Thumb prosthetic
Overview
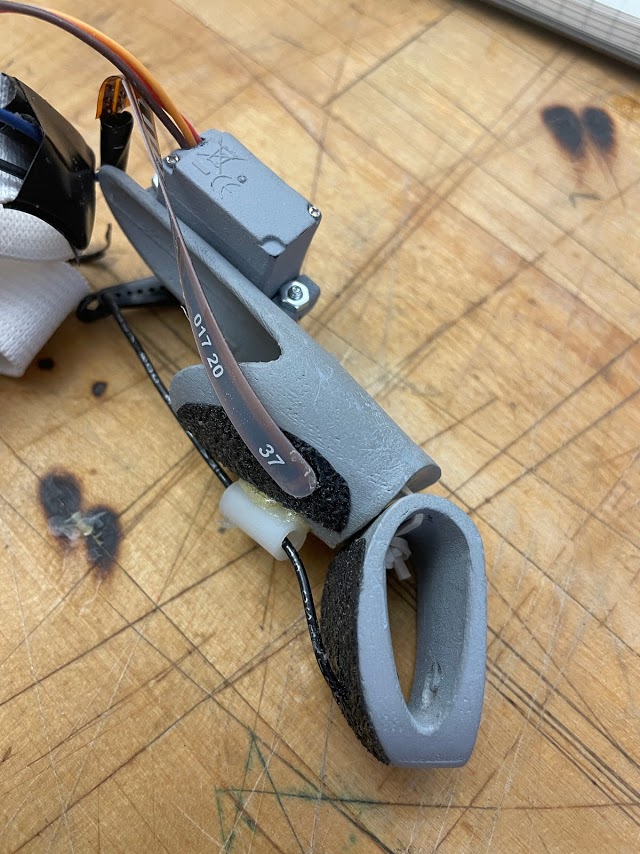
Final prosthetic
A prosthetic device for congenital trigger thumb that mechanically remaps the fused thumb joint further up the digit, using a flex sensor to sense compression and a servo to modulate the upper thumb.
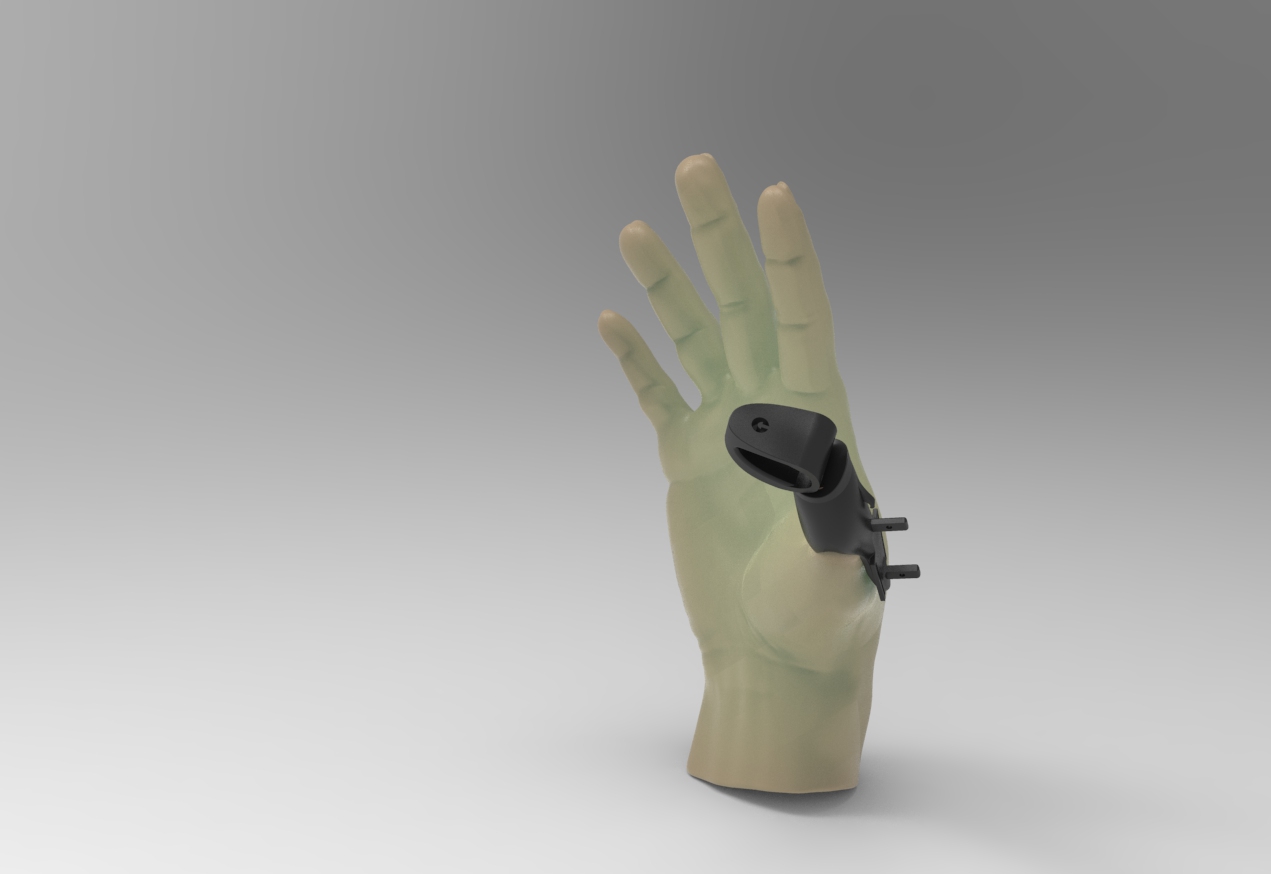
Rendering of printed components on hand model
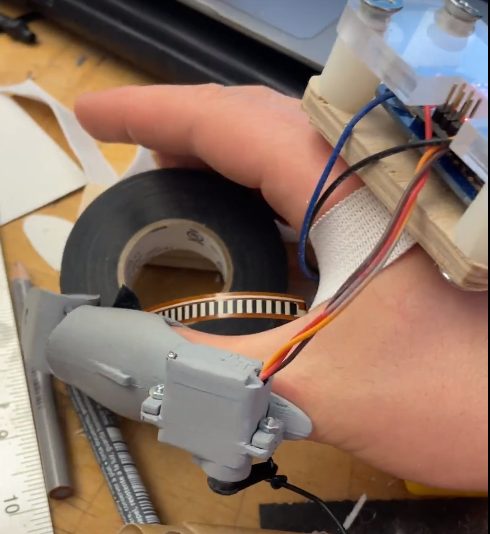
thumb in use grasping object
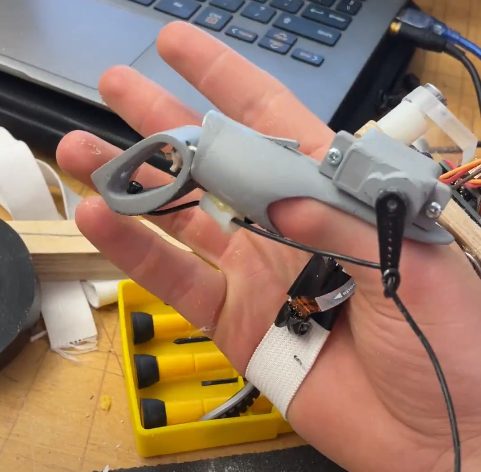
thumb in use demonstrating ease of pinch grip
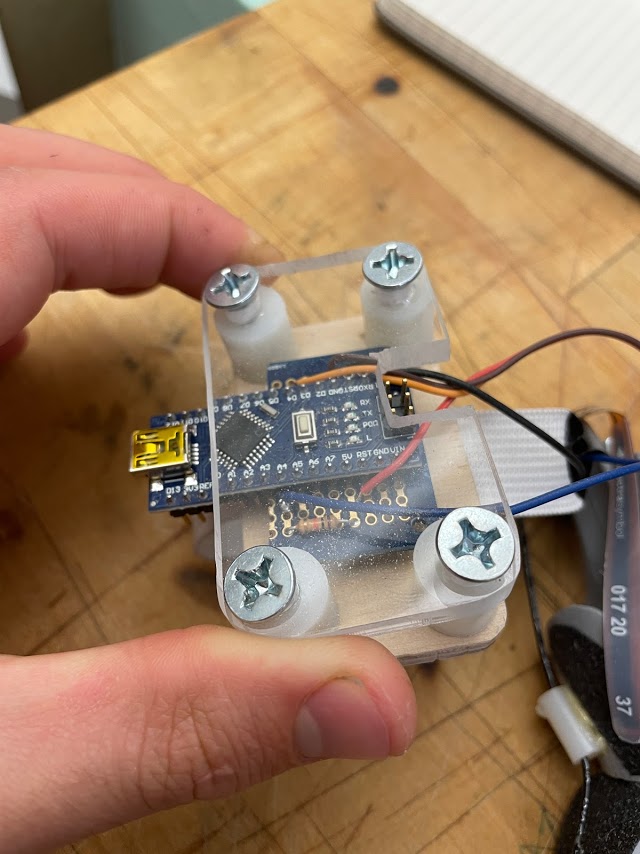
controller box
Process images and review
I began by determining the electronic hardware that I needed to use to make this work, and after doing some basic research into hand mechanics decided that a flex sensor would work well to detect joint tension and compression. I decided on the electronics early in the process and spent much of the time working mechanically to achieve an ergonomic and functional device.
To understand the necessary structures I worked initially in wood, springs, and rubber bands to create a rough works-like prototype.
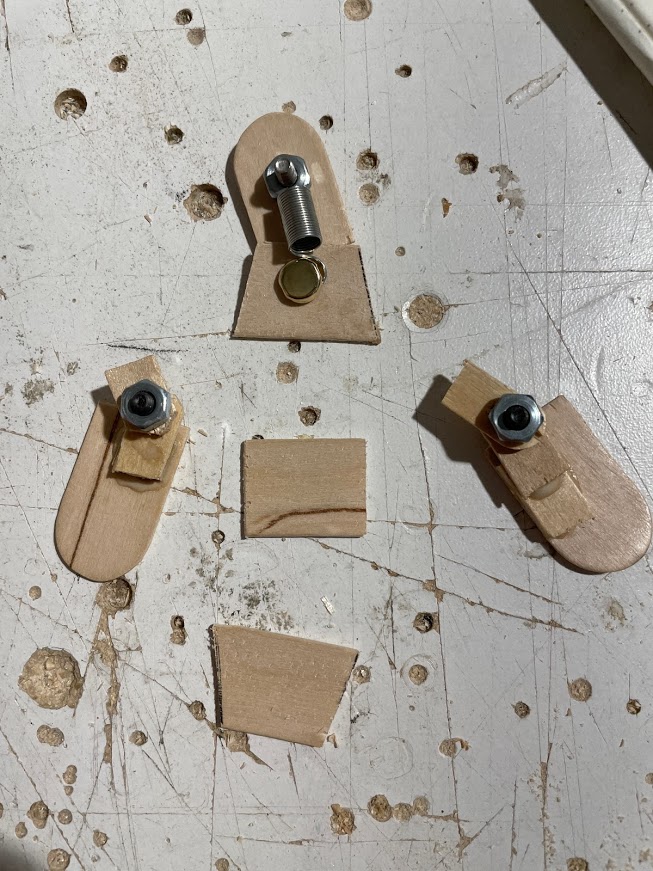
wood mechanical prototyping
After I had joined those pieces and made a non-electronic, physically manipulated prototype model, I decided to move to a purely electronic prototype to resolve the sensing and actuation.
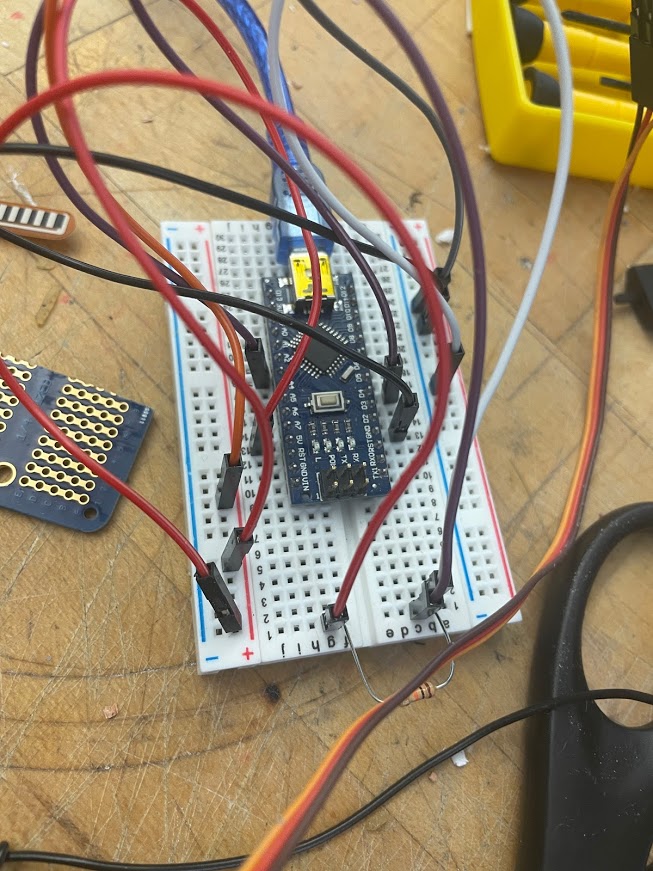
breadboard prototyping
I used a breadboard and the sensors to visualize and debug the electronics. Once I had them working, I moved to a soldered protoboard that I would use on the final device. I had no issues with the electronics and found that the direct mapping of the values was a very straightforward process. The adjustment came once the device was finally assembled and I had to modify the value ranges to reflect the physical constraints provided by the spatial range of motion.
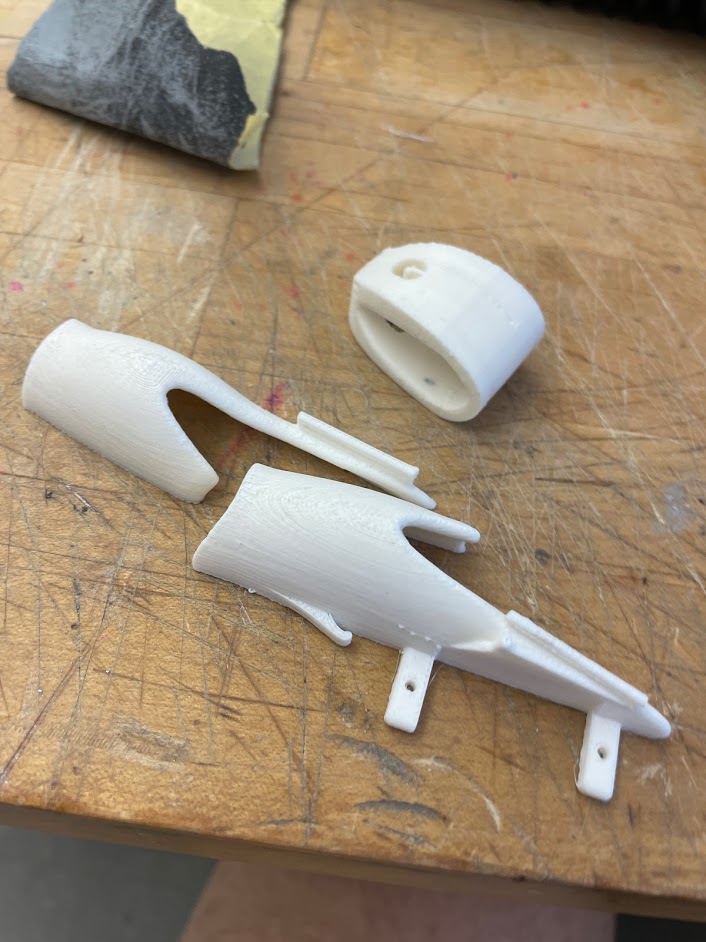
printed components
I printed a clamshell main structure and a separate digit. The main structure has mechanical interfacing for the servo motor to rest on the back. These parts were very successful and I was able to construct complex geometry in Solidworks that conformed well to my thumb contours.
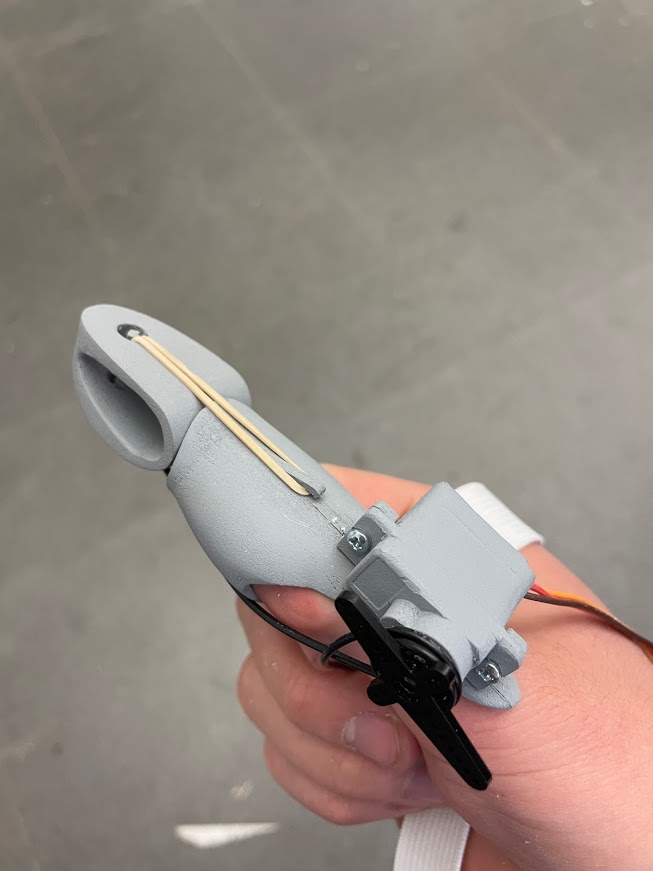
elastic prototyping for restorative force
After some of the parts were assembled and the prints had been processed, I did test fitting and began seeing what level of restorative force I needed from elastic. I ended up not needing the rubber band and used an elastic internal hinge.
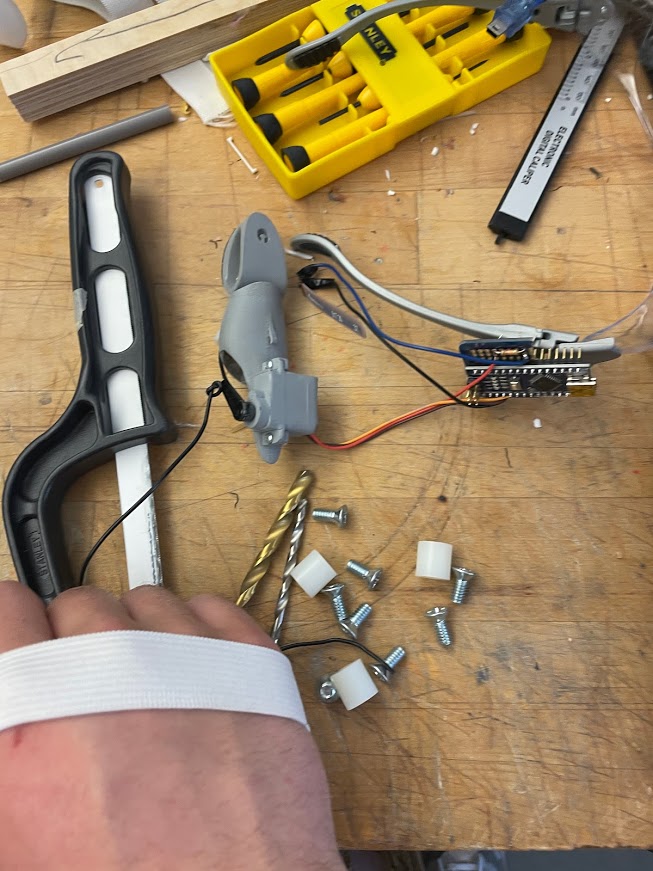
test fitting and finalizing measurements
To finish I soldered the final electronics and then attached the structures to an elastic band to hold it on my hand.
Discussion
I received a lot of positive feedback during the critique that supported my decisions and device. I think given the time frame and project constraints my device was very effective, although the brittleness of the flex sensor leads led to performance issues after user testing. I received feedback that “The attachment of an extra digit to the thumb would change the whole way a person uses their hand. A next step if the project continued might be researching ways to make that more intuitive whether it be by having a shorter extension or something else.” I totally agree with this feedback and I was sad that I couldn’t explore this more in this project. I tried to focus on the electromechanical and ergonomic aspects of the device but given more time and resources I would’ve absolutely considered physical behavior changes and the enhancement possibilities that this device affords. “Would a spring make the thumb stronger?”- Yes, but the force curve of springs leads to a lot more strain on the servo I was using so I couldn’t achieve the modulation fidelity that I desired. I had prototyped with springs and different types of rubber bands and found my restorative solution to be effective. “How would this react when actually grabbing something? Is the grip strong enough?”-I actually tried picking up some objects and had difficulty, I think it has to do with the nerve pressure that is lost and the ‘settling’ effect of flesh when grabbing something. I also think this device requires a long break-in period to get a strong mind-body connection that would allow it to be used effortlessly. I’m very happy with how the project came out. I obviously wish that things could’ve been made more miniature, but this project was not focused on those constraints. I was really surprised with how fluid of motion that I was able to achieve and how natural the movement seemed. I learned a lot about human movement and designing for human contact. I think that directly translating the compression of the human form to the movement of a motor allowed for movement curves to be accurate to human movements, so this sort of natural actuation is really important instead of more artificial methods. I think moving forward I would change the form to be a little more simpler in terms of geometry and hopefully have smaller, more reliable, and stronger electronic components but those are all in an ideal world. I don’t think I would significantly change my design process or my method because I found it to be successful. I may build another version of this in the future, but after significant time to reflect and maybe have different insights into actuation and electronic integration.
Technical information
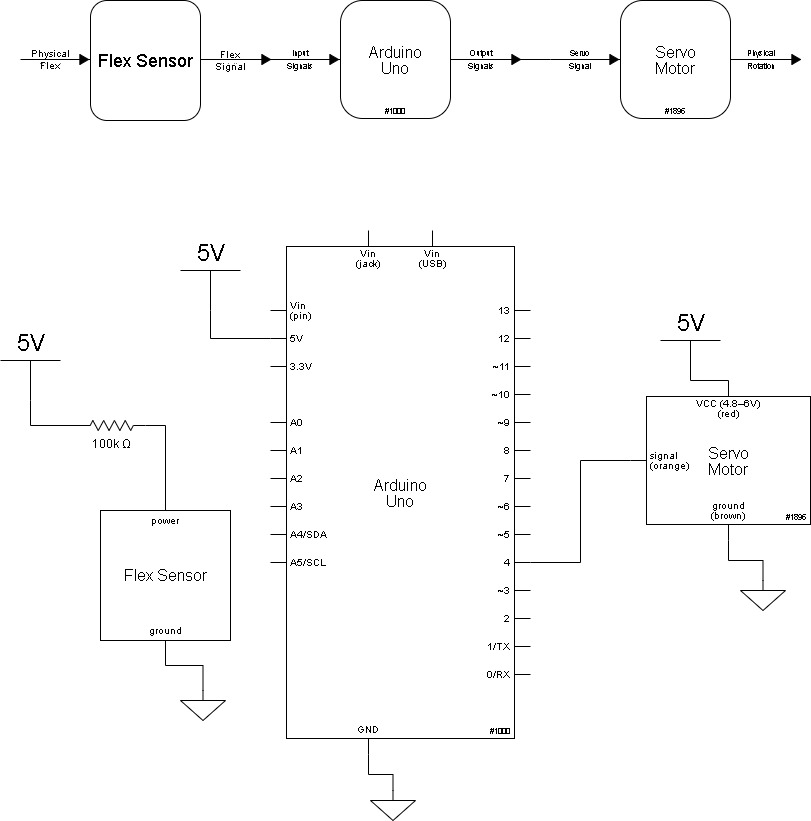
functional block diagram and schematic drawing
/*Project 2: An assistive device for someone you know very well * Prosthetic Trigger finger thumb * * This code uses a flex sensor mounted to a users inner hand to modulate a servo to bend a prosthetic thumb. * The more the flex sensor is deformed, the further the servo (and thumb) travel. * * Thank you to Last Minute Engineers for their guide on using flex sensors, which was referenced for this project. * https://lastminuteengineers.com/flex-sensor-arduino-tutorial/ * */ const int flexPin = A4; //read flex sensor analog input #include <Servo.h> Servo thumbMotor; // servo actuator const int servoPin = 4; // pin the servo is connected to int value; //analog value void setup(){ thumbMotor.attach(servoPin); // set up the servo on that data pin } void loop(){ value = analogRead(flexPin);//read and store flex value value = map(value, 800, 900, 0, 180); //map flex value to servo modulation thumbMotor.write(value); //activate servo }