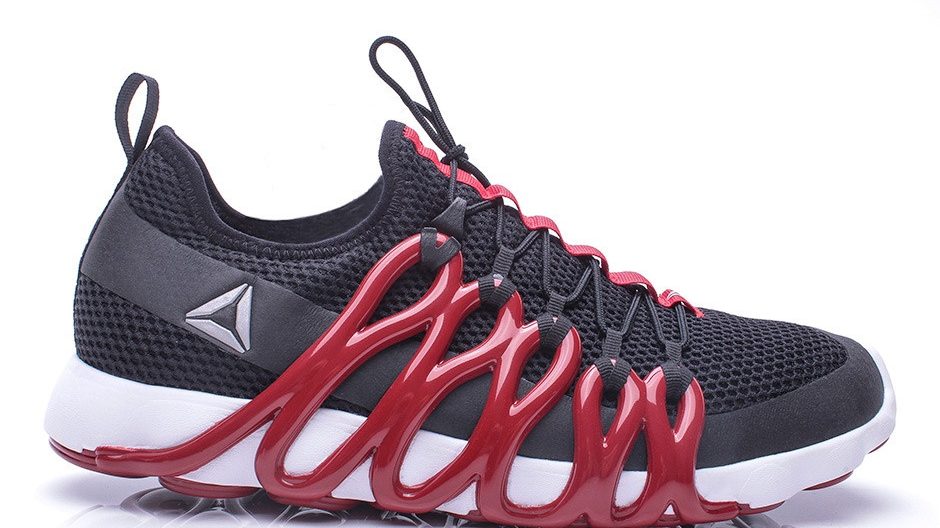
Liquid Speed is a 3d printed energy-return running shoe designed by Reebok and BASF. Printed with a special high-rebound liquid material, the outsole has wings that stretches and wraps around the side of the shoe. This gives a perfect customized fit when the shoe is laced up. What I really admire about this product is that it utilizes 3d printed material in an effective way to give the most personalized experience with the shoe. Having stretchable wings on each side of the shoe to tighten up and mold any desired foot to the shoe impresses me as a design major. The liquid factory uses state of the art machinery and software to build a system that draws the outsole of the shoe with a urethane-based liquid developed by BASF. The important part of this project is that the shoe does not need molds to be created. Molds are expensive, which is the reason why shoes are expensive in price. Developing a technology that eliminates the process of using molds is an innovative application in the shoe industry. I can see that the curvy shape of the outsole and wings give a smooth yet unique design to the shoe, while the reflective red color gives a powerful and strong emphasis to the overall design.