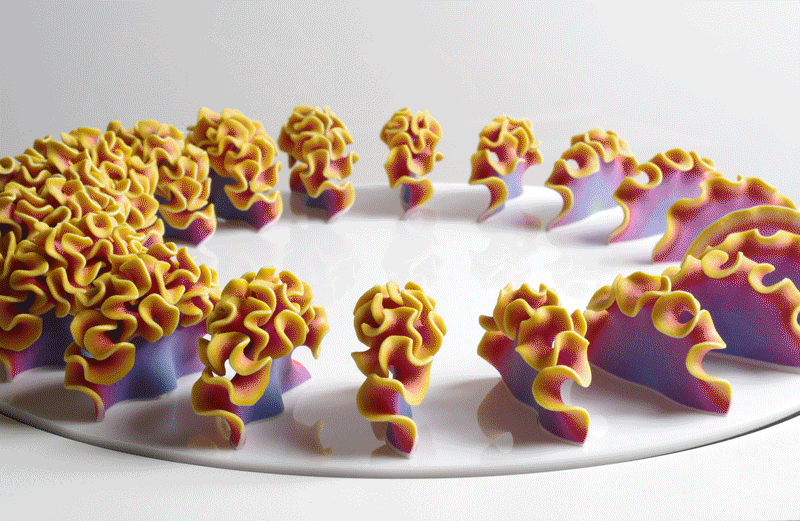
“Fluorescence Zoetrope” is a 3D printed sculptural animation piece created by the design firm Nervous System (Jessica Rosenkrantz and Jesse Louis-Rosenberg.) They 3D modeled an organic growth loop algorithmically, then PLA printed each frame. Then they mounted them onto a rotating platform to animate the form.
I am drawn to this piece because of the impressive craft involved in it. The color gradient is eye catching and perfectly smooth, and the forms themselves are incredibly high-resolution. I think this project is a testament to the level of refinement that technologies such as computer generation and 3D printed can provide at times. The algorithms used to create this project are based on natural growth processes.