Project Objectives
VoidCrawler – Jason
The main objective of this project was to create an alien creature that embodied the theme of “Void” through peculiar movement and anatomy. I wanted to offer people an experience of encountering a foreign, alien organism that blurred the lines between lifelike and lifeless. The project utilized silicone to emulate fleshy appendages and motion, while making use of rigid material to create a protective shell.
Rnav – Inbar
My objective was to recreate Whitesides’ soft robot successfully, in order to then create another version of this robot that is scaled up to the dimensions of my pet rabbit. The purpose of the scaled-up version of the robot is to be feathered in one scene of my documentary project, which premise is centered around my hopeless attempts to restore the lost libido of a castrated pet. The design of my soft robot has only one variation from the original one – another round chamber that will be filled with a smell-induing liquid, for the purpose of drawing my rabbit to it. Thus, my objective was not to change the original design of the soft robot, but rather to utilize its aesthetics and the connotations of its materials to then showcase it in the context of my video project. The current title of my project is “Rnav”, which is a misuse of English letters that resolve in what sounds like the Hebrew word “Rabbit”.
Creative Design Opportunities
Jason
The use of soft silicone material allowed me to design and fabricate appendages that mimicked the texture of slimy and shiny creatures. Additionally, the silicone’s behavior when actuated created a slow and steady motion that imitated how animals get up from rest.
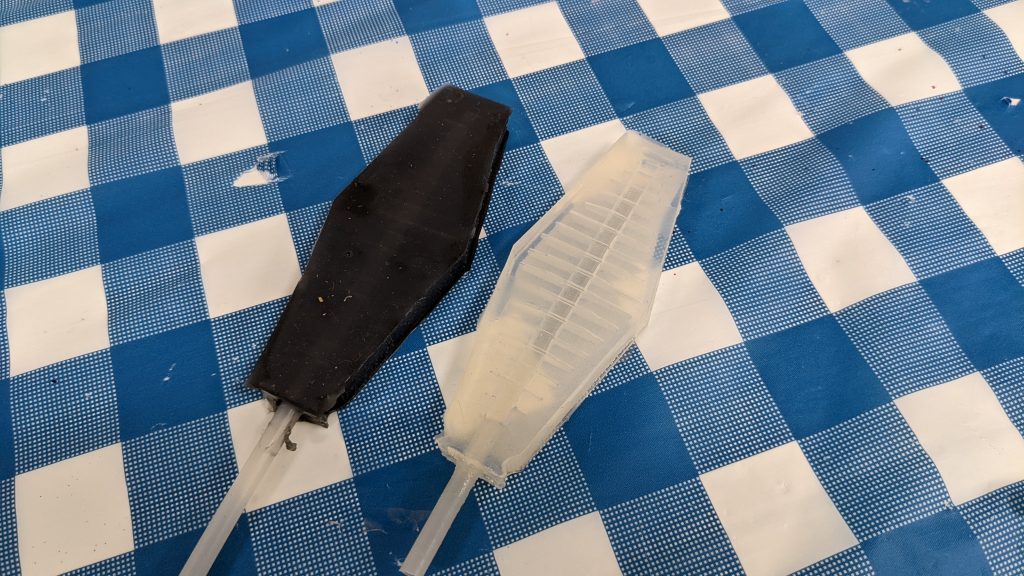
The versatility of the silicon also allowed modifications to be made during fabrication. Although not an intentional design choice, the use of the fabric within the clear silicone appendages created an interesting visual effect that resembled that of jellyfish. Furthermore, the usage of dyes within the silicone parts allowed for more creative freedom by creating really dark parts that match the theme of Void.
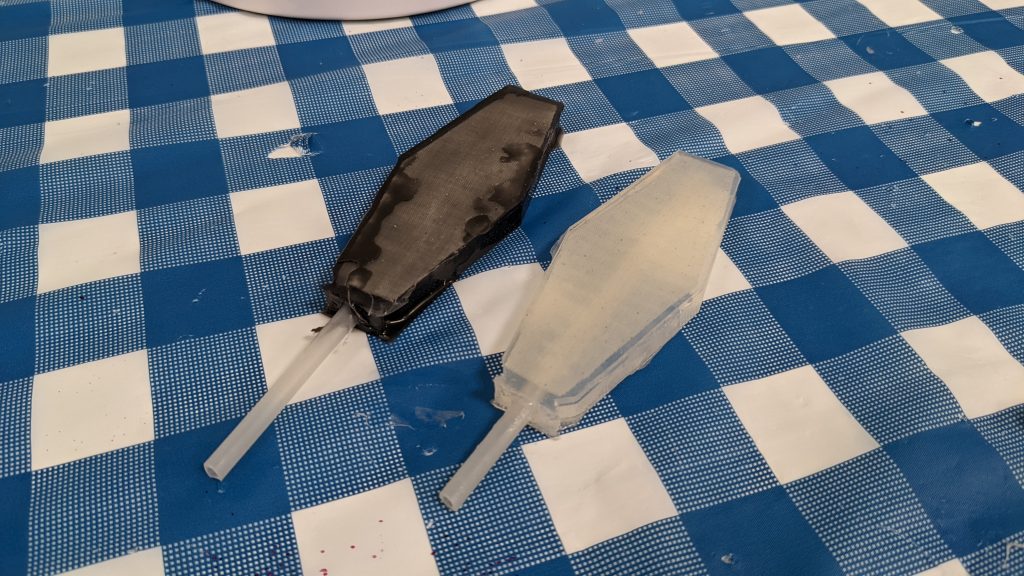
Beyond the silicone molds, the use of rigid parts through 3D printing incorporated some mechanics within the design. I was able to design a central unit where multiple appendages could be attached to create an n-legged creature. Similarly, I was able to use color with this material as well, specifically black, to produce a shiny and hard product that perfectly resembled a hard outer shell of an organism.
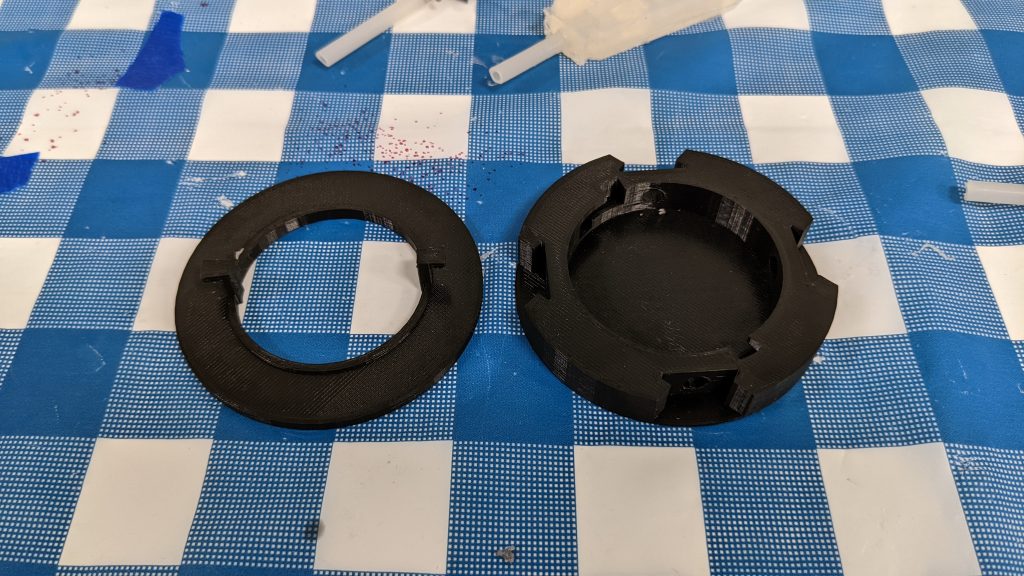
Inbar
The design process of Whitesides’ soft robot required me to learn several new skills: silicone rubber casting and bonding, parametric design using SolidWorks, and 3D printing. This is the first time that I’ve experimented with either of these skills, and the intense engagement with them during the course has led me to acquire enough knowledge so that I can continue to use them in my future projects. I find this very gratifying since silicone rubber and mold making is a scope in sculpture that I have always wanted to experiment with but never did because I felt I lacked the needed abilities and/or knowledge.
Silicone is an inspiring material that is fascinating to work with because of its skin-like qualities, and the different signifiers it can evoke in different contexts: body implants, props, sex toys, etc. However, the design and manufacturing process with silicone needs to be very precise and well-planned, especially when trying to mimic an existing robot from a scientific paper that does not include instructions or exact dimensions of each part. Such a slow and precise work process is very different from the creative processes to which I am accustomed in my artistic practice, and I believe this is the reason I had to go through a few failed fabrication attempts until I became accustomed to the orderly work process.
Outcomes
Jason
The final outcomes of the project were a fully assembled Void Crawler, albeit with only two functioning appendages. The sequence developed for the Void Crawler consisted of a basic rising up motion followed by actuation for just one appendage at a time.
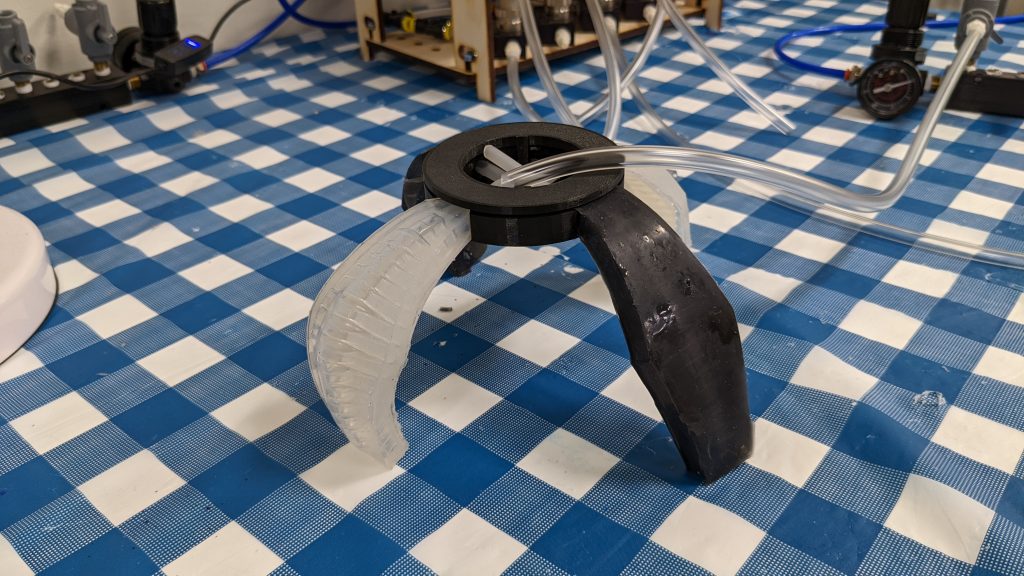
The greatest success of this project was the design of the soft silicone appendages and the use of fabric during fabrication. The initial design choice of making the appendage a stretched-out hexagon was arbitrary but later showed interesting behavior as the chamber design was modified. The varying length of the thin chambers from end to end proved to create a desired “joint-like” actuation. Although this was assumed to be a result of the chamber pattern, there was no formal test to validate this claim. Upon additional research, a fabric embedding technique was found. It was implemented and provided a more consistent and circular curvature. Although some papers mentioned specific materials, regular and thin fabric performed really well.
One of the greatest failures within the project was bonding. Although in the end I managed to have two fully operational appendages, the bonding process proved to be too inconsistent to guarantee full bonding every time. There were several attempts to fix this issue. The latest solution with mixed results consisted of changing the shape of the tube port to square to allow slicing of a thin base layer. A full thin layer would be spread over the intricate top mold and then bonded with the thin bottom layer.
The current state of the project is very much a prototype. There are many ways this project can be improved upon. One of the key areas for improvement would be with the bonding. The research papers used in this project mentioned the use of “bonding surfaces” to ensure proper bonding. The current molds could be modified to include a new bond design that would incorporate this idea. Additionally, the lengths of each chamber and distance can be modified to see if there are more interesting movements that can come from the hexagonal shape. An idea mentioned early on in this project was the incorporation of an additional chamber within the center unit to initiate a vital organ, such as a brain. This idea can be further developed in the next iteration of this project.
Inbar
During the design process, Jason encountered a post online that documented a similar studential attempt to recreate Whitesides’ soft robot. During their fabrication process, these students decided to slightly change the robot’s design in order to allow for easier fabrication and bonding (they expanded the width of the inner chambers and also expanded the distance between the chambers). After several design attempts, I’ve decided to follow the same path and tried to recreate their design rather than the original Whitesides one.
My final soft robot bonded successfully except for one small slit in the bonding area, which I detached through a bubble test and resolved using epoxy glue. It was also pretty easy to understand and recreate the choreography that is needed to create crawling locomotion using the movement code – I followed the rhythm from a documentation video the previously mentioned students uploaded to that post. All five parts of my robot inflated successfully and the robot seemed to crawl forward through two consecutive loops of movement – until I pressed one of the legs and it exploded (as can be seen in my documentation video). Two more legs ended up exploding later in the showcase event, which perhaps means we used too-high air pressure. However, I do perceive this as a positive result, since the documentation video indicates that during the two movement loops that the robot completed before the first leg exploded, it did manage to move forward.
In the next few months, I plan to attempt to create a scaled-up version of this robot, and then use it while filming the scene I’m planning for my documentary project. I’m planning to scale up the same final design and stick to the same silicone casting protocol but will have to create the molds differently, due to the size limit of 3D printers. As a first step, I will try to fabricate one large-scale mold using wood and laser cutting. Another future step would be to identify and achieve the correct liquid to use within the added camber I added to the design, which might need to be the urine of a different rabbit or other substance that contains the appropriate pheromones.
Documentation video
Jason
Inbar
Citations
Jason
The project was almost entirely original, mainly drawing on ideas regarding fabrication and application found within many academic papers on the topic of soft robotics. One influential paper that helped in understanding the design and fabrication process, however, was the Whitesides paper on an untethered soft robot design. This paper provided more context for fabrication problems and solutions. Additionally, the paper on this starfish robot provided the inspiration for a central unit to attach all appendages.
Tolley, Michael T., Robert F. Shepherd, Bobak Mosadegh, Kevin C. Galloway, Michael Wehner, Michael Karpelson, Robert J. Wood, and George M. Whitesides. “A Resilient, Untethered Soft Robot.” Soft Robotics 1, no. 3 (September 2014): 213–23. https://doi.org/10.1089/soro.2014.0008.
Zou, JiaKang, MengKe Yang, and GuoQing Jin. “A Five-Way Directional Soft Valve with a Case Study: A Starfish like Soft Robot.” In 2020 5th International Conference on Automation, Control and Robotics Engineering (CACRE), 130–34, 2020. https://doi.org/10.1109/CACRE50138.2020.9230177.
Inbar
Hao, Bohan, “Soft-robot Design and Fabrication,” cargo collective, May 2013, https://cargocollective.com/bohanh/Soft-robot-Design-and-Fabrication.
Shepherd, Robert F., et al. “Multigait soft robot.” Proceedings of the national academy of sciences 108.51, 2011, https://doi.org/10.1073/pnas.1116564108
Technical Documentation
Group Member Contributions
Jason:
- Updating code to work with the project specifications
- Testing thick chamber designs
- Bonding/Slicing technique
Inbar:
- Locomotion
- Testing thin chamber design