This week, I chose to explore the world of parametric design and crafting by looking into artist Jimmy Jian‘s ceramic pieces. He creates a variety of ceramic containers through 3D modeling. Using Grasshopper (a Rhinoceros 3D plugin), he is able to produce many iterations of whichever design he is working on at the moment. What I appreciate most about his pieces are the elegant, repeating qualities they have, simplistic in form but complex by nature.
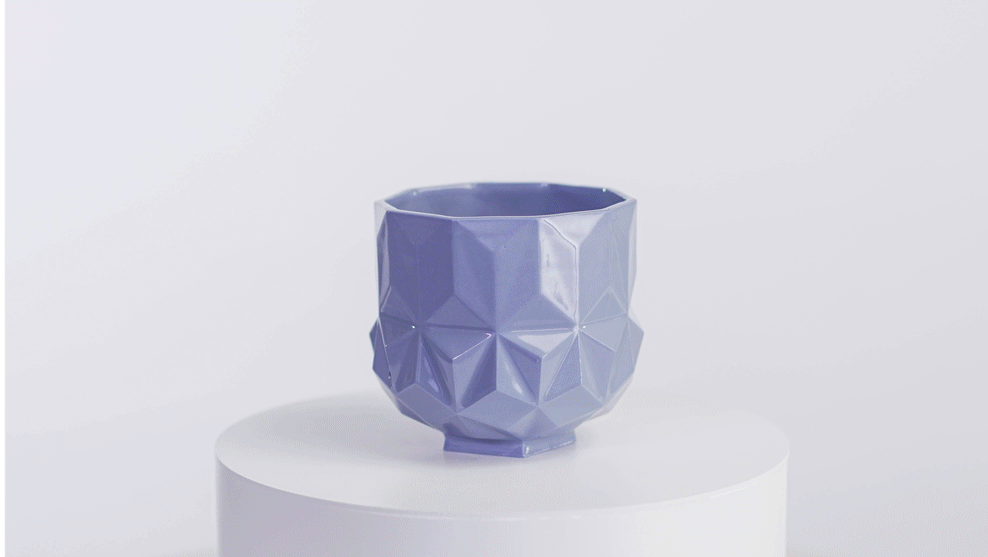
Jian’s process involves first modeling the forms using Grasshopper. Then, using a 3D printer, he is able to print out the forms to a very high degree of accuracy. Those forms are then inserted into plaster to create molds, which are then used to slip-cast the ceramic pieces. The resulting pieces are then glazed in various colors and fired. This workflow allows Jian to replicate the pieces in any number he wishes, as long as he keeps the mold intact. The artist’s sensibilities show in the color of the glazes he uses, keeping to shades of blue and blue-green. He also seems partial to subtle, repetitive patterns.
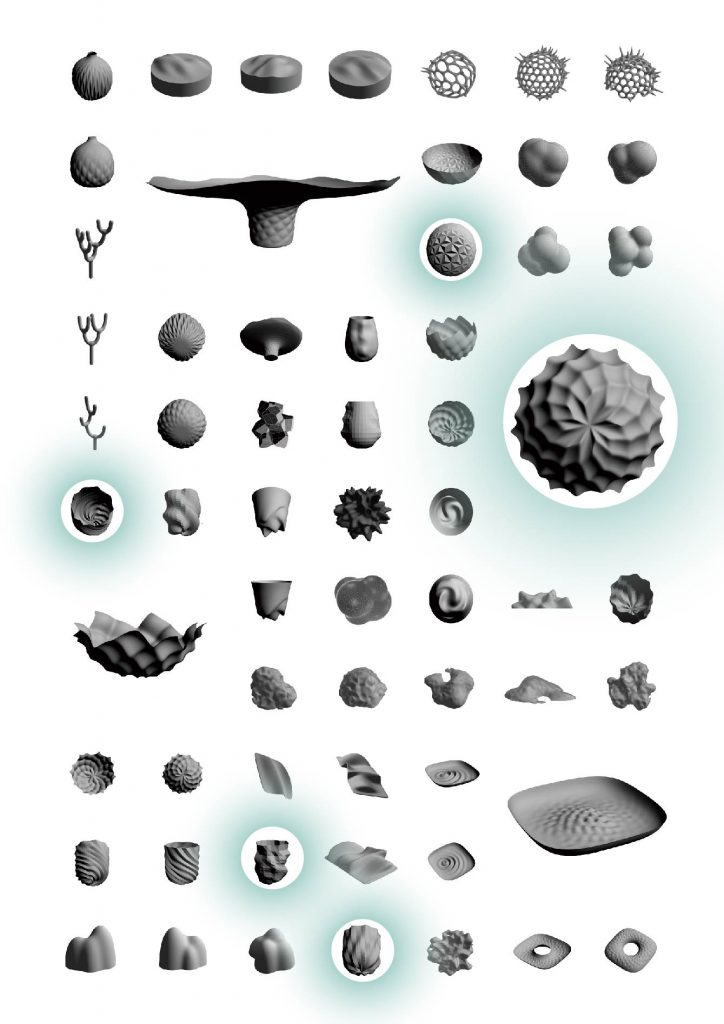
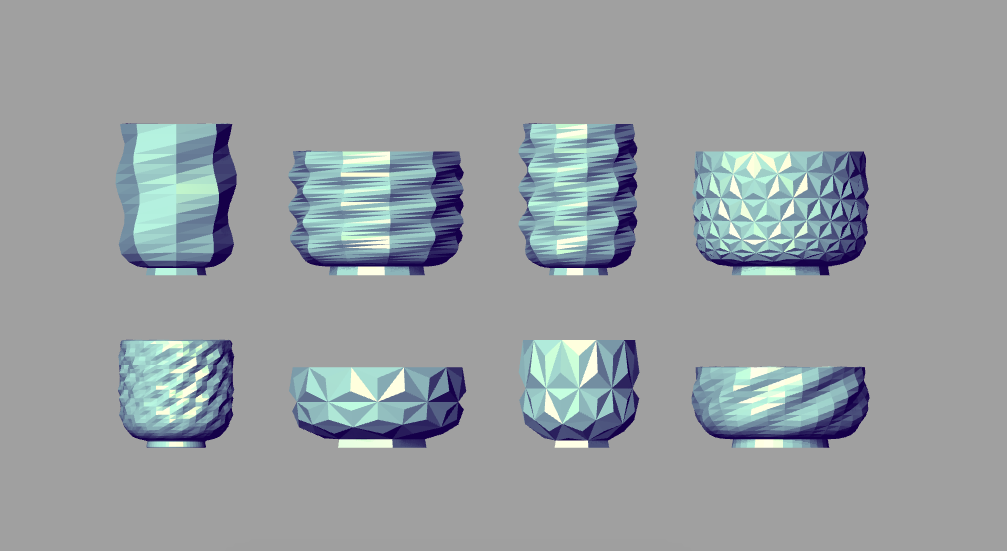
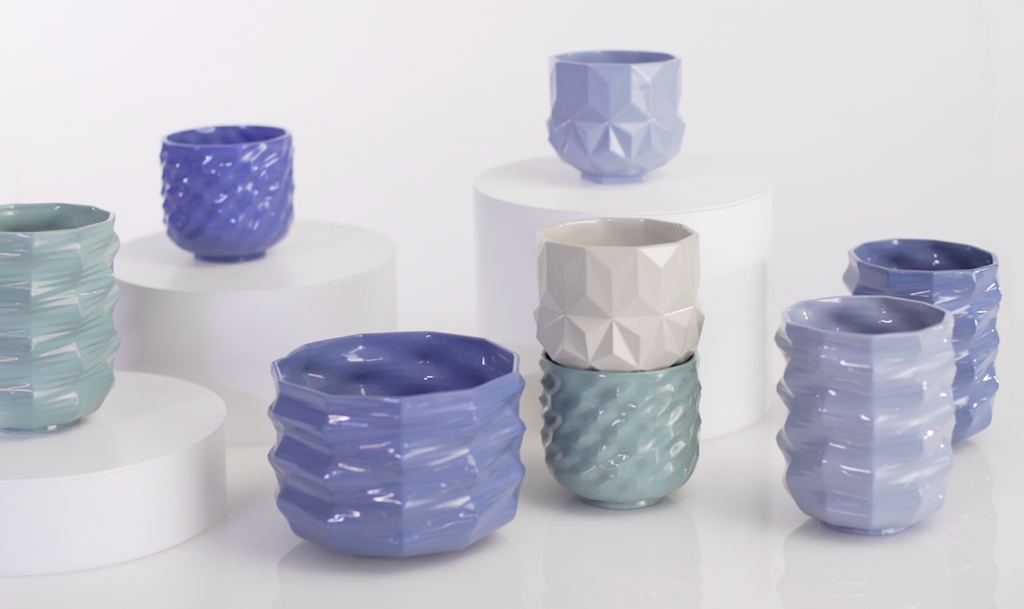