We rewired the 3×3 sensor grid we had last week and the signals become much cleaner, so I think the noisy signal from last week is caused by error in wirings.
We were able to figure out a somewhat efficient way to create the sensor grid and fabricated a 6×6 sensor grid(which still took 2h+) and got it connected/working with both the arduino code and processing code.
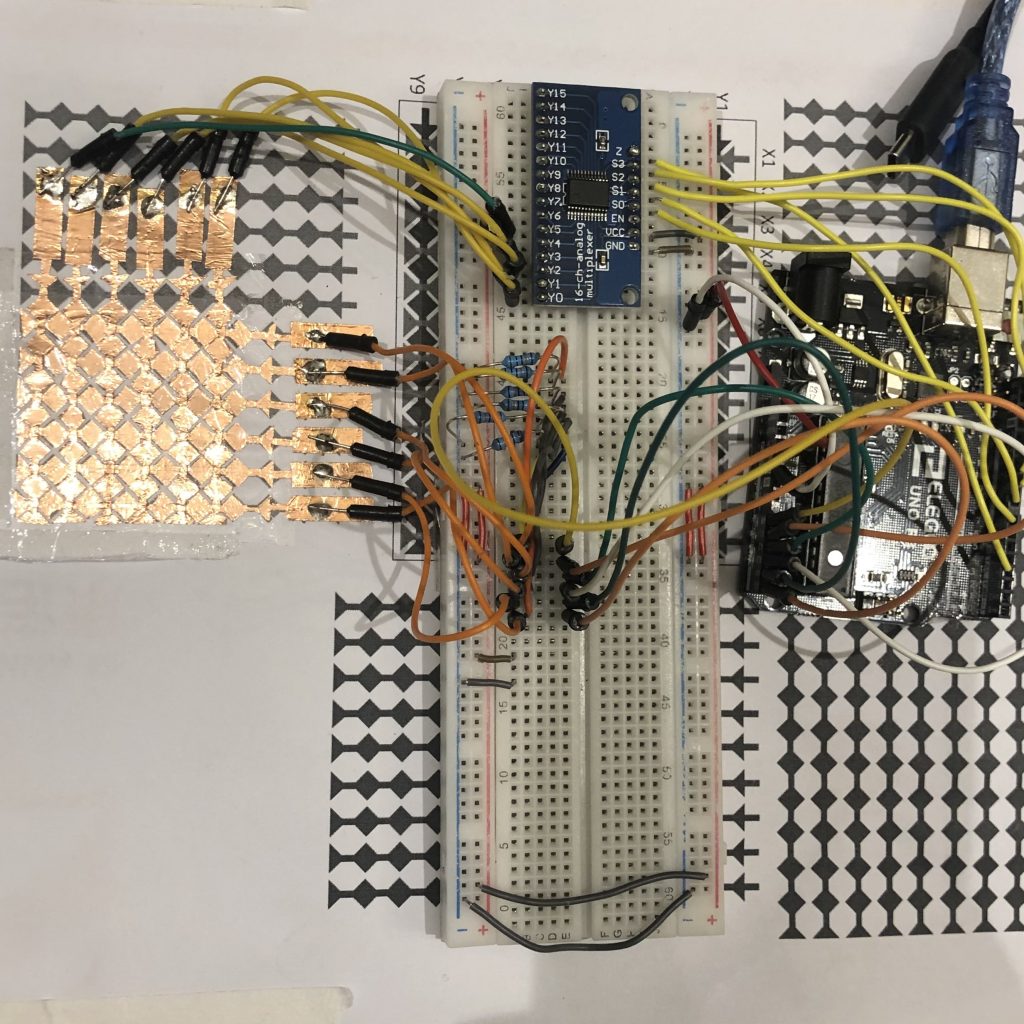
Though some issues remain:
- Touch is rarely detected with touching, and the accuracy increases with pressing. We played a little with tunable parameters and thresholds but the issue remains. We think a potential reason for it is the fabrication of the sensor grid. The 3×3 sensor we had has copper tape taped on both sides of a plastic sheet, but this 6×6 sensor has one side on paper, a plastic sheet layered on top of the bottom sheet, and the second layer of copper tape taped on top of the plastic sheet.
- Multitouch is far from robust. Again, we think the fabrication could be the issue. Because we have to press hard on the grid to get a detection, it was difficult to have a single contact point from a single touch.
- Sliding/stroking behavior does not appear obvious. We think one reason could be with sliding/stroking, the finger stays on one contact position for too short a period of time, so we need to go back and look at the paper again for more information. And similarly, the fabrication could cause the issue.
Action item for next week:
- Remake the 6×6 grid using the 3×3 method for a more robust sensor grid
- Look at the paper again
- Decide on what gestures can be detected
Four week plan
Week | Goals |
4.12-4.18 | Decide on what gestures can be detected |
4.19-4.25 | Test sound output Decide uses of different outputs(auditory&visual) Decide sensor grid materials: conductive tape/conductive yarn |
4.26-5.2 | Start on fabricating the page from a textile learning book |
5.3-5.9 | Finish fabricating the page from a textile learning book |