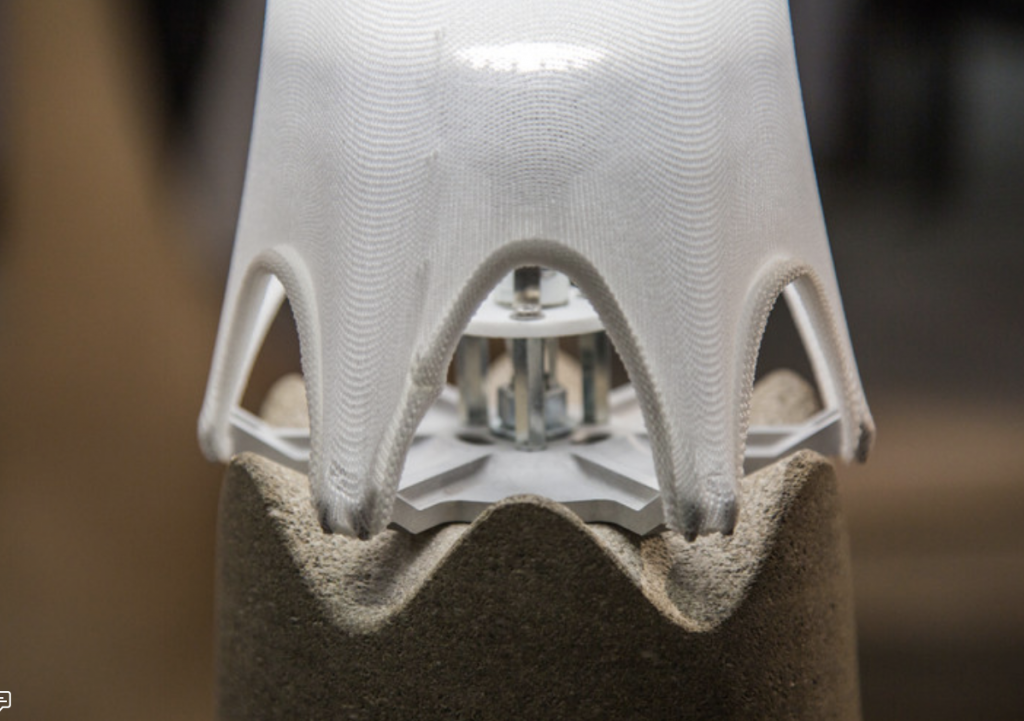
https://www.archdaily.com/804456/autodesks-generative-design-pavilion-plays-with-properties-and-fabrication-processes-in-stone-and-fabric
Autodesk’s Generative Design Pavilion was designed by architect Sean Ahlquist and research engineer Andrew Payne to explore materiality using stone and fabric. It is interesting in how it wants to compare the different material properties of stone and fabric, juxtaposing the strength of the limestone to the flexibility of the fabric, but also merge them to create similar forms. Not only was the form generatively designed, but the fabric was customized as well. Although the fabric and the stone created similar forms, the algorithms used to create them would have been extremely different. The algorithm for fabric would have worked to exploit how the fabric stretched, while the one for the stone would have worked to calculate its breaking points and subtraction of form. The designers’ artistic sensibilities arise in the final structure not only through the form, in which the completely different materials manifest the same form, but also in the joinery that connects them. Where the fabric and stone meets, they elegantly are able to describe both material properties with having the strength of the stone stretch the canopy of fabric above.