Elise Chapman and Leah Walko
Project Objectives:
To imitate a living organism that reacts to human touch/proximity by way of group movement. The organism reactions should feel organic and unpredictable, engaging the audience.
Reflection on the Creative Design Opportunities:
We embraced the use of silicon, pneumatic actuation, and capacitive touch sensing to create a feeling of movement and mysticism in the piece. The silicon paired particularly well with the capacitive touch sensing while embedding the necessary wires into the individual silicon tentacles. Then our inflation technique, while simple, was effective in creating the desired movement.
Unfortunately due to 3D printer problems, the shape of the individual tentacles was quite blocky as opposed to our ideal, more rounded shape. However, we were able to effectively counteract this inorganic feeling through our use of color and environment staging. The 1-to-2 pink to orange gradient in fluorescent colors mimicked real sea anemone in a very productive way. Additionally, the off-white clay placed around the base of the anemone brought a natural texture to the surroundings.
Outcomes:
We are quite pleased with how our piece turned out. Our audience was surprised and delighted by the interactions with anemone. The color was especially well received as people had not seen silicon cast as a gradient before. They were particularly excited by one of the tentacles that had a lot of movement. The box also worked well by creating a “blank” display space, while also, of course, hiding all of our extra wires. The natural environmental quality was also not lost due to the space at the top of the box being made into a rough terrain. Serendipitously, the motors’ noises played a fun part in the final exhibition, with some audience members asking if the sounds were intentionally included.
The motors, however, did initially pose a challenge to us. They could not vacuum air out as advertised, so we had to find a work-around to still drain air out of the tentacles. In the end, we poked holes in the tubing itself to create intentional air leaks. This worked very well, the deflation process appeared very natural.
Another large issue for us was the defunct 3D printers, limiting what our shapes could be to our first iteration mold. However, as mentioned above, that seemed to also work out. A notable comment by an audience member was that they liked the shape because it felt more “crystalline”, amplifying the surprise and mysticism when the anemone would start to inflate.
Citations
K. Suzumori, S. Iikura and H. Tanaka, “Development of flexible microactuator and its applications to robotic mechanisms,” Proceedings. 1991 IEEE International Conference on Robotics and Automation, Sacramento, CA, USA, 1991, pp. 1622-1627 vol.2, doi: 10.1109/ROBOT.1991.131850.
Qi Wang, Zhenhua Wu, Jianyu Huang, Zhuolin Du, Yamei Yue, Dezhi Chen, Dong Li, Bin Su. Integration of sensing and shape-deforming capabilities for a bioinspired soft robot. In Composites Part B: Engineering, Volume 223, 15 October 2021, doi: 10.1016/j.compositesb.2021.109116.
T. Wang, Y. Zhang, Z. Zhu and S. Zhu, “An Electrohydraulic Control Device With Decoupling Effect for Three-Chamber Soft Actuators,” in IEEE/ASME Transactions on Mechatronics, vol. 27, no. 3, pp. 1683-1691, June 2022, doi: 10.1109/TMECH.2021.3087196.
Technical Documentation
Code:
CAD Files
Photographs
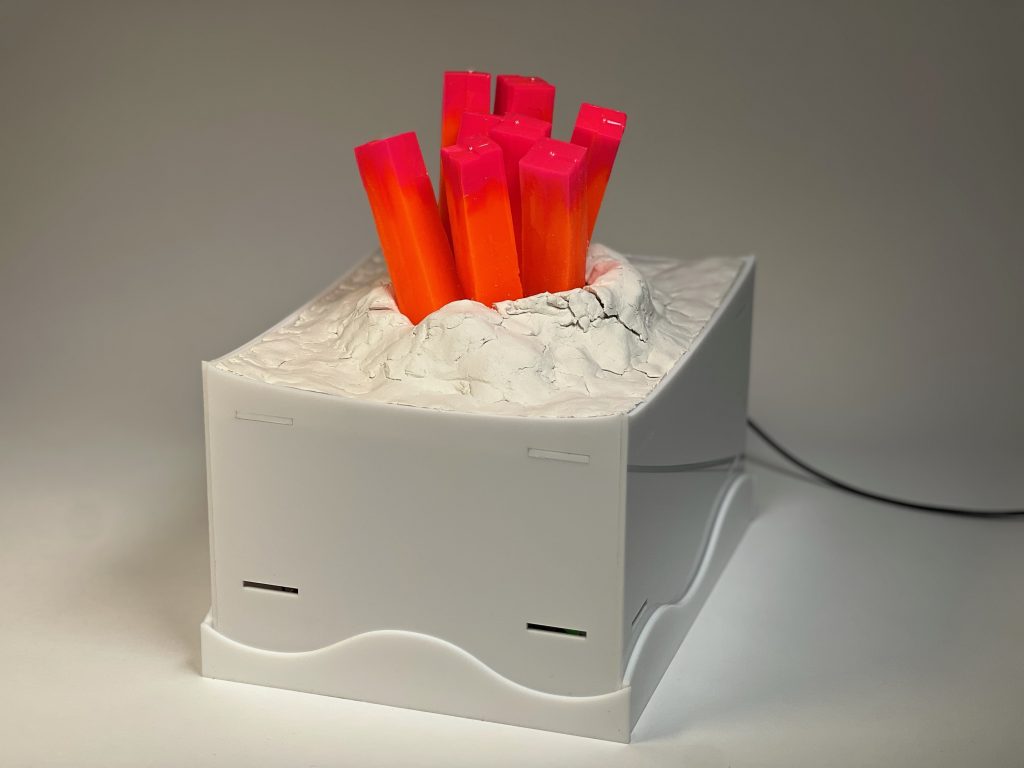
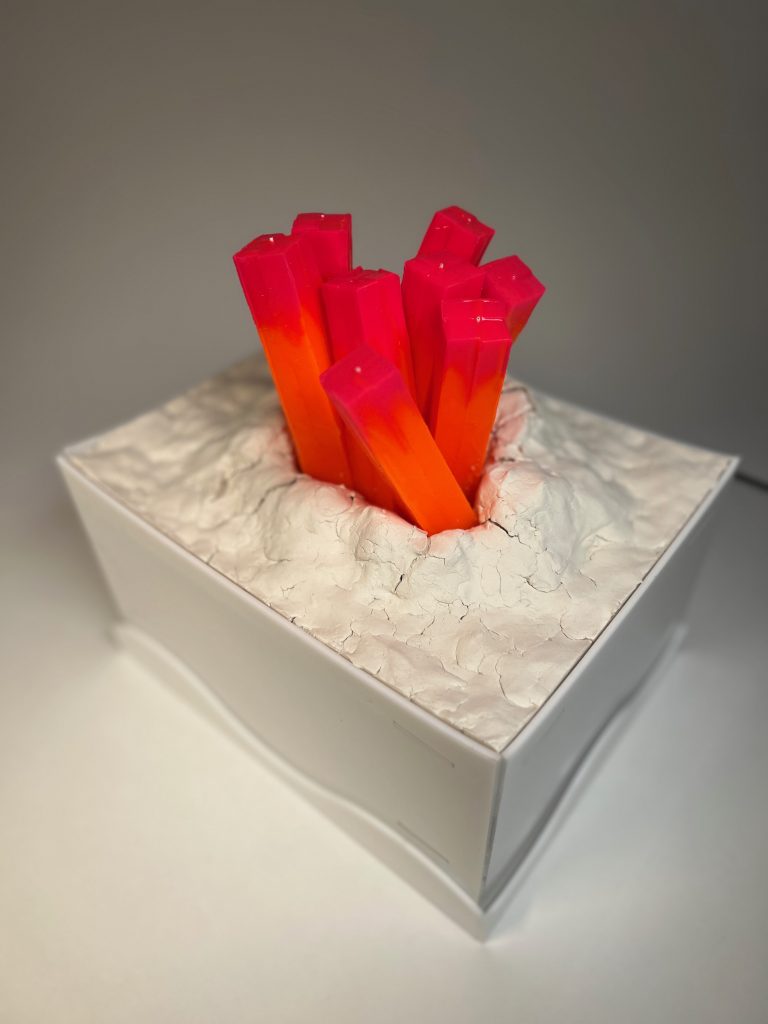
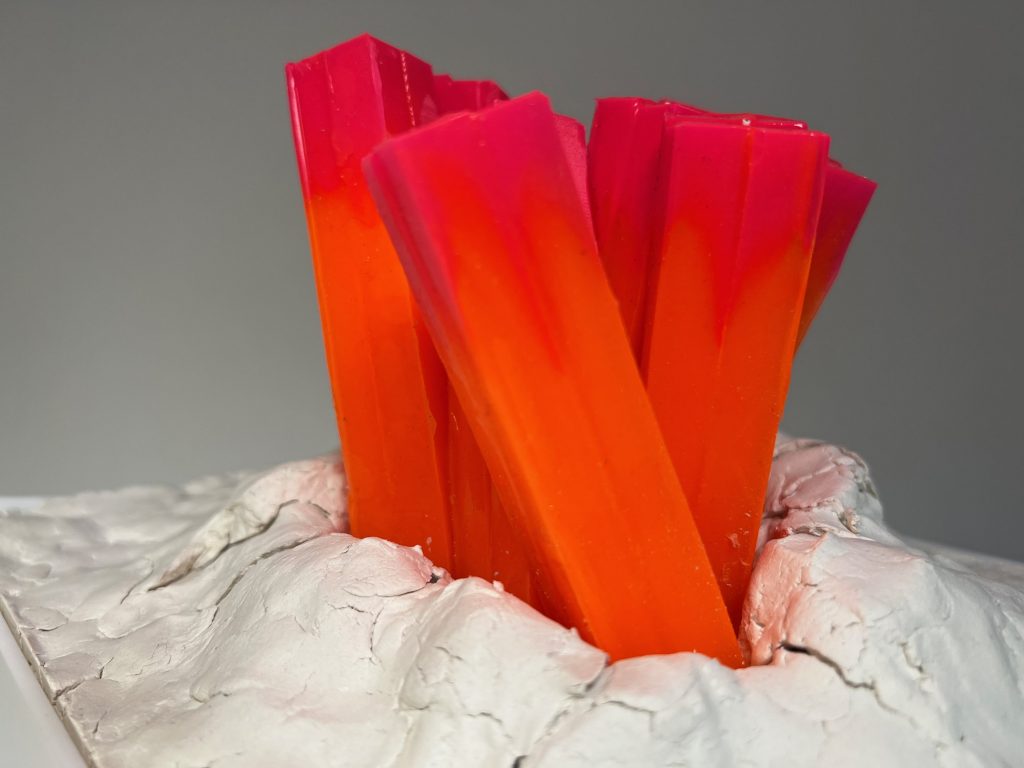
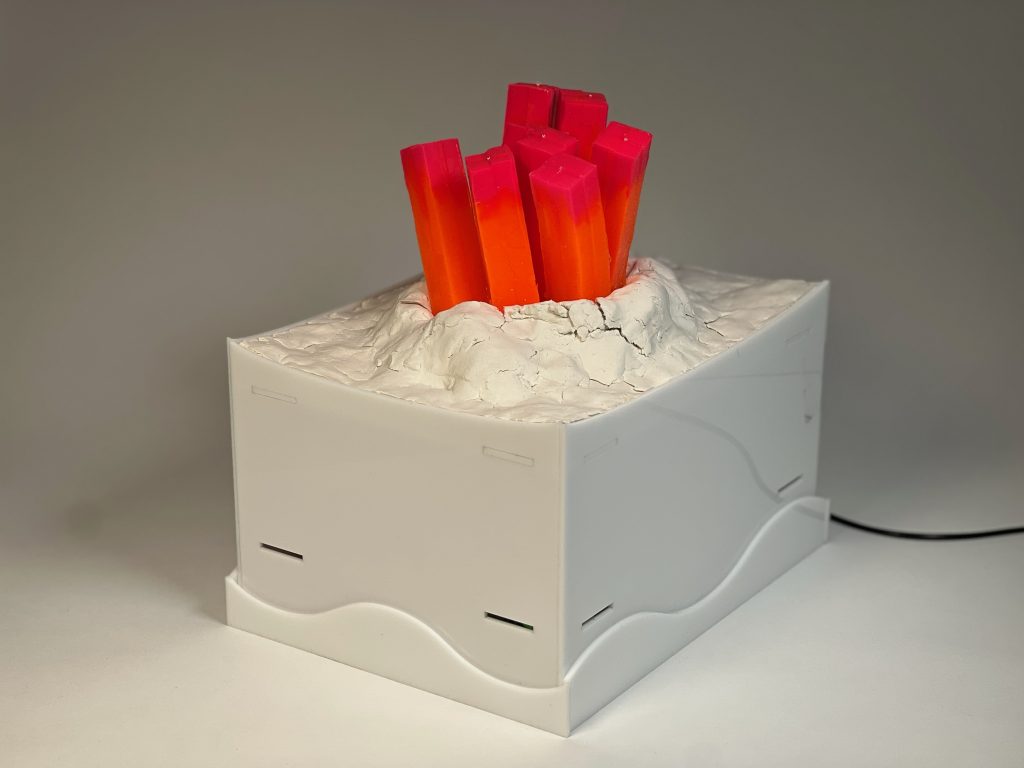
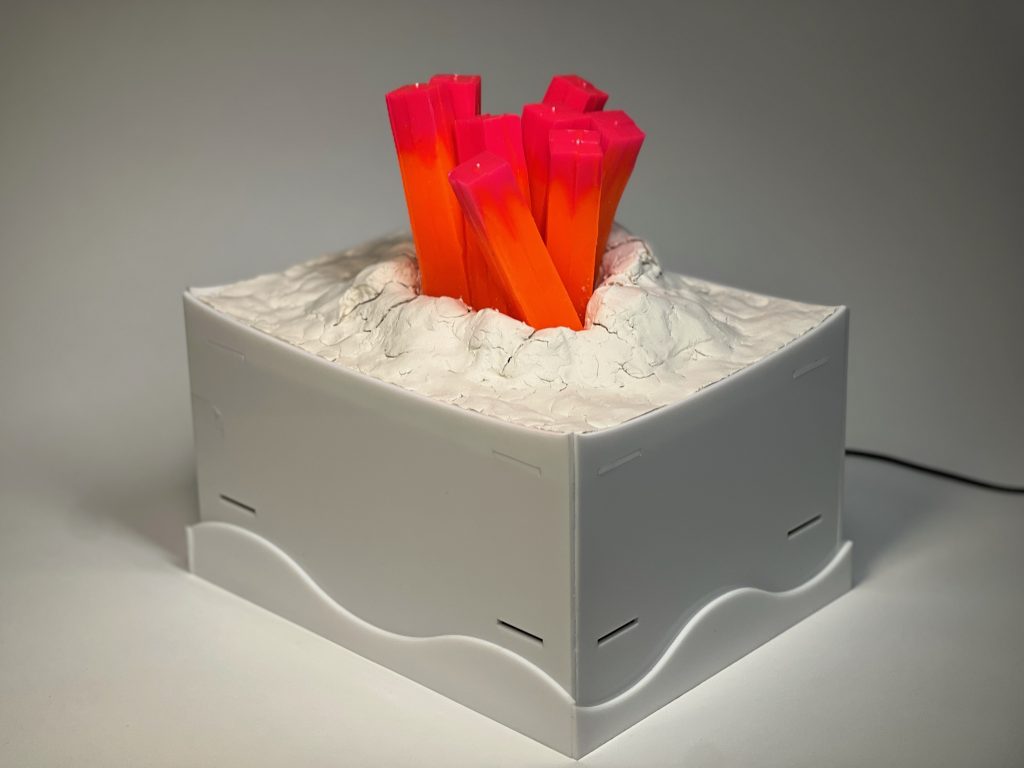
Contributions
Elise:
Silicon Fabricator: Mixed the silicon and poured it into the mold to make our tentacles. Responsible for the silicon color gradient idea.
Circuit Board Engineer: Wired the Raspberry PI, MOSFETs, capacitor, pumps, etc.
Box Laser Cutter: Designed and laser cut the box. Filled the top with paper clay.
Leah:
Movement Choreographer: Designed the intended timing of each pump to produce movement in each tentacle, creating 6 different “dances” for the anemone to perform.
Programmer: Wrote the code that turns the pumps on and off and reads the capacitor input.
Pump Mechanic: Poked holes in each tentacle pipe to cause a controlled leak. Determined the number of holes after a series of tests. Connected and hooked up each tentacle to a specific pump.
Both:
Mold Designers: Worked together to design the mold. Figured out and decided on a two-chamber system early on in the project.
Assistants: Each assisted the other with their primary duties. Leah assisted Elise with fabricating tentacles and wiring the MOSFETs. Elise assisted Leah with debugging and hooking up pumps.