Team: Yu Jiang & Max Kornyev
Technical Plan
Our objectives for the first proof-of-concept demonstration are the following.
- A functional set of laser-cut maze components; including the press-fit maze walls, the three maze Shielding Boxes, and their working assembly.
- A functional set of Sonar Sensors with smoothed input; such that it is possible to control the two maze axes with your hands.
Once we make good headway on these objectives, we will move on to implementing some additional features.
- A mobile app to interface with the CKS server using the paho.mqtt client. The app will run on the iOS platform.
- Introducing remote input modes to the application; via distant sonars or mobile phones.
Unknowns and Contingencies
- Stability of the three-box maze structure – we will need to be mindful of the structure’s weight, in order to minimize strain on our Servo motors. If this becomes an issue, we can make the maze smaller, use an arm to pivot boxes on their axes, or increase the number of motors used.
- Ranger input uncertainty – sonar rangers are not perfect, and have high potential to ruin the user experience with consistently faulty readings. We will need to spend additional time on ensuring a smooth tilt of the servo.
- Mobile application uncertainty – developing the application may be time consuming. And because the paho.mqtt client is not directly available in iOS, the app may require an additional information layer to pass on application input to the CKS server.
- Latency issues – This is just a consequence of Remote communication, and is something we have to be mindful of when testing the user experience.
Project Management
Designated individual responsibilities, as applicable.
- Create a simple system circuit diagram – Max
- Create the first maze design using Fusion360 – Yu
- Cut & assemble the parts, make design changes as needed – Team
- Write code to parse range sensor input and control the Servo arm appropriately – Max
- Test the hands free interactions and make changes as needed – Team
- Refactor code to accept remote input – Yu
- Create / deploy mobile app – Team / Max for deployment
Remote collaboration will be primarily planned via Facebook Messenger. While our weekly meetings can be held throughout the week and on weekends; at 9AM or 9PM in either timezone.
Bill of Materials
Component | Quantity | Kit parts expected to be used | Acquired parts | Design and fabrication method |
Base ground | 1 | none | plywood | CAD design and laser cutting |
Wires and Power Source | 1 | 5V battery, breadboard, resistors, UNO R3 controller board, screws, wires | plywood | CAD design and laser cutting |
Sensor station | 1 | One ultrasonic sensor, breadboards, wires | plywood, an ultrasonic sensor | CAD design and laser cutting |
Marble receiver | 1 | none | plywood | CAD design and laser cutting |
Marble sensor | 1 | optical proximity sensor, breadboard | plywood | CAD design and laser cutting |
Rotation unit | 2 | hobby servos, popsicle sticks, paper clips, shoulder screws, bush bearings, unthreaded spacers, hex nuts, wires | none | Drill parts and assemble |
Shield box | 3 | none | plywood | CAD design and laser cutting |
Game board | 1 | optical proximity sensor, breadboard, LED | plywood | CAD design and laser cutting |
Tilted marble board | 1 | none | plywood | CAD design and laser cutting |
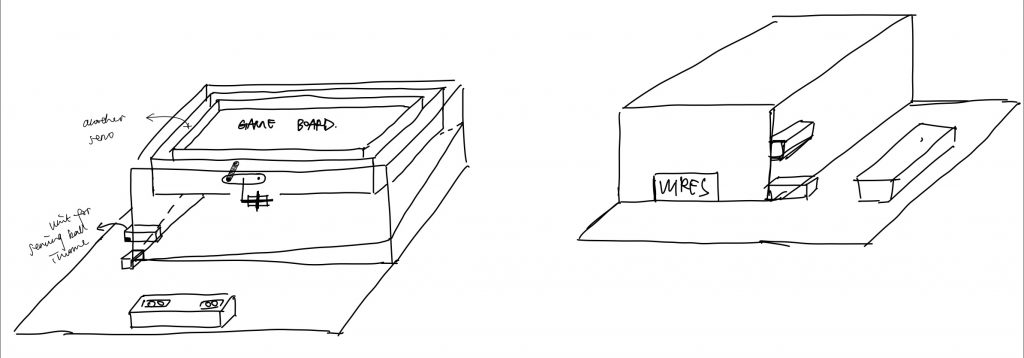
updated sketch
Leave a Reply
You must be logged in to post a comment.