Zaha Hadid Architects generated geometry through robotic-assisted design
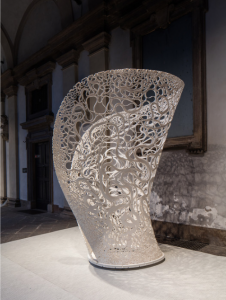
“Thallus” by Zaha Hadid Architects in Accademia di Belle Arti di Brera, Milan,Italy
Thallus is a installation being part of the exhibition “White In The City” in Milan. The exhibition explored use of white color for art and architecture in the contemporary world. The structure is 3D printed using premium polylactide plastic. I think how the shape and pattern are generated is interesting. The pattern started with simple cylinders on surface and Six-axis robotic 3D-printing technology generated one continuous stroke connecting the each cylinder, which produced “calla lily”-like geometry on the surface. The design explores how the curve is guided along the surface and change its density and size through parametric boundaries.
What is interesting about ZHA’s Thallus was use algorithmic thinking to clarify the relationship between the design intent and design response. The geometry is clearly defined by certain rules within the boundary of parametric calculation also it successfully rendered its parametric relationship with the original cylinder shape and its final calla lily-like curve.