This past week we have been established two different work flows: Elena has been working on the connection of the silicone piece to the Legos/tubes, while Sebastian has been continuing our work on the silicone parts.
The Lego/tube/silicone connector progress:
We have modeled three parts (to accommodate for the FDM printers we will be using in the early iterations) and sent the parts to print on Sebastian’s printer. The printer couldn’t handle the thin tubes well, so we will send it to the Stratasys in the hopes of getting better prints. We see this part being SLA printed for the more final parts.
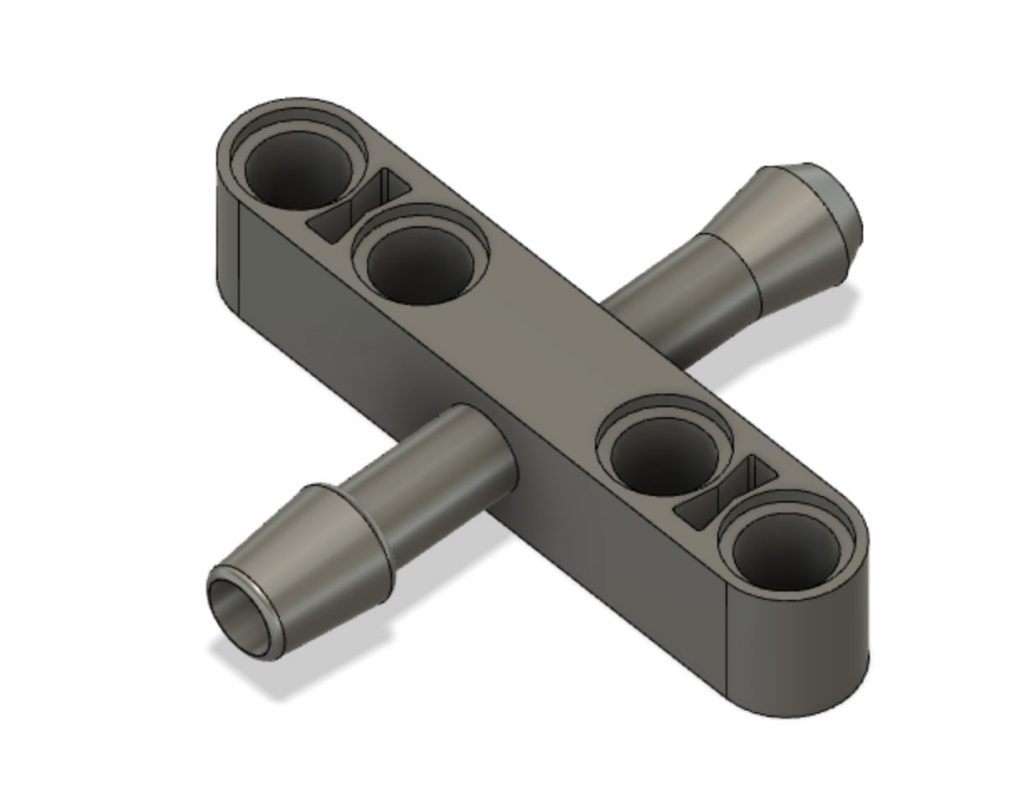
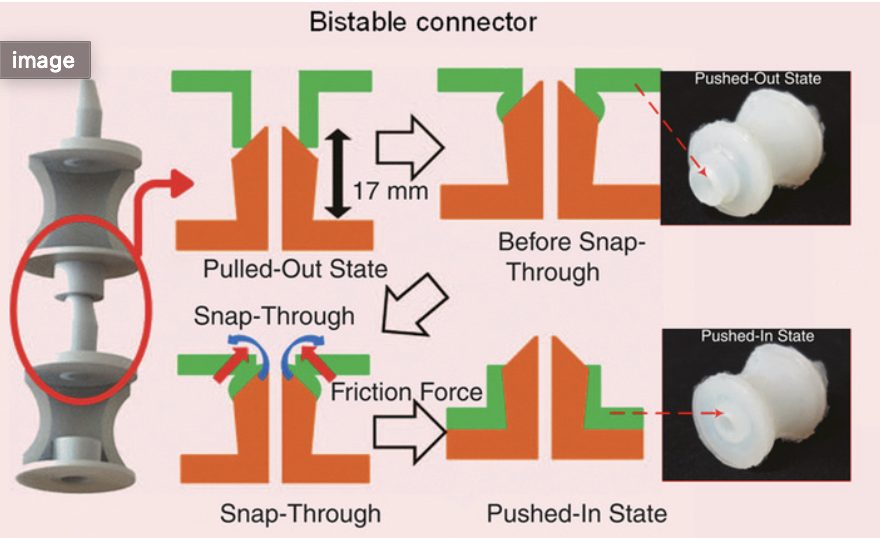
The Silicone/Air Chamber Part Progress
We tried to cast a silicone mold of one of the air chamber concepts from our last post. The silicone cast successfully, and we were able to avoid the leaking that we encountered last time, but we encountered a new problem: an inability to pull the central bit out of the mold.
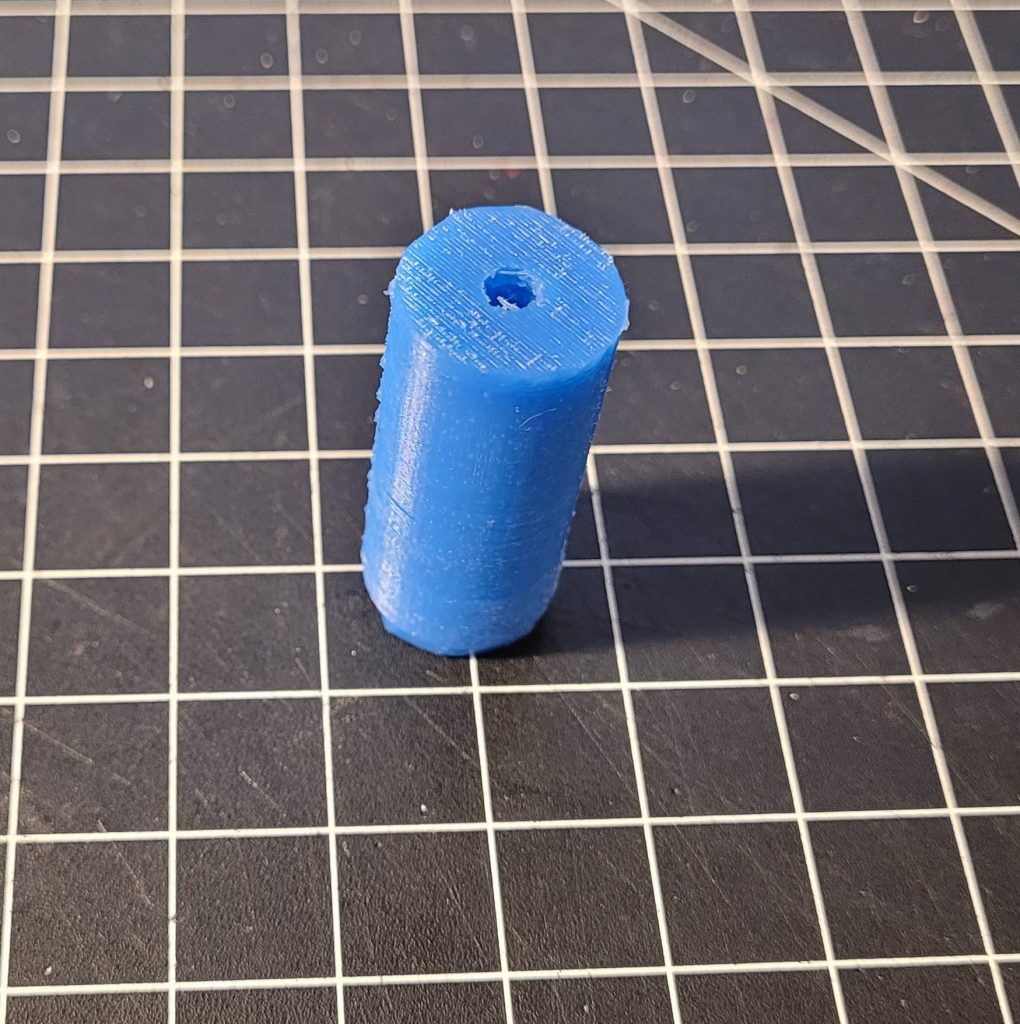
In order to address this issue and some issues unnecessary excess material, we updated the design of our molds.
We attempted to make a negative of the center piece and cast it in a soy wax that could be melted out after the silicone cured. This initial attempt at casting wax failed, as the wax seemed to adhere better to the mold than to itself, breaking in half when we tried to split the mold in half.
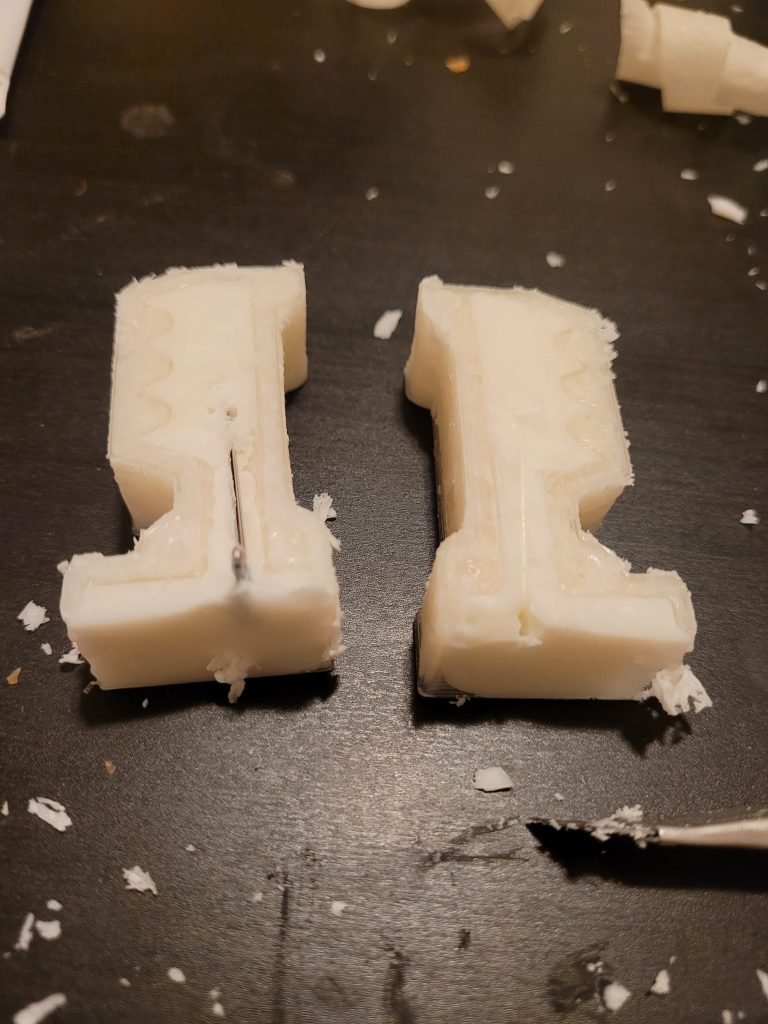
We are going to continue trying to work with the wax. A couple things we are intending to try: adding draft angles where they do not currently exist, checking for and patching all holes in the 3D print (some wax leaked into the inside of the 3d print), breaking the mold into more parts to decrease the contact surface area of any given mold piece to the wax. Another potential avenue to improve this casting might be to switch from soy wax to a harder beeswax or even a paraffin wax. The increased rigidity might make it easier to separate from the mold in one piece.