“Thermoformable sheets of bioplastics will represent a resource-efficient alternative [to oil-based plastics, glass, or metal] in the future, as they combine the high malleability and recyclability of plastics with the environmental benefits of materials consisting primarily of renewable resources.” explained the project team.
The Project Team
Overview
Stuttgart University’s ITKE Institute has designed and built the ArboSkin pavilion out of 388 bioplastic pyramids. A 140-square foot digitally fabricated mock-up composed of recyclable components that can be freely shaped and manufactured as 3D façade elements, the project was created within the Institute’s Bioplastic Façade Research Program to demonstrate the aesthetic and structural potentials of bioplastics.

About the Creators
ITKE is the Institute of Building Structures and Structural Design in Stuttgart, Germany. Bioplastics are plastics made from renewable biomass sources such as starches, cellulose or other biopolymers, that offer sustainable alternatives to plastics derived from fossil fuels. The bioplastic used in the ArboSkin project is called Arboblend and is produced by German firm, Tecnaro, by combining different biopolymers such as lignin – a by-product of the wood pulping process – with natural reinforcing fibres.
Collaborating materials scientists, architects, product designers, manufacturing technicians, and environmental experts were able to develop a new material for facade cladding which is thermoformable and made primarily (>90%) from renewable resources. I admire the interdisciplinary approach to this project.
Process and Project Details
The blueprint of the shell structure is based on a network of triangular shapes of different sizes. The double curved skin is made of 3.5 mm thick bioplastic pyramids that are mechanically assembled to create the free form surface. The bioplastic sheets can be freely shaped and adapted to fit any requirement for building exteriors.
Personally, what really inspired me is the fact that waste produced during the CNC milling process can be regranulated and reused to create more of these façade elements in 3D format.

The double-curved skin is formed by linking the pyramids together, with bracing rings and joists helping to create load-bearing walls. CNC-milling was used to remove sections from some of the modules, creating apertures in the facade, which I believe can be really cool if it is done based on sun data allowing for shading/sunlight during certain times of the day.
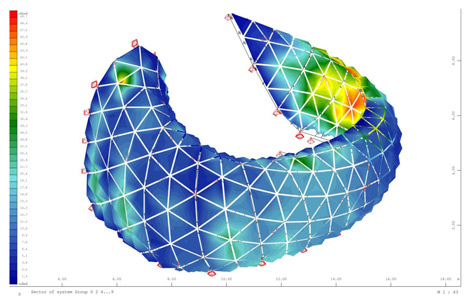
Notes:
Duration of the project: December 20, 2011 – October 31, 2013
Mock-Up: The bioplastics facade mock-up was created within the framework of the Bioplastic Facade Research Project, a project supported by EFRE (Europäischer Fonds für Regionale Entwicklung / European Fund for Regional Development). It demonstrates one of the possible architectural and constructional applications of bioplastic materials developed during the course of the project. The blueprint is based on a triangular net composed by mesh elements of varying sizes.
Links:
ITKE Constructs New ArboSkin Pavilion with 388 Recyclable Bioplastic Pyramids
ArboSkin pavilion made from bioplastic by ITKE
ArboSkin: Durable and Recyclable Bioplastics Facade Mock-Up