- Conceptual Statement
Our piece invites two viewers to work together to teleoperate a helpless two-legged crawling robot traversing a children’s sandbox. Together they inhabit its body; each controlling a single one of the robot’s legs, it can only march forward if the two operators synchronize their motions. Each operator’s controller communicates what forces the robot is feeling back to the operator. If the leg is dragging through the viscous sand, the operator will feel the resistance. If the leg is swinging freely through the air, the operators will feel that too. If the two operators are successful in interpreting these motions and forces, they will create a single, unified nervous system for this little machine.
2. Additional Notes
Sand environment:
We believe the choice of a sandbox for the robot’s environment will create a rich sense of tactile feedback for each operator. As the robot goes through its gait cycle, the operator will feel a range of forces, from free low-resistance swinging through the air, to hard “slapping” contacts against the ground, to slow, viscous high-resistance dragging through the sand.
3. Concept Sketches
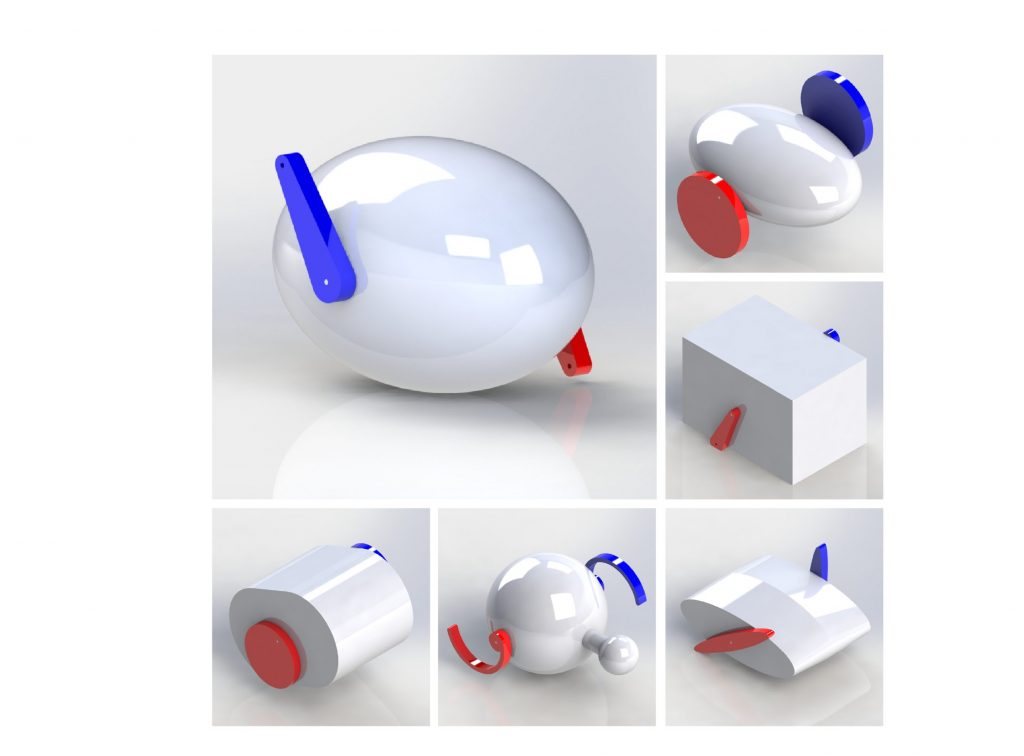
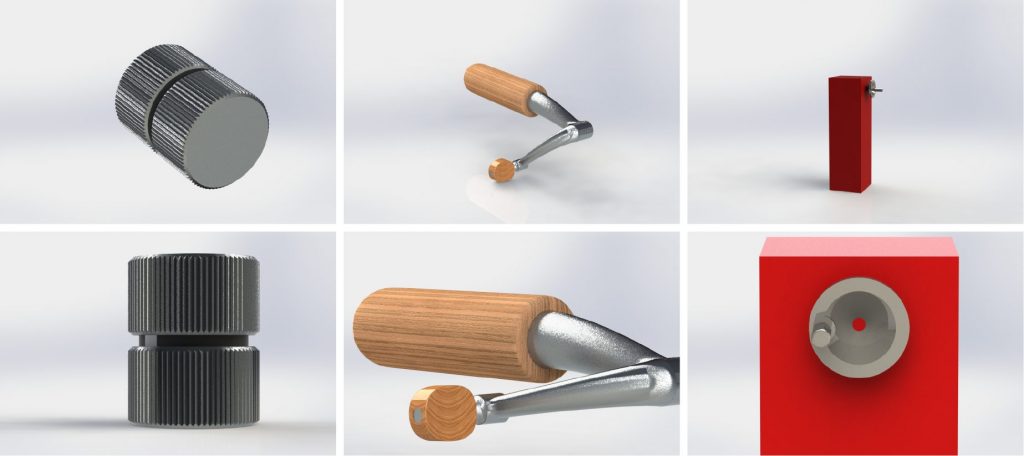
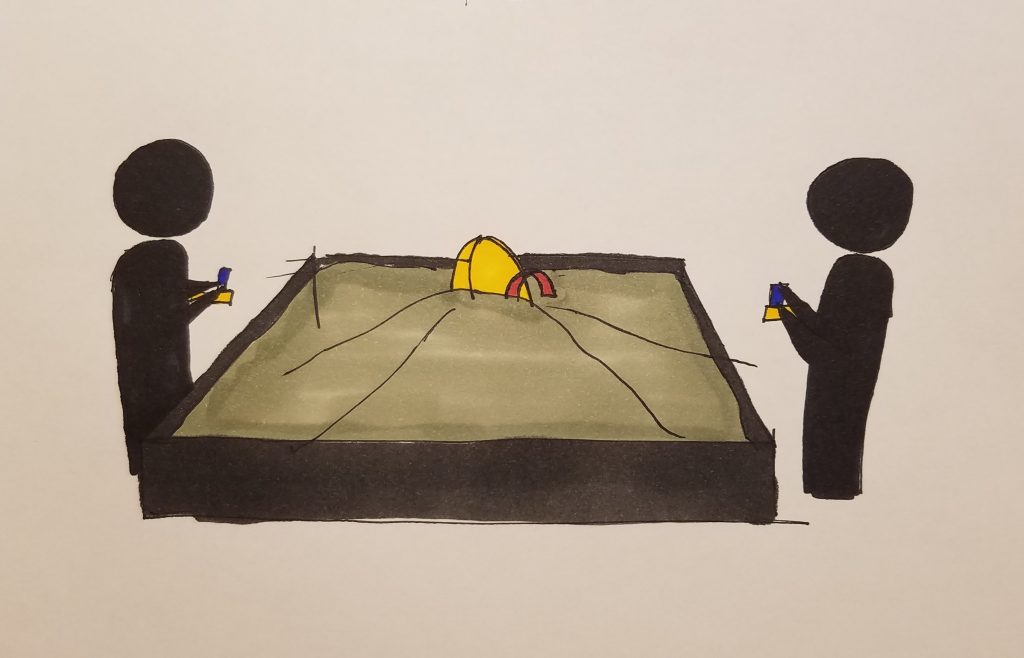
Two people driving the robot up a hill in a sandbox.
Note that the handle on one of the controllers should be red, not blue.
4. Technical Resources
For this project there is a wealth of resources on hobbyist sites for taking cheap widely available BLDC (Brushless DC) motors and adding high-resolution encoding and current-sensing in order to do the force control we want.
Motors
Due to time constraints we are limited to what is quickly available on amazon/eBay. Electric skateboard motors meet the low speed and high torque requirements we want, and are widely available. We would like to start with a motor that has an abundance of torque, so that we never run into stalling issues. For prototypes like this it is always easier to lower the torque in software than it is to buy all new motors with extra torque. One candidate is shown below: (Note: the motor as is is sensorless so we would need to couple it to an encoder to make it work).
Motor Control:
https://odriverobotics.com/ has a suitable motor controller that is shipped from the U.S. and provides force control features. Also Joey is familiar with using it, and the manufacturer has good documentation and online support.
Tying it all together:
The odrive board has a very low amount of overhead, so the only other components we would need is a laptop (communicating with each board over USB), or a microcontroller like a Teensy or Arduino (communicating over UART).
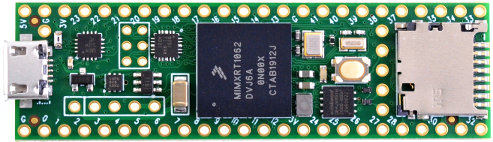
5. Pandemic Contingency Plan
If the CMU machine shops close, we can focus on building the joysticks in hardware, using largely 3d printed components, and creating a simulation environment to control the robot in.
Comments are closed.