Zaha Hadid Architects created a gallery that is now displayed as The Winston Gallery in London’s Science Museum. The Handley Page aircraft is placed in the center of the artpiece while a three-dimensional pod structure curves around it. The design of the creation imitates the movement of airflow used throughout aviation industry history. I admire how the piece encapsulates the entire room and draws your eyes up towards the ceiling. I also admire the fact that the context behind this piece is deeply rooted in history and mathematics. Mathematics has allowed for the progression of the society that we know today, solving the world’s biggest problems and allowing us to advance.
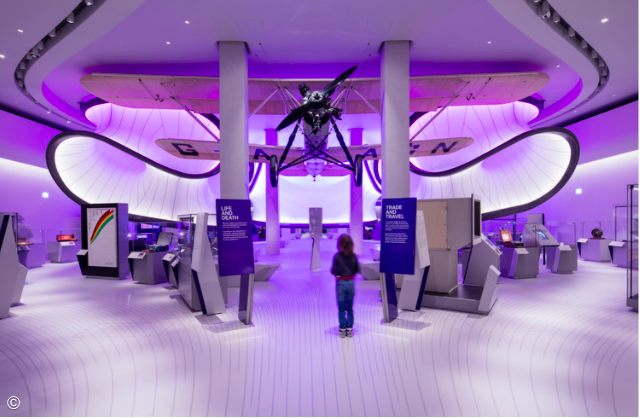
Mathemiticians and engineers used mathematical models in wind tunnels to design new aircraft. Similarly, the creators of the artpiece had the actual aircraft. They used it to construct the geometry of the gallery and the airflow that would have followed the aircraft.
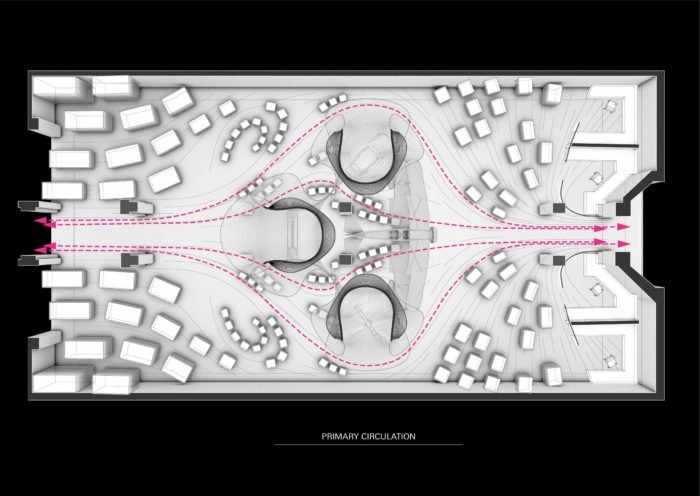
The creator’s artistic sensibilities manifest in the final form with a very elegant design. Dame Zaha Hadid, who was known for her use of curves, designed the smooth, curving surfaces and soft contour lines throughout the gallery.