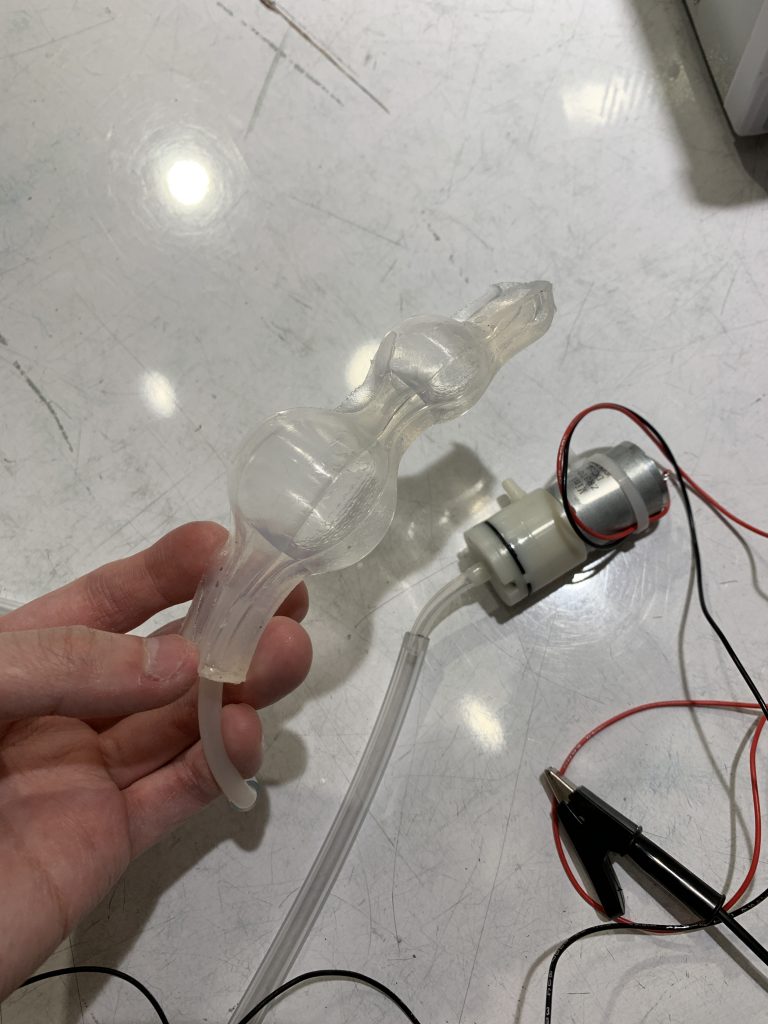
Unfortunately, this first version of the model did not work well. You can see that the silicone bends at an angle of only 10-15 degrees. This is far below our expectations. Another problem is the “balloon”.
Also this week we tried to cast the wire in silicone and tried to connect to a power source to watch the energy transfer. Unfortunately, we could feel a lot of temperature while the wire inside of the silicone barely straightened.
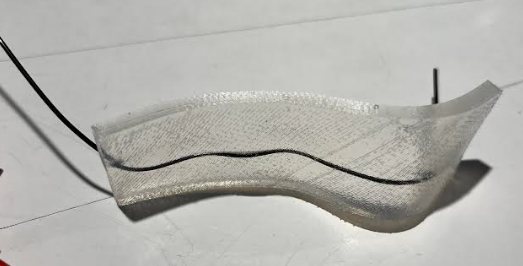
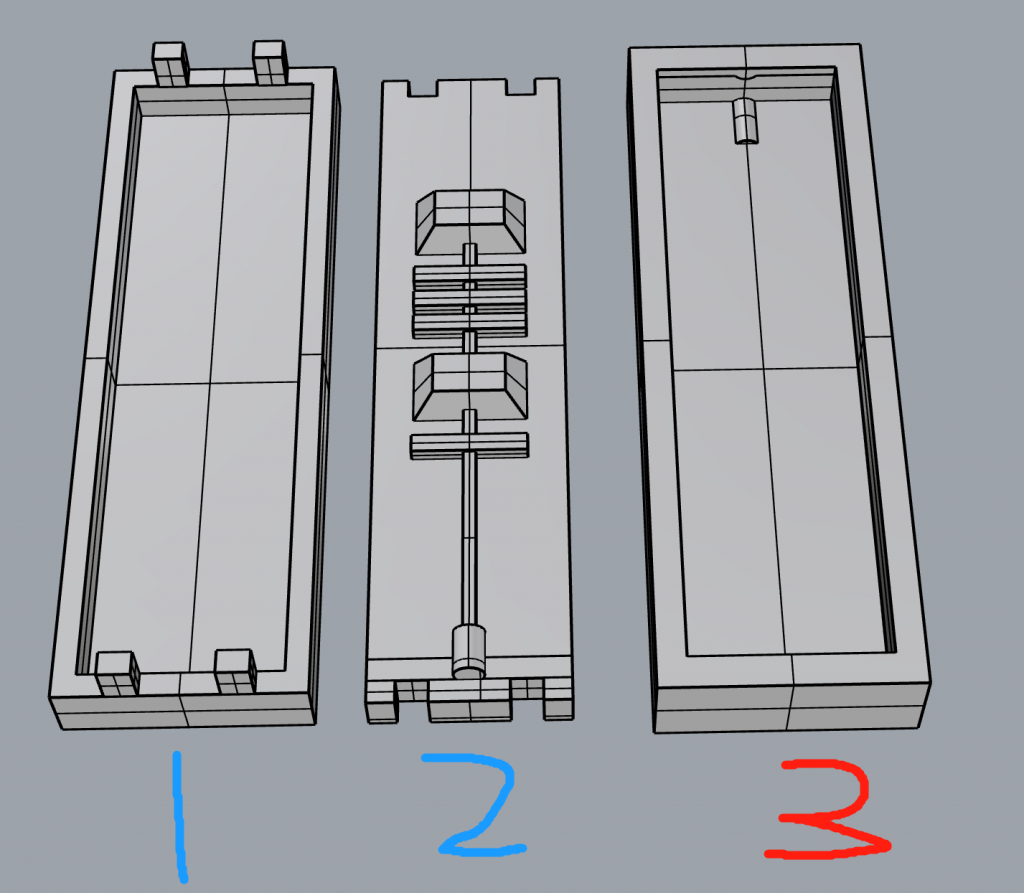
(Above is a two-part model. The blue numbers “1” and “2” in the picture can form the upper part of our model. The red number “3” is a simple 5-6mm flat surface to help us improve the bottom strength.)
We first tried to fix the bending angle problem. We think there are two reasons for not being able to reach the angle. First, the structure and location of the air region. Second, the force of the air is not concentrated in one area.
We tried to adjust the structure and position of the air area to make the wall more inclined. We also added some small channels to try to see if the silicone would help increase the angle after it was inflated.
For the second problem, we agreed that the main reason was that the bottom silicone was not thick enough. In the first version it only had a bottom of about 2.5mm. In the second version we increased the bottom to 5mm to see if it made a big difference.
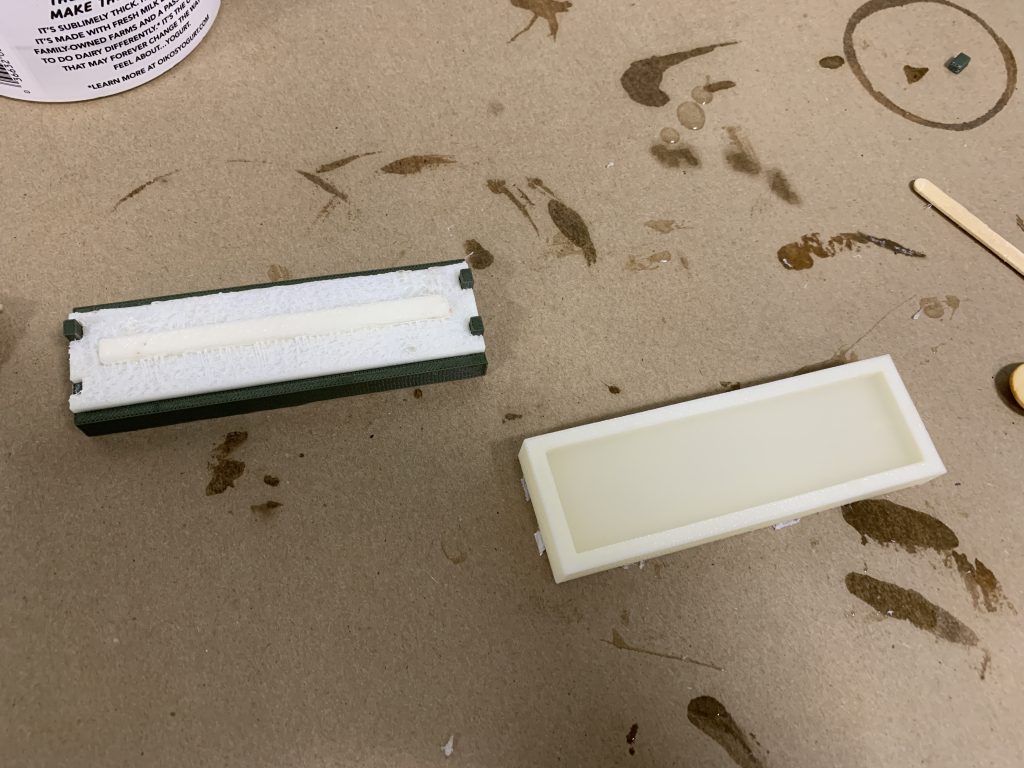
After casting the new three-piece design in silicone, we realized that there were some measurement errors that we believe are the result of transferring the STL between CAD programs. Nevertheless, we bonded the pieces together as best as possible, and hope to gain something from this iteration.
We will be re-modeling this design, as well as fleshing out a more triangular design we discussed with Garth last week (rough sketches below):
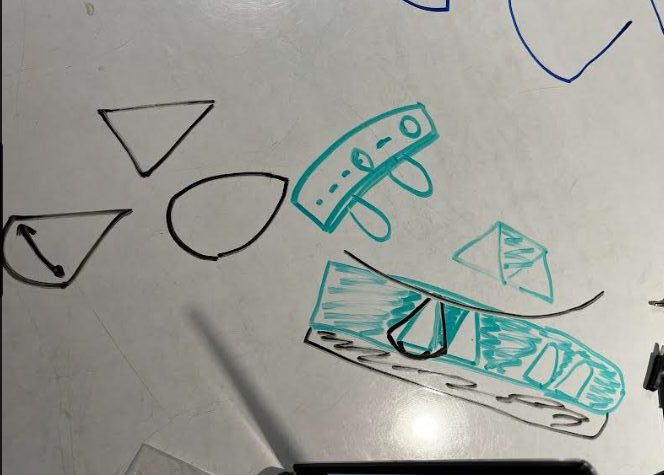
Another interesting idea is to add some fibers to the bottom layer to further increase the strength. We are looking for materials that still do. We have not implemented this concept in any way yet, so stay tuned!