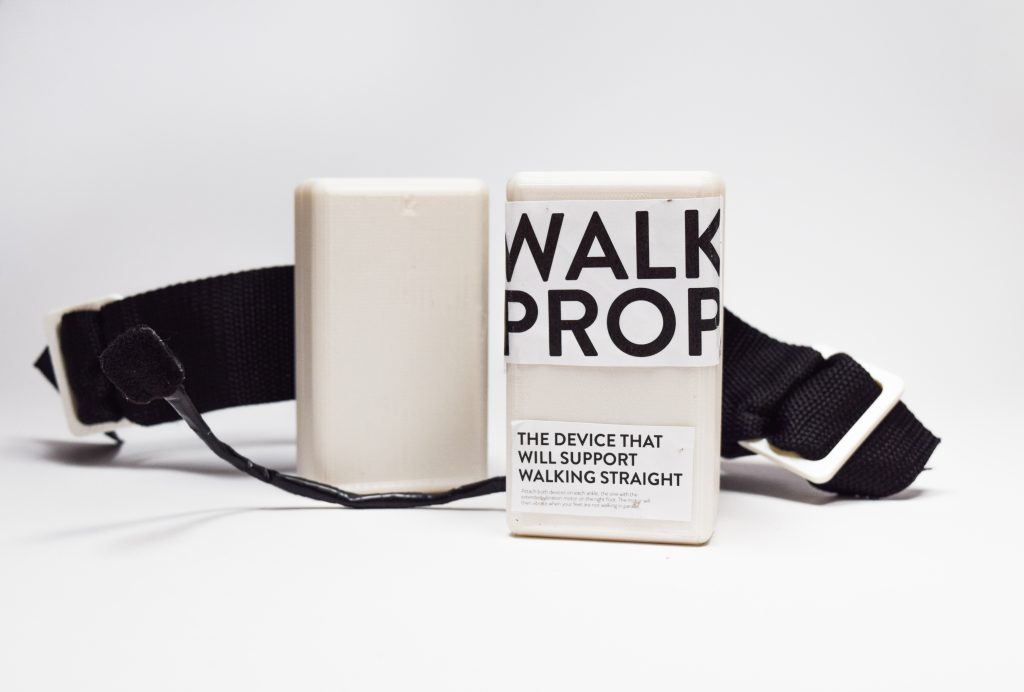
WalkProp
OvervIew
WalkProp is an assistive device that will support your feet “walking straight” or parallel from each other.
How the device works (you can hear the vibration when the right foot is not parallel to the left foot)
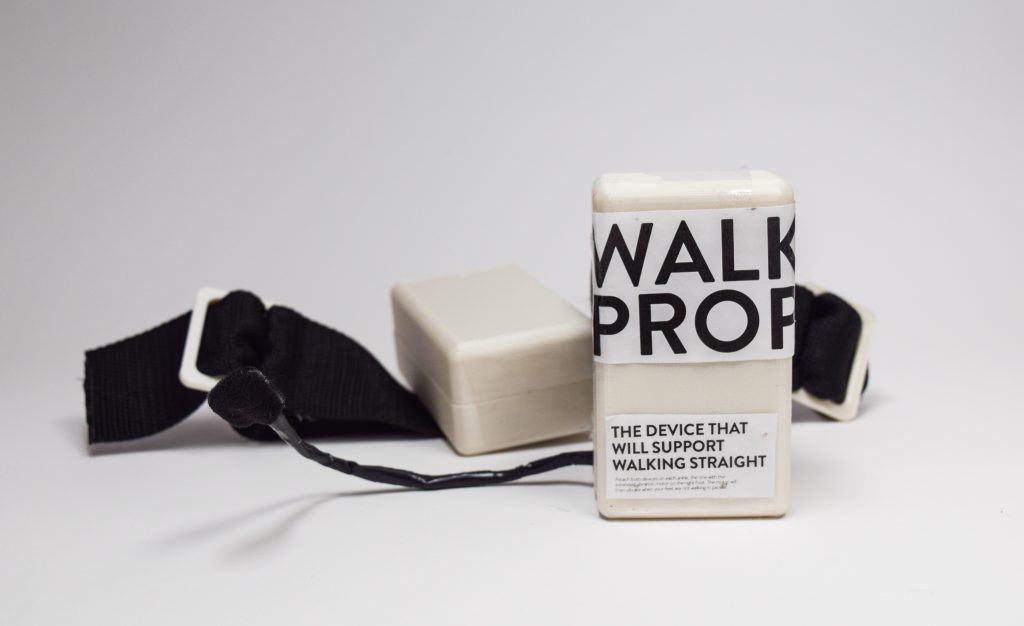
Overall image
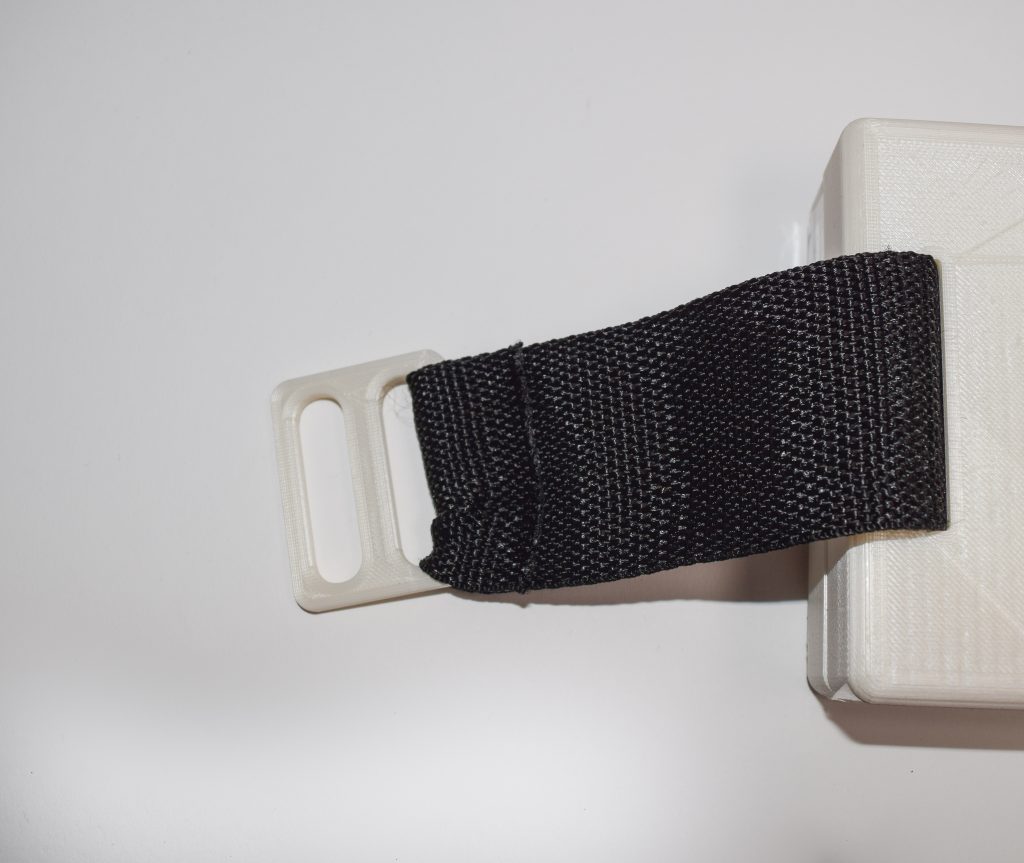
3D printed strap buckle
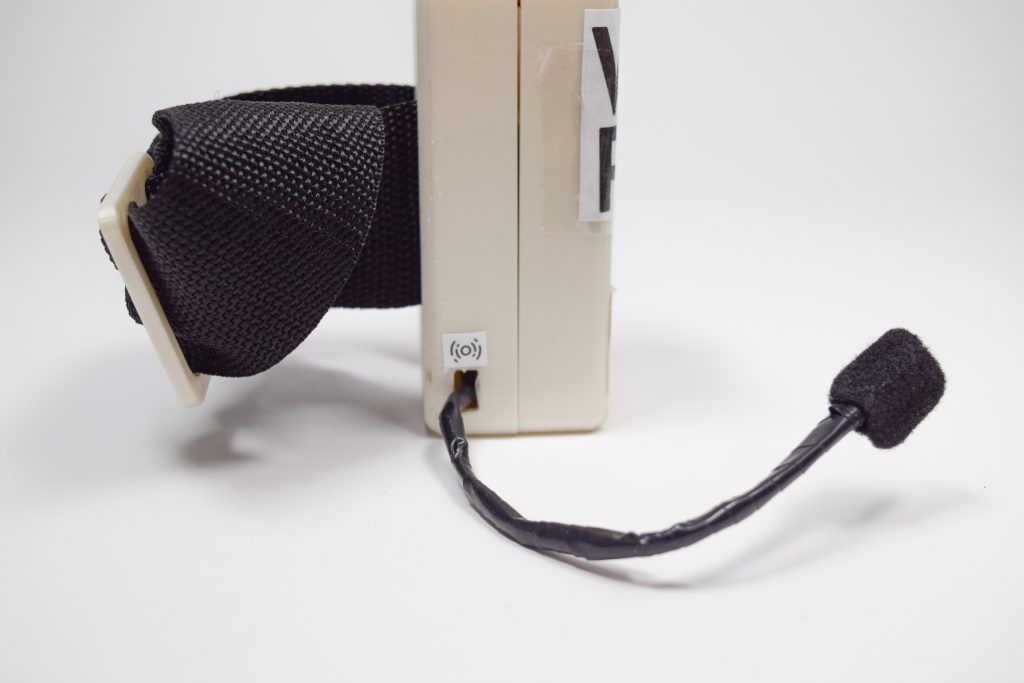
Vibration motor and its packaging design on device
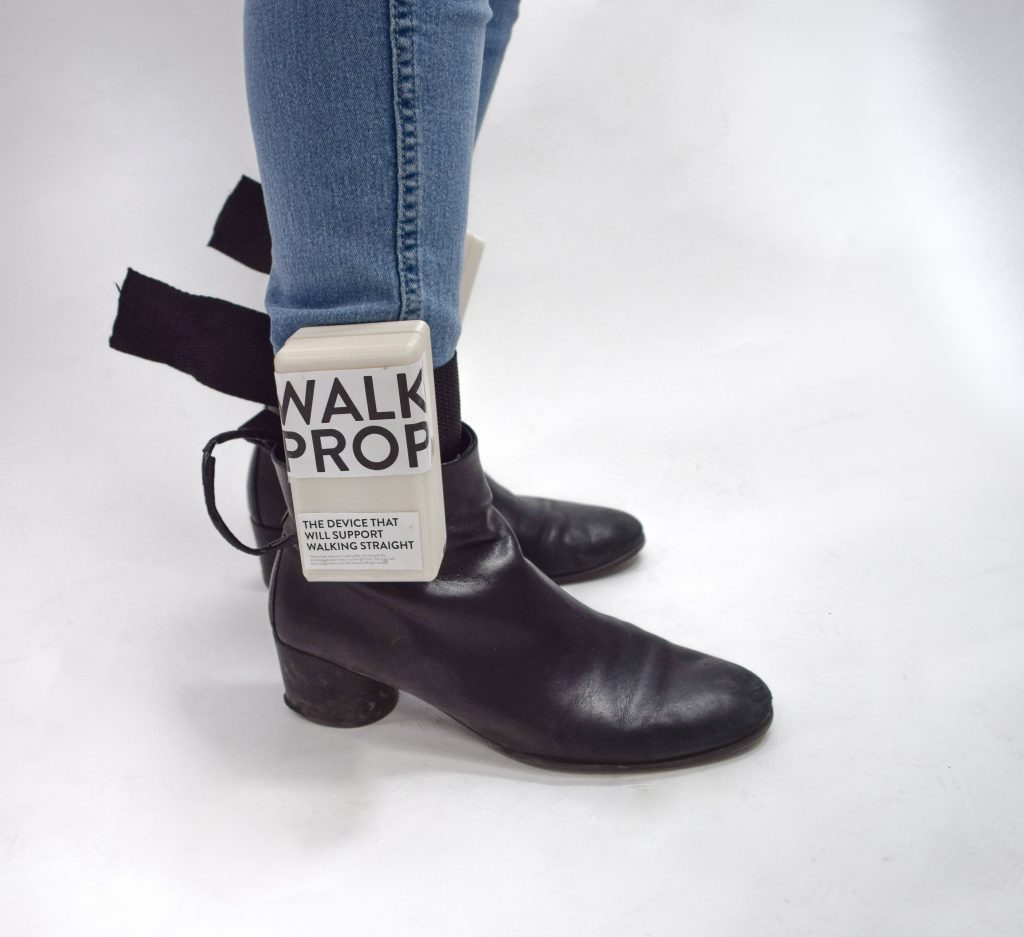
Wearing the device
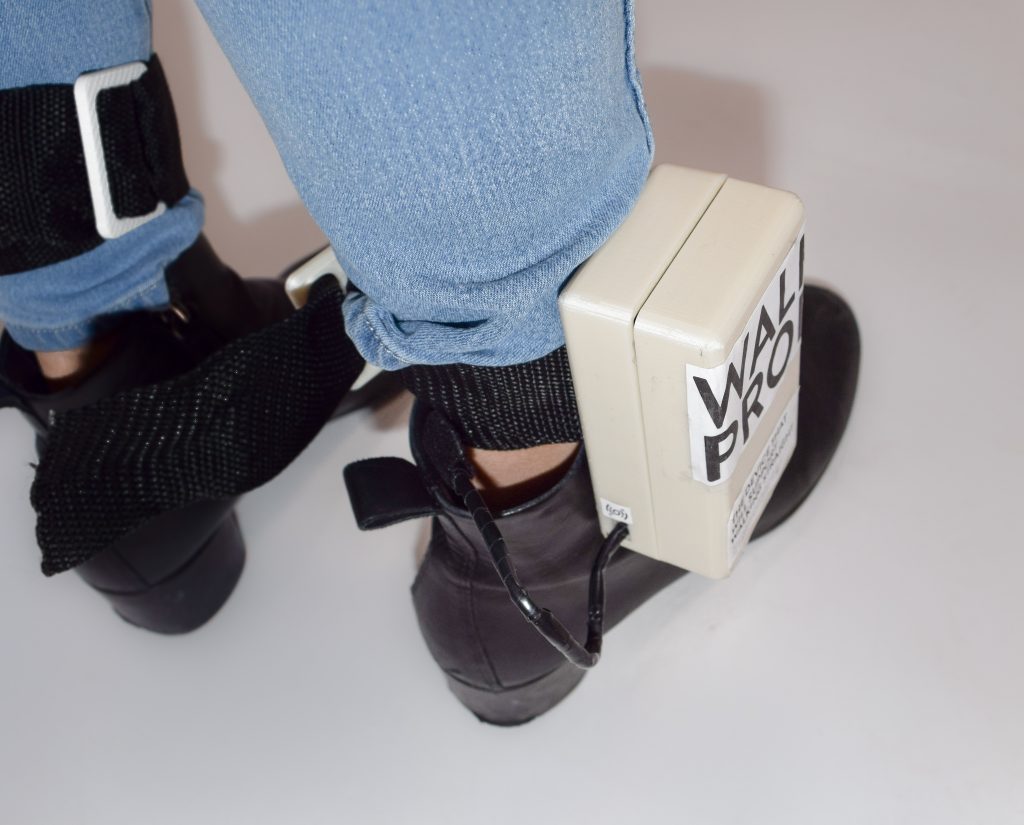
How the vibration motor would be placed inside a shoe
Process images and review
These are two of the major decision points in my progress that impacted the end result of my project.
- The Arduino Uno and Arduino Pro Mini Situation:
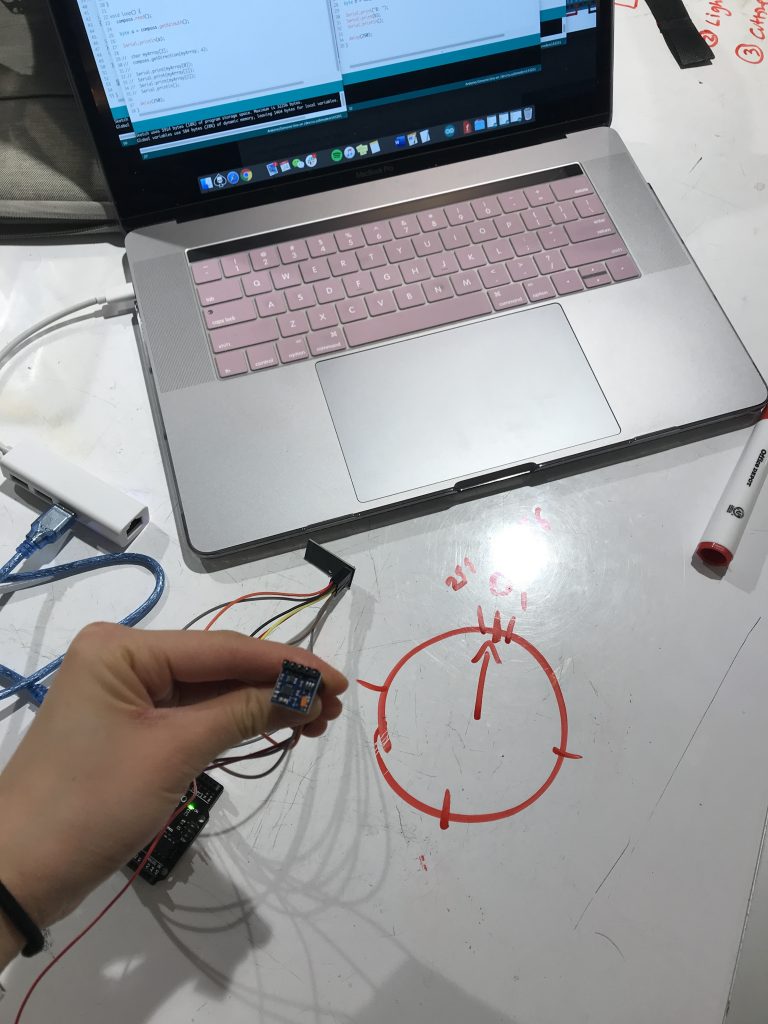
The magnetometer acts as a compass
I started this project with wiring two GY 271 magnetometers and my plan was to code for the magnetometers so that they would read the direction of where they were turned (on one plane) just like a compass. From this, I learned that to communicate between the two magnetometers, the more effective option would be to use transmitters and to separate them onto two Arduinos.
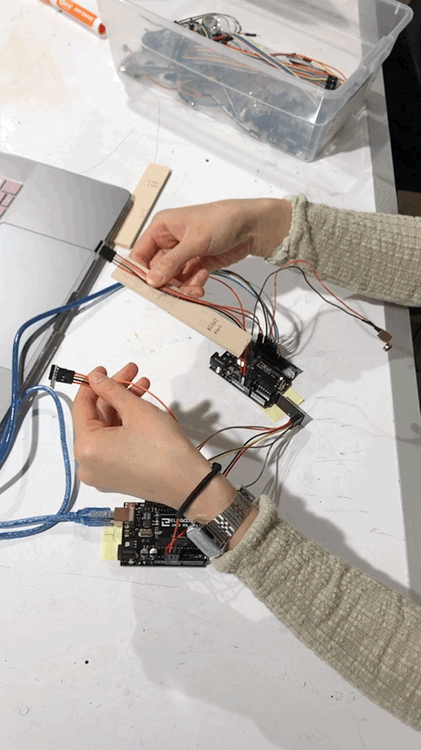
Prototype of device with magnetometer, transmitter and vibration motor
This prompted me to use the smaller Arduino Pro Minis to replace the larger Arduino Uno, hoping to make my device more comfortable to wear and inconspicuous on the body. I wired up the Arduino Pro Minis and was able to send my code to it, however, the feedback was jumbled and I could not receive the data of the left and right magnetometers that I would have been able see from the Arduino Uno.
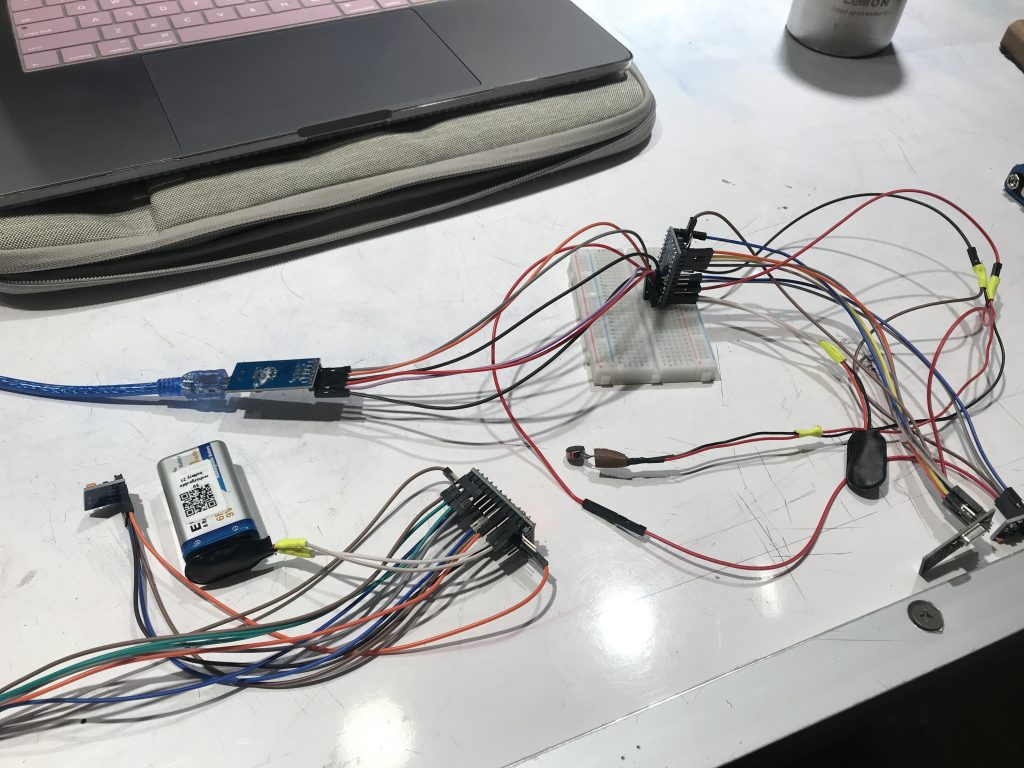
Replacing the Arduino Uno with the Arduino Pro Mini
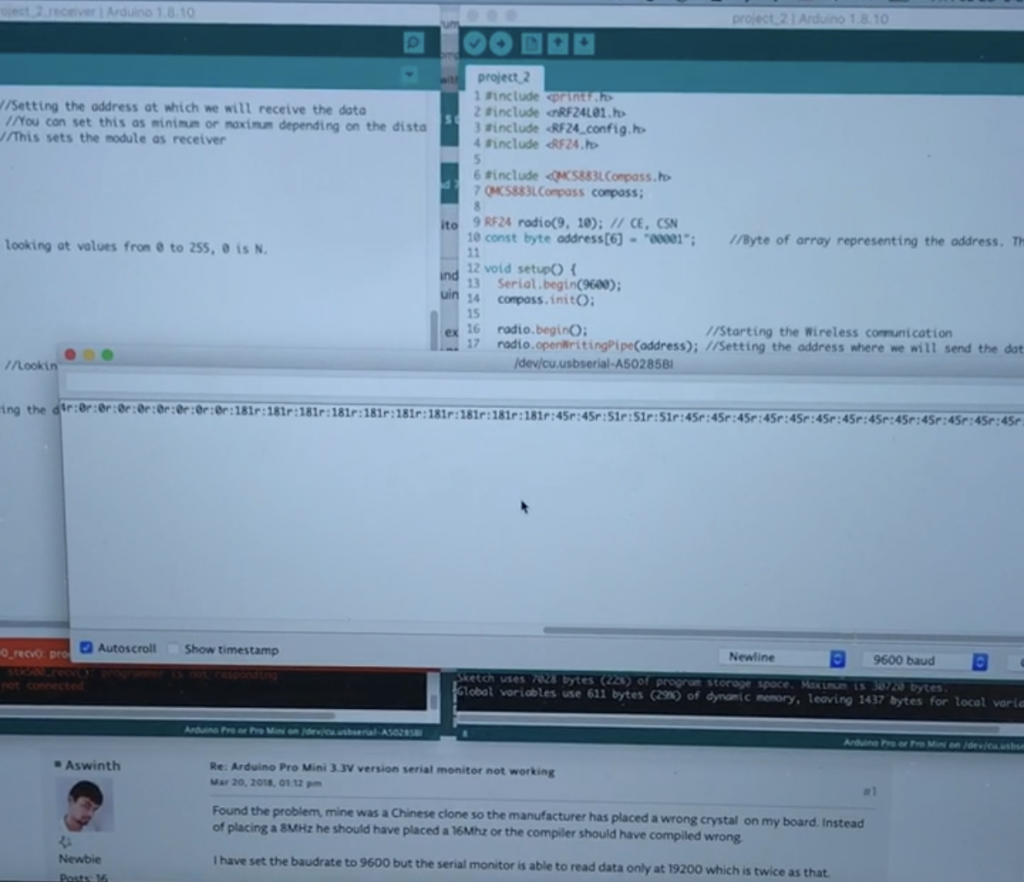
The screen shows that it is only displaying the receiving transmitter’s data (right foot) and not the transmitting one (left foot)
I spend a significant amount of time making this change to a smaller device so I tried multiple ways to resolve the problem. I asked multiple people about how I could use the Arduino Pro Mini and searched for online solutions. However, the left foot’s transmitter would not display its data. I doubled checked my wiring and replaced wires in case that that was the issue, yet the result was the same. This was the point where I decided that in order for my device to work in our limited time, I should switch back to the larger Arduino Uno.
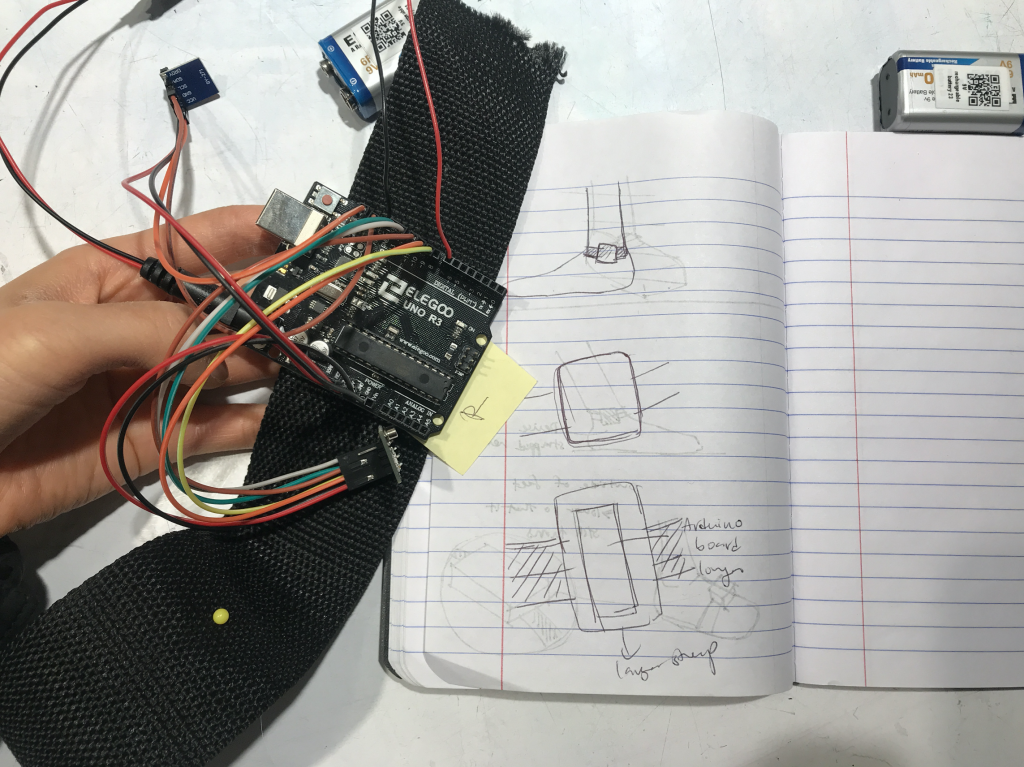
Using the Arduino Uno for the final deliverable and sketching ideas for the packaging
Working with a larger device base, I tried to condense the size as much as possible with taping Arduino components as tightly as possible together. I drew ideas for how I could package my device and I decided to 3D print a custom sized rectangular prism with rounded corners and edges to be more aesthetically pleasing (I wanted to create a minimalistic style) and user friendly to touch.
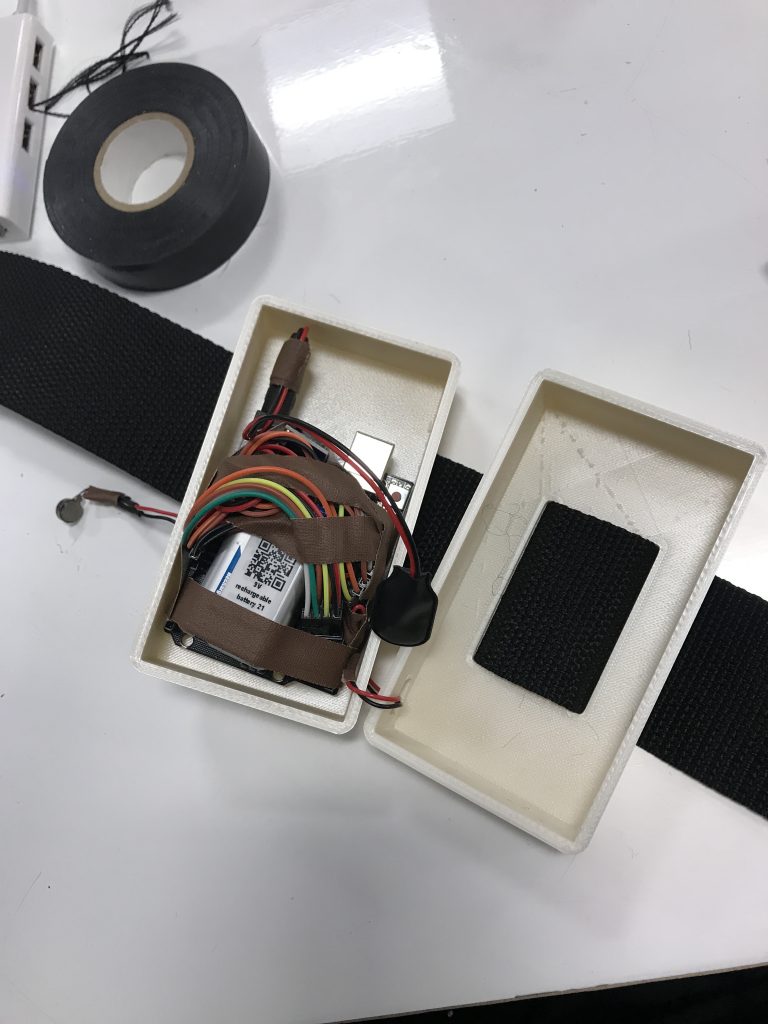
Condensing the wiring and interior as much as possible with tape to place inside its packaging
2. Changing the Code:
While I was creating the packaging for my device, I realized for the magnetometers that were connected to the Arduino Unos, the data that was being displayed was very noisy and fluctuated significantly. Even though the range of data that is coming from the magnetometers was suppose to be from 0 to 255, this was not the case in reality. This led to my second major change, where I looked for patterns in the code and calibrated the device so that the right foot (since my right foot was the one that normally doesn’t walk straight forward) needed only to be parallel to the left foot. In my code, I looked for the changes in numbers when my right foot strayed from being parallel and I used the this to signal when the vibration motors should be activated. I also included a line of code (with help from the TA) that helped reduce the noise and fluctuation of the data being received from the magnetometers to increase the accuracy of the readings.
Discussion
After completing this project, I am satisfied with what I have accomplished because I was able to learn and explore new Arduino devices that I did not know how to use before, such as the transmitter and Arduino Pro Mini. Also, I experienced the process of creating something that could be potentially used in the real world to help myself or others. I was also happy that I was able to move on with the issue over the Arduino Mini Pro and solve the situation quickly by using the Arduino Uno. Thinking back, if I dwelled on this, I would not have been able to spend time on the exterior design. Furthermore, I realized that it is much more difficult to create a useable device than I expected. If it was already so demanding to create an assistive device just for myself, it would be multiple times more difficult to create a tool for everyone. I also learned that there can also be many different obstacles that you cannot anticipate. Through this project, I learned to used the resources and knowledge that I have to adapt to situations and modify the final product according to these unexpected troubles. I think this is very relevant for the future in real world situations where these situations can happen much more often and I would need to quickly adapt and learn on the spot to face these troubles in order to find a solution.
Specifically in the making of my device. I realized that much of how to solve Arduino coding problems is to search online and learn from example codes. Before, I thought that people who were experts in Arduino would simply know what the problem is with just by looking at the code because they knew the C language, however, when I asked them about various issues I was having, they also went through the same pattern of searching online and learning on the go. This really helped me find methods on how to solve problems myself for the future. Furthermore, I was surprised by how enjoyable 3D printings was. I was not very familiar with 3D printing before and from this project, it suddenly hit me how magical and easy this can be – I simply model anything I want and I can print it in real life. Next time, I want to try to experiment with more complex exterior packaging for devices and also try different laser cutting techniques (such as laser cutting patterns on wood to allow it to bend).
I think this project really incited my interest for wearable technology. For future projects, I would want to explore e-textiles including Adafruit boards, flexible technology, and more. This would compliment my design background well.
Most people that gave feedback for my project mentioned that is was quite large and I was able to explain the reason behind this. They also enjoyed how minimalistic it was and this made me happy with my decision on how I chose to design the exterior even with its large size. If I were to further develop this project, I would spend more time investigating how I could make the device more compact (perhaps purchasing another type of board and using smaller portable batteries).
My classmates said:
“A bit bulky, but you covered why.”
“It is a little too large for what it is supposed to do”
“The design is clean and polished. The size is a bit large”
“The box is minimalist and simple”
“The project looks very clean and easy to put on”
One comment was especially interesting to me where they said that,
“you can definitely expand the product to solve all different ways of walking ‘wrong’, if you detect angles and whatnot.”
I thought that this very interesting and I think it would be a great way for me to expand my device from a more individualized use to a public one. This way, I would also be able to learn to use other Arduino components that I could use to help correct people’s walking.
Technical Information
Schematic
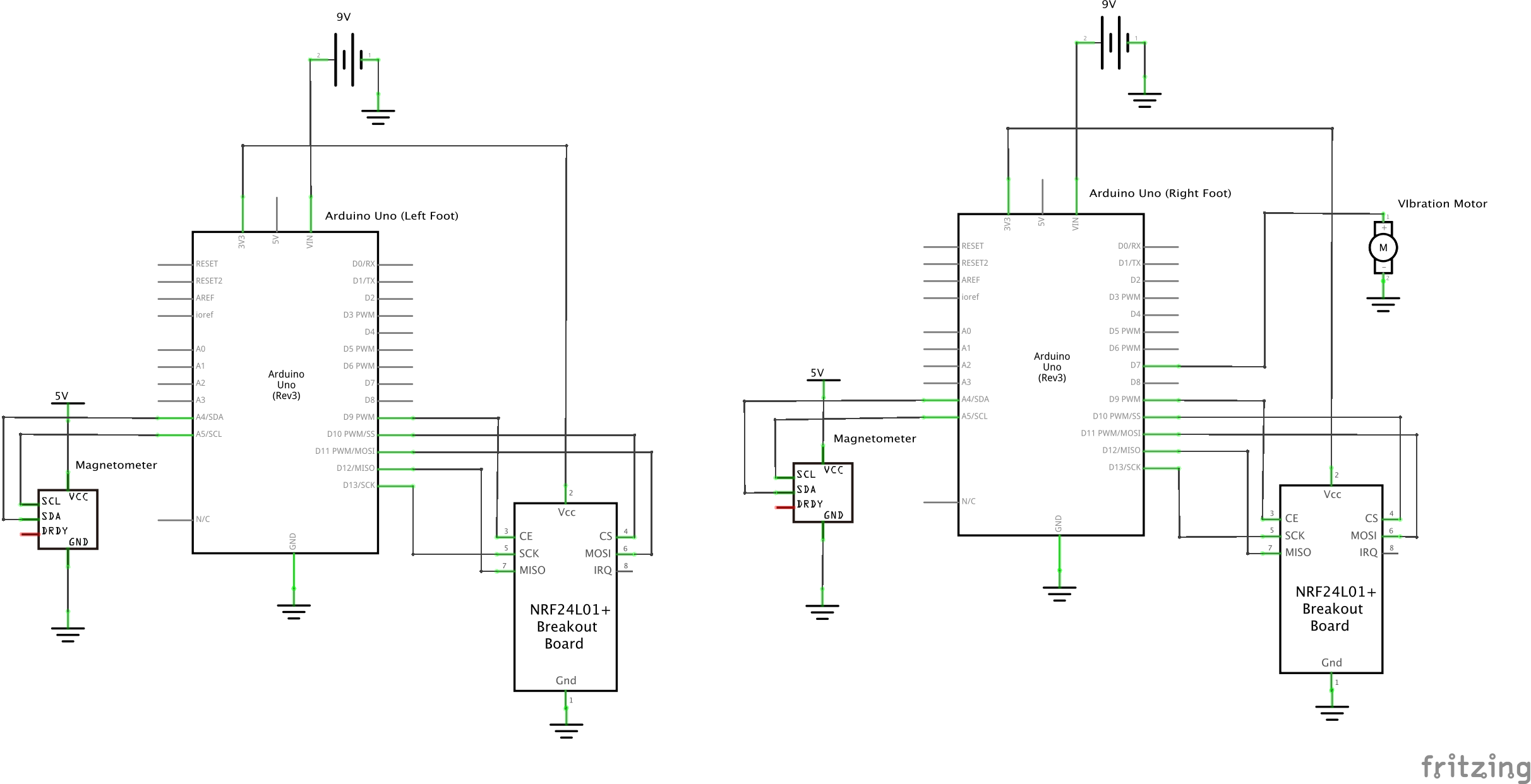
Schematic for left and right foot devices
Code
Left foot code (Transmitter)
- <span class="com">/*
- Title: WalkProp
- Author: Patricia Yu
- Description: This the code for the left foot of my device (the transmitting transceiver).
- There are two magnetometers that measure compass direction and translates this data into a number
- range from 0 to 255 (0 signifying North, however, this was not always the case as
- there was a lot of noise in the data and the transmitting data did not follow this rule).
- For the left foot's device, the transceiver RF24 will then send the data from the magnetometer
- to the receiving transceiver on the right foot. The receiving end will compare this sent data to
- its own compass' data (on the right foot) and if it is within a certain range (this limit number is gotten from
- me turning the right foot's device and seeing a pattern within the differences fo the numbers
- seeing a pattern between the right and left foot's magnetometer's data), then the feet are parallel.
- Or else, it will signify that the feet are not parallel and the vibration motor on the right foot will
- vibrate to alert the user.
- _____________________________________________________
- Pin mapping:
- pin | mode | description
- ------|--------|------------
- 09 output nRF24L01 Transceiver
- 10 output nRF24L01 Transceiver
- 11 output nRF24L01 Transceiver
- 12 output nRF24L01 Transceiver
- 13 output nRF24L01 Transceiver
- SDA/SCL input Magnetometer
- _____________________________________________________
- Credits:
- Magnotometer/Compass code library:
- QMC5883LCompass by MRPrograms
- nRF24L01 Transceiver code library:
- RF24 by TMRh20
- Transceiver wiring/code help:
- https://create.arduino.cc/projecthub/muhammad-aqib/nrf24l01-interfacing-with-arduino-wireless-communication-0c13d4
- Professor Zacharias for helping with figuring out how to set the magnetometer to be a compass
- TA Harshine for helping me with the code to reduce noise from the compass
- */</span><span class="pln">
- </span><span class="com">//Magnetometer code from library:</span><span class="pln">
- </span><span class="com">#include</span><span class="pln"> </span><span class="str"><QMC5883LCompass.h></span><span class="pln">
- QMC5883LCompass compass</span><span class="pun">;</span><span class="pln">
- </span><span class="com">//RF24 code from library:</span><span class="pln">
- </span><span class="com">#include</span><span class="pln"> </span><span class="str"><printf.h></span><span class="pln">
- </span><span class="com">#include</span><span class="pln"> </span><span class="str"><nRF24L01.h></span><span class="pln">
- </span><span class="com">#include</span><span class="pln"> </span><span class="str"><RF24_config.h></span><span class="pln">
- </span><span class="com">#include</span><span class="pln"> </span><span class="str"><RF24.h></span><span class="pln">
- RF24 radio</span><span class="pun">(</span><span class="lit">9</span><span class="pun">,</span><span class="pln"> </span><span class="lit">10</span><span class="pun">);</span><span class="pln"> </span><span class="com">// CE, CSN</span><span class="pln">
- </span><span class="kwd">const</span><span class="pln"> </span><span class="kwd">byte</span><span class="pln"> address</span><span class="pun">[</span><span class="lit">6</span><span class="pun">]</span><span class="pln"> </span><span class="pun">=</span><span class="pln"> </span><span class="str">"00001"</span><span class="pun">;</span><span class="pln"> </span><span class="com">//Byte of array representing the address. This is the address where we will send the data. This should be same on the receiving side.</span><span class="pln">
- </span><span class="kwd">byte</span><span class="pln"> t </span><span class="pun">=</span><span class="pln"> </span><span class="lit">0</span><span class="pun">;</span><span class="pln">
- </span><span class="kwd">void</span><span class="pln"> setup</span><span class="pun">()</span><span class="pln"> </span><span class="pun">{</span><span class="pln">
- </span><span class="typ">Serial</span><span class="pun">.</span><span class="kwd">begin</span><span class="pun">(</span><span class="lit">9600</span><span class="pun">);</span><span class="pln">
- compass</span><span class="pun">.</span><span class="pln">init</span><span class="pun">();</span><span class="pln"> </span><span class="com">//setup for magnetometer</span><span class="pln">
- </span><span class="com">//setup for transceiver:</span><span class="pln">
- radio</span><span class="pun">.</span><span class="kwd">begin</span><span class="pun">();</span><span class="pln"> </span><span class="com">//Starting the Wireless communication</span><span class="pln">
- radio</span><span class="pun">.</span><span class="pln">openWritingPipe</span><span class="pun">(</span><span class="pln">address</span><span class="pun">);</span><span class="pln"> </span><span class="com">//Setting the address where we will send the data</span><span class="pln">
- radio</span><span class="pun">.</span><span class="pln">setPALevel</span><span class="pun">(</span><span class="pln">RF24_PA_HIGH</span><span class="pun">);</span><span class="pln"> </span><span class="com">//You can set it as minimum or maximum depending on the distance between the transmitter and receiver.</span><span class="pln">
- radio</span><span class="pun">.</span><span class="pln">stopListening</span><span class="pun">();</span><span class="pln"> </span><span class="com">//This sets the module as transmitter</span><span class="pln">
- </span><span class="pun">}</span><span class="pln">
- </span><span class="kwd">void</span><span class="pln"> loop</span><span class="pun">()</span><span class="pln"> </span><span class="pun">{</span><span class="pln">
- </span><span class="com">// Read compass values in directions looking at values from 0 to 255, 0 is suppose to be N.</span><span class="pln">
- compass</span><span class="pun">.</span><span class="pln">read</span><span class="pun">();</span><span class="pln">
- t </span><span class="pun">=</span><span class="pln"> </span><span class="pun">(.</span><span class="lit">9</span><span class="pun">)</span><span class="pln"> </span><span class="pun">*</span><span class="pln"> </span><span class="pun">(</span><span class="pln">t</span><span class="pun">)</span><span class="pln"> </span><span class="pun">+</span><span class="pln"> </span><span class="pun">(</span><span class="lit">0.1</span><span class="pun">)</span><span class="pln"> </span><span class="pun">*</span><span class="pln"> </span><span class="pun">(</span><span class="pln">compass</span><span class="pun">.</span><span class="pln">getAzimuth</span><span class="pun">());</span><span class="pln"> </span><span class="com">// to reduce noise when receiving compass data from Transmitter</span><span class="pln">
- radio</span><span class="pun">.</span><span class="pln">write</span><span class="pun">(&</span><span class="pln">t</span><span class="pun">,</span><span class="pln"> </span><span class="kwd">sizeof</span><span class="pun">(</span><span class="pln">t</span><span class="pun">));</span><span class="pln"> </span><span class="com">//Sending the message to receiver</span><span class="pln">
- delay</span><span class="pun">(</span><span class="lit">5</span><span class="pun">);</span><span class="pln">
- </span><span class="pun">}</span>
Right foot code (Receiver)
- <span class="com">/*
- Title: WalkProp
- Author: Patricia Yu
- Description: This the code for the right foot of my device (the receiving transceiver).
- There are two magnetometers that measure compass direction and translates this data into a number
- range from 0 to 255 (0 signifying North, however, this was not always the case as
- there was a lot of noise in the data and the transmitting data did not follow this rule).
- For the right foot's device, the transceiver RF24 fromt he left foot will send the data from the magnetometer
- to the receiving transceiver on the right foot. The receiving end will compare this sent data to
- its own compass' data (on the right foot) and if it is within a certain range (this limit number is gotten from
- me turning the right foot's device and seeing a pattern within the differences fo the numbers
- seeing a pattern between the right and left foot's magnetometer's data), then the feet are parallel. Or else, it will signify that
- the feet are not parallel and the vibration motor on the right foot will vibrate to alert the user.
- _____________________________________________________
- Pin mapping:
- pin | mode | description
- ------|--------|------------
- 09 output nRF24L01 Transceiver
- 10 output nRF24L01 Transceiver
- 11 output nRF24L01 Transceiver
- 12 output nRF24L01 Transceiver
- 13 output nRF24L01 Transceiver
- SDA/SCL input Magnetometer
- 07 output vibration motor
- _____________________________________________________
- Credits:
- Magnotometer/Compass code library:
- QMC5883LCompass by MRPrograms
- nRF24L01 Transceiver code library:
- RF24 by TMRh20
- Transceiver wiring/code help:
- https://create.arduino.cc/projecthub/muhammad-aqib/nrf24l01-interfacing-with-arduino-wireless-communication-0c13d4
- Professor Zacharias for helping with figuring out how to set the magnetometer to be a compass
- */</span><span class="pln">
- </span><span class="com">//Magnetometer code from library:</span><span class="pln">
- </span><span class="com">#include</span><span class="pln"> </span><span class="str"><QMC5883LCompass.h></span><span class="pln">
- QMC5883LCompass compass</span><span class="pun">;</span><span class="pln">
- </span><span class="com">//RF24 code from library:</span><span class="pln">
- </span><span class="com">#include</span><span class="pln"> </span><span class="str"><printf.h></span><span class="pln">
- </span><span class="com">#include</span><span class="pln"> </span><span class="str"><nRF24L01.h></span><span class="pln">
- </span><span class="com">#include</span><span class="pln"> </span><span class="str"><RF24_config.h></span><span class="pln">
- </span><span class="com">#include</span><span class="pln"> </span><span class="str"><RF24.h></span><span class="pln">
- RF24 radio</span><span class="pun">(</span><span class="lit">9</span><span class="pun">,</span><span class="pln"> </span><span class="lit">10</span><span class="pun">);</span><span class="pln"> </span><span class="com">// CE, CSN</span><span class="pln">
- </span><span class="kwd">const</span><span class="pln"> </span><span class="kwd">byte</span><span class="pln"> address</span><span class="pun">[</span><span class="lit">6</span><span class="pun">]</span><span class="pln"> </span><span class="pun">=</span><span class="pln"> </span><span class="str">"00001"</span><span class="pun">;</span><span class="pln">
- </span><span class="kwd">int</span><span class="pln"> angle</span><span class="pun">;</span><span class="pln"> </span><span class="com">//angle is the number that will be used to set a range for when the vibration motor is activated</span><span class="pln">
- </span><span class="kwd">const</span><span class="pln"> </span><span class="kwd">int</span><span class="pln"> VIBRATE </span><span class="pun">=</span><span class="pln"> </span><span class="lit">7</span><span class="pun">;</span><span class="pln"> </span><span class="com">// vibration motor pin</span><span class="pln">
- </span><span class="kwd">void</span><span class="pln"> setup</span><span class="pun">()</span><span class="pln"> </span><span class="pun">{</span><span class="pln">
- </span><span class="typ">Serial</span><span class="pun">.</span><span class="kwd">begin</span><span class="pun">(</span><span class="lit">9600</span><span class="pun">);</span><span class="pln">
- compass</span><span class="pun">.</span><span class="pln">init</span><span class="pun">();</span><span class="pln"> </span><span class="com">//setup for magnetometer</span><span class="pln">
- pinMode</span><span class="pun">(</span><span class="pln">VIBRATE</span><span class="pun">,</span><span class="pln"> OUTPUT</span><span class="pun">);</span><span class="pln">
- </span><span class="com">//setup for transceiver:</span><span class="pln">
- radio</span><span class="pun">.</span><span class="kwd">begin</span><span class="pun">();</span><span class="pln">
- radio</span><span class="pun">.</span><span class="pln">openReadingPipe</span><span class="pun">(</span><span class="lit">0</span><span class="pun">,</span><span class="pln"> address</span><span class="pun">);</span><span class="pln"> </span><span class="com">//Setting the address at which we will receive the data</span><span class="pln">
- radio</span><span class="pun">.</span><span class="pln">setPALevel</span><span class="pun">(</span><span class="pln">RF24_PA_HIGH</span><span class="pun">);</span><span class="pln"> </span><span class="com">//You can set this as minimum or maximum depending on the distance between the transmitter and receiver.</span><span class="pln">
- radio</span><span class="pun">.</span><span class="pln">startListening</span><span class="pun">();</span><span class="pln"> </span><span class="com">//This sets the module as receiver</span><span class="pln">
- </span><span class="pun">}</span><span class="pln">
- </span><span class="kwd">void</span><span class="pln"> loop</span><span class="pun">()</span><span class="pln"> </span><span class="pun">{</span><span class="pln">
- </span><span class="com">// Read compass values in directions looking at values from 0 to 255, 0 is suppose to be N.</span><span class="pln">
- compass</span><span class="pun">.</span><span class="pln">read</span><span class="pun">();</span><span class="pln">
- delay</span><span class="pun">(</span><span class="lit">5</span><span class="pun">);</span><span class="pln">
- </span><span class="kwd">byte</span><span class="pln"> r </span><span class="pun">=</span><span class="pln"> compass</span><span class="pun">.</span><span class="pln">getAzimuth</span><span class="pun">();</span><span class="pln"> </span><span class="com">//compass data from Receiver</span><span class="pln">
- </span><span class="typ">Serial</span><span class="pun">.</span><span class="kwd">print</span><span class="pun">(</span><span class="str">"r:"</span><span class="pun">);</span><span class="pln">
- </span><span class="typ">Serial</span><span class="pun">.</span><span class="kwd">print</span><span class="pun">(</span><span class="pln">r</span><span class="pun">);</span><span class="pln">
- delay </span><span class="pun">(</span><span class="lit">500</span><span class="pun">);</span><span class="pln">
- </span><span class="kwd">if</span><span class="pln"> </span><span class="pun">(</span><span class="pln">radio</span><span class="pun">.</span><span class="pln">available</span><span class="pun">())</span><span class="pln"> </span><span class="com">//Looking for the data.</span><span class="pln">
- </span><span class="pun">{</span><span class="pln">
- </span><span class="kwd">int</span><span class="pln"> t</span><span class="pun">;</span><span class="pln">
- radio</span><span class="pun">.</span><span class="pln">read</span><span class="pun">(&</span><span class="pln">t</span><span class="pun">,</span><span class="pln"> </span><span class="kwd">sizeof</span><span class="pun">(</span><span class="pln">t</span><span class="pun">));</span><span class="pln"> </span><span class="com">//Reading the data from Transmitter</span><span class="pln">
- </span><span class="typ">Serial</span><span class="pun">.</span><span class="kwd">print</span><span class="pun">(</span><span class="str">" t:"</span><span class="pun">);</span><span class="pln">
- </span><span class="typ">Serial</span><span class="pun">.</span><span class="pln">println</span><span class="pun">(</span><span class="pln">t</span><span class="pun">);</span><span class="pln">
- </span><span class="com">// using the difference between the angles of magnetometers to detect when angles of feet are changed to indicate if they are parallel or not</span><span class="pln">
- angle </span><span class="pun">=</span><span class="pln"> </span><span class="pun">(</span><span class="pln">t </span><span class="pun">-</span><span class="pln"> r</span><span class="pun">);</span><span class="pln">
- angle </span><span class="pun">=</span><span class="pln"> abs</span><span class="pun">(</span><span class="pln">angle</span><span class="pun">);</span><span class="pln">
- </span><span class="pun">}</span><span class="pln">
- </span><span class="com">// if the angle between the two devices are over a certain calibrated debree, the vibration motor will signal the user to adjust their feet position</span><span class="pln">
- </span><span class="kwd">if</span><span class="pln"> </span><span class="pun">(</span><span class="pln">angle </span><span class="pun">>=</span><span class="pln"> </span><span class="lit">70</span><span class="pln"> </span><span class="pun">)</span><span class="pln"> </span><span class="pun">{</span><span class="pln">
- digitalWrite</span><span class="pun">(</span><span class="pln">VIBRATE</span><span class="pun">,</span><span class="pln"> HIGH</span><span class="pun">);</span><span class="pln">
- </span><span class="pun">}</span><span class="pln">
- </span><span class="kwd">else</span><span class="pln"> </span><span class="pun">{</span><span class="pln">
- digitalWrite</span><span class="pun">(</span><span class="pln">VIBRATE</span><span class="pun">,</span><span class="pln"> LOW</span><span class="pun">);</span><span class="pln">
- </span><span class="pun">}</span><span class="pln">
- </span><span class="pun">}</span>
Comments are closed.