Project Summary
Our project is an actuating silicone hand. Each finger’s large movements will be powered via pneumatic pumps, and current-driven nitinol wire will fine-tune these movements. The finger will be cast in two parts out of silicone and fused together; afterwards, trained nitinol will be strategically guided into the cured silicone, with wire leads attached to a current supply coming out of the base (see sketches below).
Updated Sketches
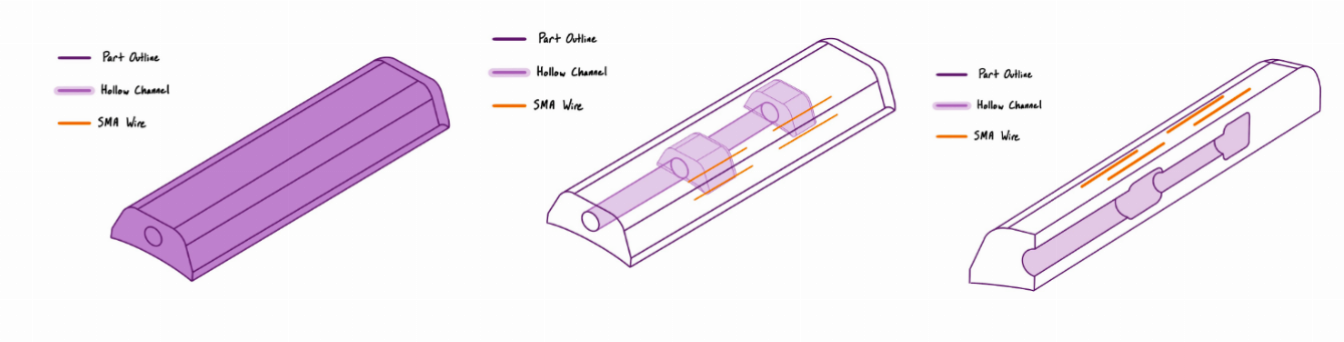
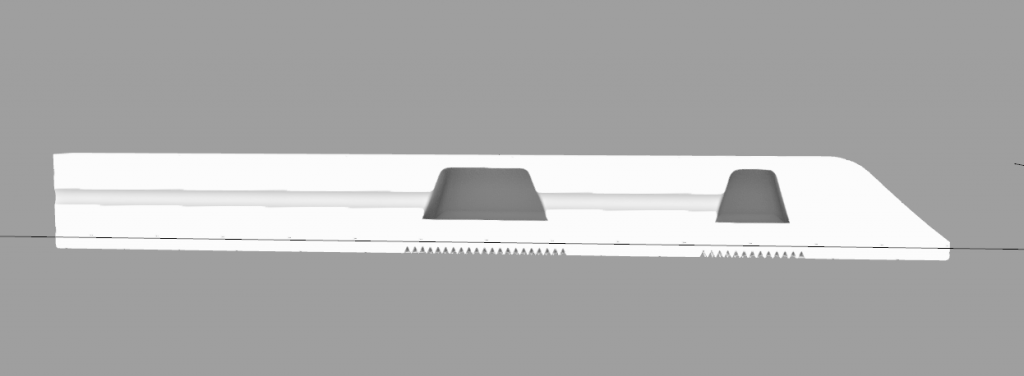
First Experiment Summary
Our first experiment will be broken down into two parts:
Part 1 – Silicone Casting
We were able to “successfully” cast our part in silicone, however, the 3D print failed about ⅔ of the way through. We hope that our first iteration will allow us to test the design in terms of functionality, however, we still want to test our full design.
Part 2 – SMA Training
The second half of our first experiment involves us both getting used to working with and training Shape Memory Alloys (SMA). We have samples, and want to practice heating them up to remember bent shapes, as well as use this trial and error to choose a specific gauge to embed in our part.
Reference
M. N. Golchin, A. Hadi and B. Tarvirdizadeh. Development of A New Soft Robotic Module Using Compressed Air and Shape Memory Alloys. In 2021 9th RSI International Conference on Robotics and Mechatronics (ICRoM), Tehran, Iran, Islamic Republic of. 517-522. https://doi.org/10.1109/ICRoM54204.2021.9663519