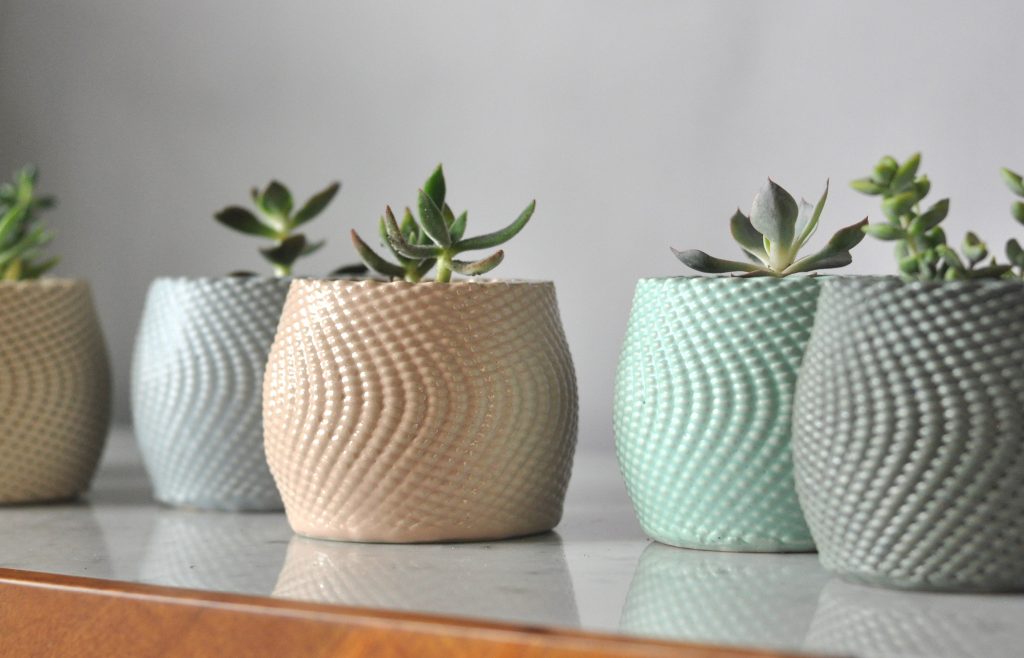
Coded Clay is a project and business where 3D parametric fabrication creates pots and vases for people to use in their homes. This project is particularly interesting because code is used to alter every aspect of the 3D printing process to create unique vases. The 3D printer is also custom built to be able to print clay after using parametric coding in grasshopper.
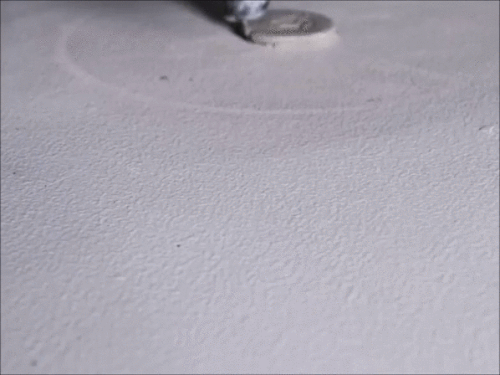
The process taken to create the pots starts by a sketch idea of a form/shape. Then by the use of parametric coding in grasshopper, the forms are digitally modified until the desired aspects of the pot are met. Lastly, the pots are 3D printed, fired twice, and hand glazed. Brian Peter is the creator of these and he if interested in both computational architecture as well as pottery. He went to undergrad for Studio Art and completed a ceramic residency – where the 3D printed clay idea started.
