Mary Tsai and Matt Prindible
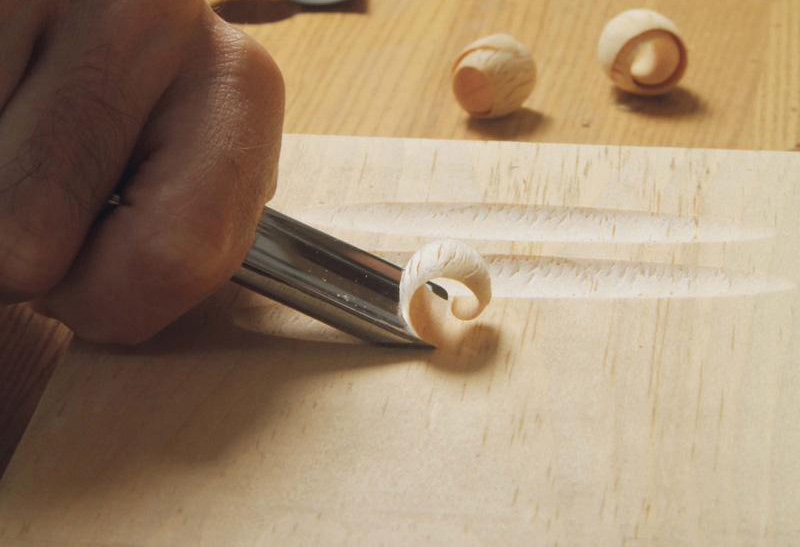
Introduction:
For this exercise, we chose to study a simple hand gouge and a basswood blank. The specific motion we are interested in is the gouge digging in and carving up a sliver of the wood. Because of the linear shape of the hand gouge, we had to construct a platform on which the retroreflective markers could be attached. We also added these markers to the wood blank.
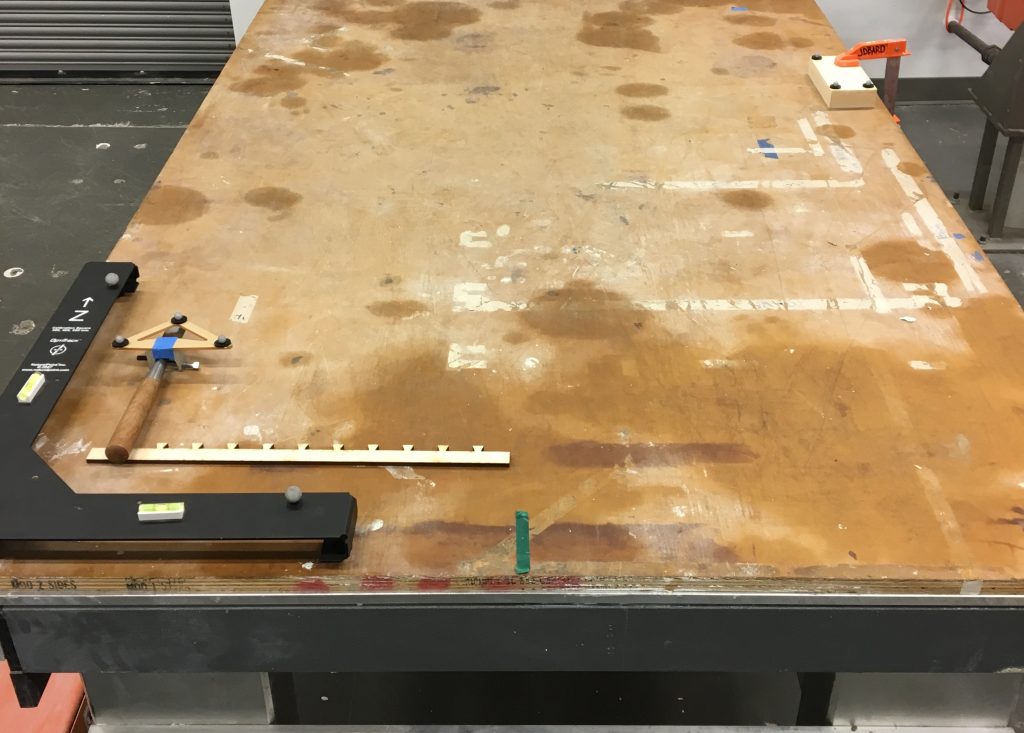
Process:
Because of the small workable surface area of the wood block, the hand gouge motions were limited and fairly constricted to movement in one direction. Typically, a wood carver would be able to approach the block from multiple directions in order to make certain types of carving. The range of motion was further constrained keeping the markers in the camera’s field of view.
We then created two rigid bodies (the gouge and the block) in Motive and captured a base pose for orientation and three takes of ten seconds of use.
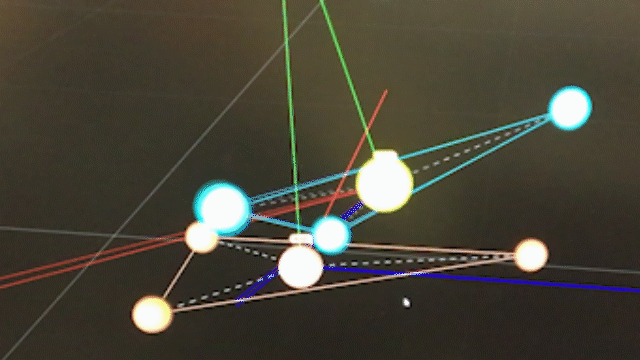
We imported the base pose capture data into Grasshopper and baked its points into Rhino. We created models of the tool and block independently and then used the base planes from the motion capture data to orient and position the models. Since the wood block is static, it also served as our ground plane.
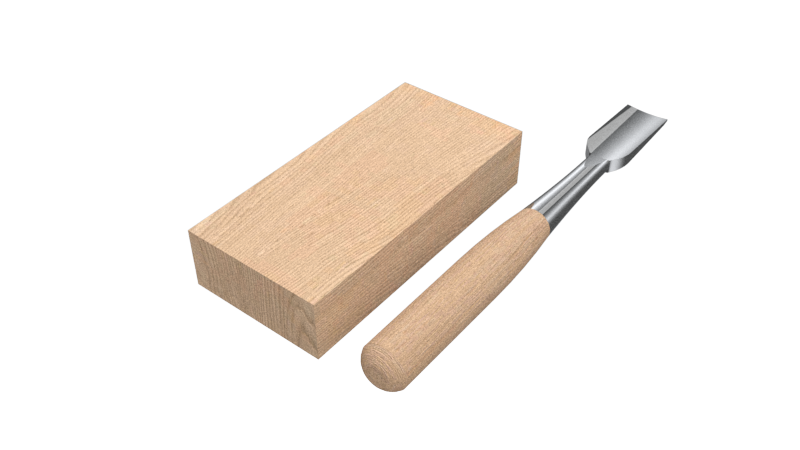
We used these models in Rhino to create Grasshopper geometries for each rigid body (Geo). We then fed the motion capture data into Grasshopper and used the orient node to manipulate the position of our Rhino models.
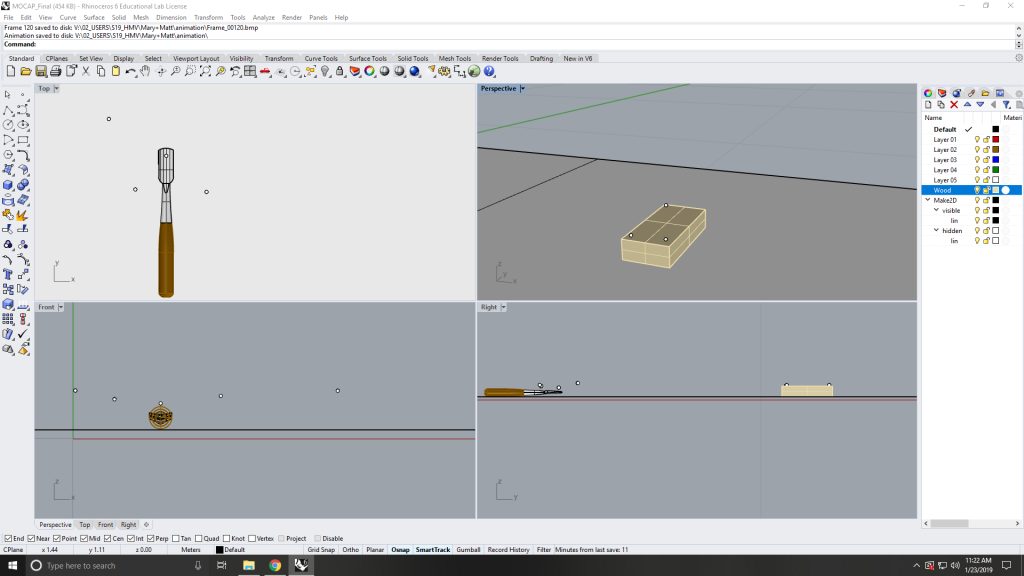
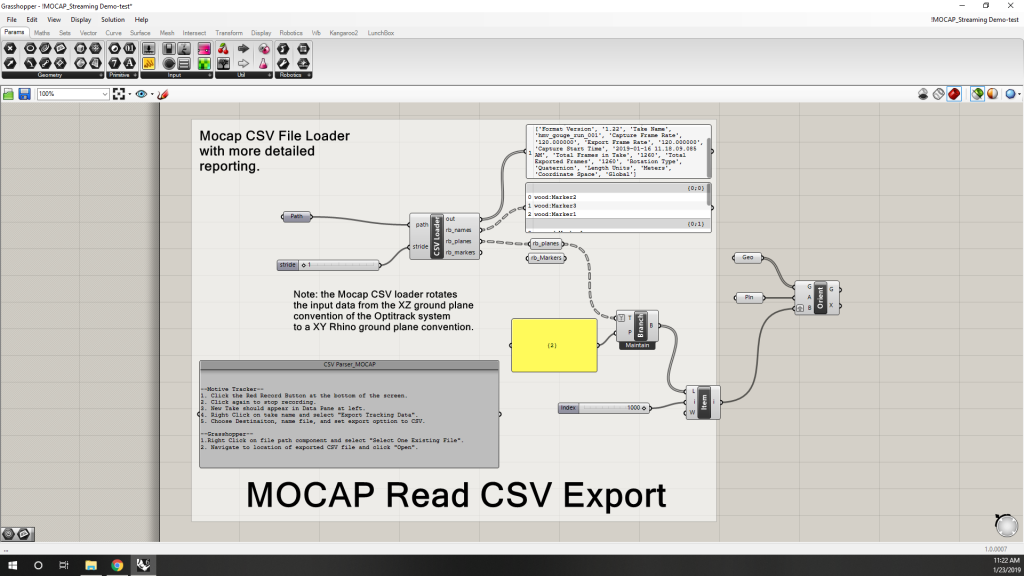
We added a slider to isolate one interesting second of motion: where the tool interacts with the wood and captured the animation.
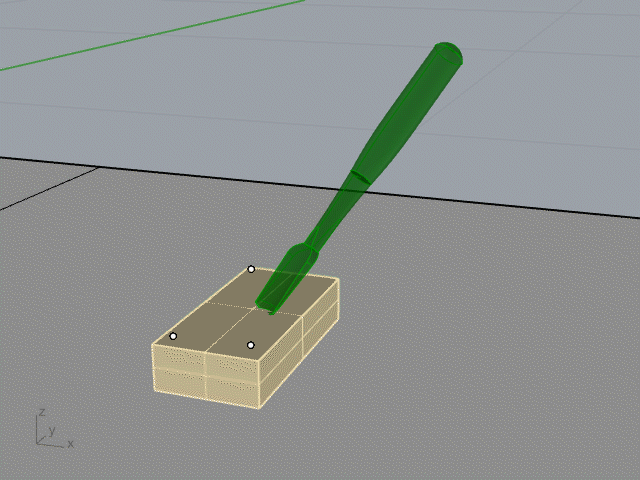
Analysis:
Based on our motion study and data, we would be able to figure out the velocity and force at which the gouge hits the block (visibly, the point at which the gouge stops moving). This appear obvious, but depending on the level of skill of the craftsperson (or wood type/grain direction) the gouge would either come to a hard stop or continuously move through the wood. In our capture we see the former—the tool coming to a complete stop and building up enough force to overcome the material. Some of this is because of the limited range of motion afforded to the craftsperson during motion capture. Some of the tool rotation observed in our study is a result of the resistance that the tool encountered.
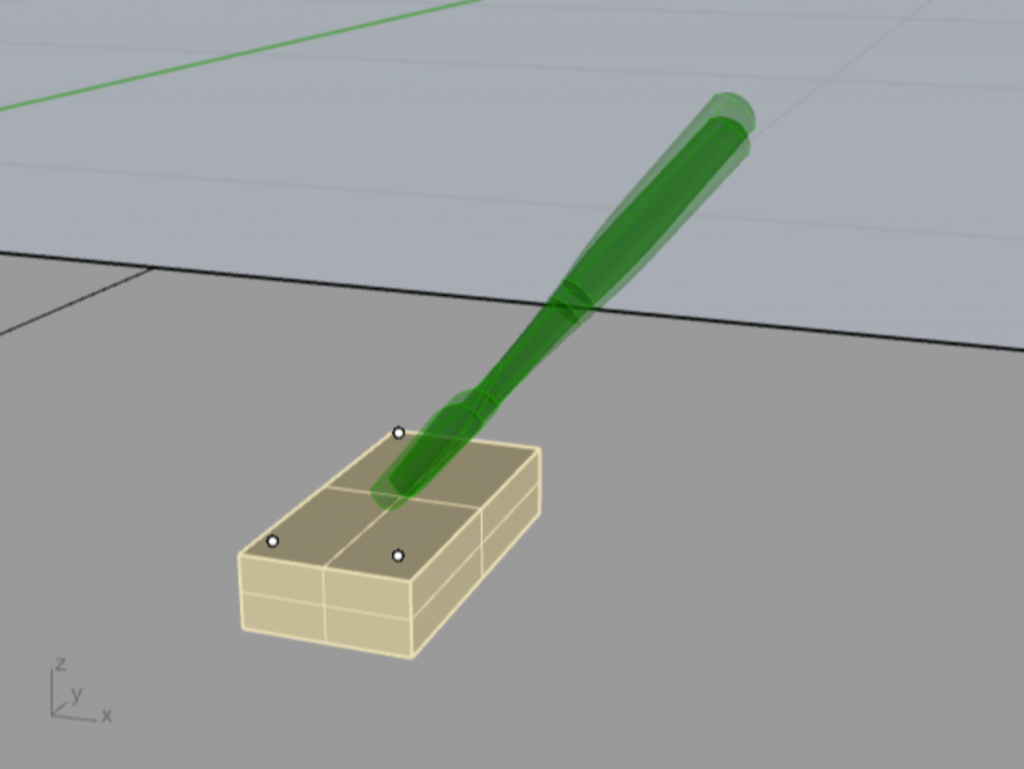